Selecting the correct welding rod for stainless steel, particularly 304 stainless steel, plays a crucial role in ensuring a strong, durable weld. 304 stainless steel, known for its excellent corrosion resistance and good formability, is widely utilized across various industries, from the production of kitchenware to the construction of architectural paneling. However, welding this ubiquitous alloy requires specific expertise and understanding of the welding rods best suited for it.
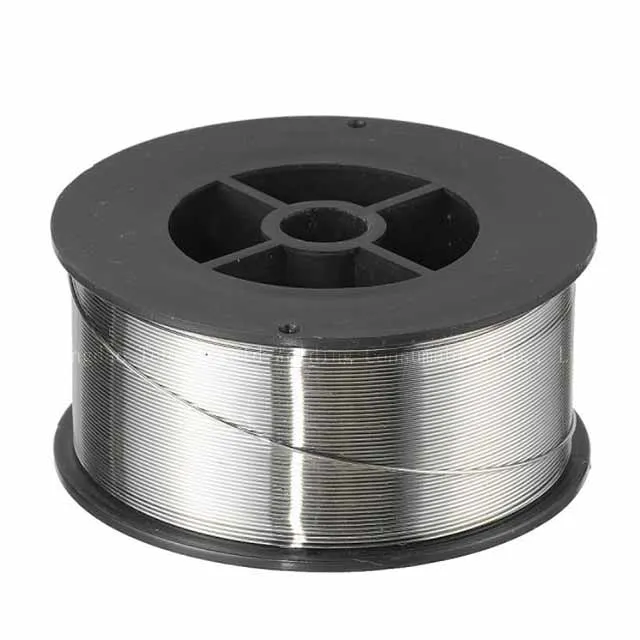
When welding 304 stainless steel, the most recommended welding rods are those composed of 308L or 308. The L in 308L denotes a low carbon content, which minimizes the risk of carbide precipitation, a common problem in stainless steel welding. Carbide precipitation occurs at temperatures between 425°C and 870°C, leading to intergranular corrosion and potentially compromising the structural integrity of the weld. Thus, using 308L rods often aids in maintaining the corrosion-resistant properties of the base metal, a vital factor in stainless steel applications.
A key experience factor when working with 304 stainless steel is understanding the specific challenges posed by its composition. This alloy mainly comprises chromium and nickel, improving its resistance to oxidation and corrosion. However, these elements also make the welding process challenging because they can lead to the formation of a brittle microstructure in the heat-affected zone. Therefore, an authoritative approach involves adopting a balanced heat input and ensuring adequate post-weld cleaning to maintain the desired mechanical properties.
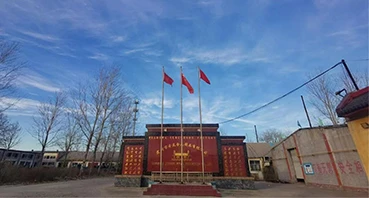
Expert opinions often highlight the importance of controlling temperature during the welding process. An experienced welder will always avoid overheating the 304 stainless steel, as excess heat can compromise its physical properties. The use of 308L welding rods supports this endeavor by requiring lower heat inputs due to their efficient melting characteristics. The result is a clean, well-fused weld with minimal distortion of the metal.
304 ss welding rod
Another authority aspect in choosing 308L rods is their applicability in different welding methods, such as TIG (Tungsten Inert Gas) and MIG (Metal Inert Gas) welding. TIG welding, in particular, benefits from the consistency and precision of 308L rods, making it ideal for welding thin sections of stainless steel with an aesthetically pleasing finish. MIG welding, on the other hand, can utilize 308L wires for thicker applications, providing strong and reliable connections capable of withstanding considerable stress.
The adoption of appropriate safety practices further enhances trustworthiness and reliability when welding 304 stainless steel. Welders should equip themselves with proper protective gear, including masks and gloves, to prevent exposure to harmful fumes and intense light. Ensuring a well-ventilated work environment is another critical step in safeguarding health and ensuring high-quality welds.
Finally, the consistent performance of 308L welding rods in both domestic and industrial applications highlights their recommended status among welding professionals. Continuous advancements in rod composition and manufacturing techniques promise to enhance the effectiveness and efficiency of welding processes involving 304 stainless steel, solidifying the reputation of 308L rods as a trusted solution.
In summary, the choice of 308L welding rods for welding 304 stainless steel is supported by expert insights and real-world experiences. Their low carbon content and adaptability to various welding methods (such as TIG and MIG) ensure durability, corrosion resistance, and professional-grade results. Welding professionals consistently emphasize the importance of correct rod selection, showcasing the profound impact of this decision on the longevity and reliability of stainless steel structures.