Welding, a crucial skill in the construction and manufacturing industries, requires precision and the appropriate tools. Among the myriad of welding rods available, the 7018 welding rod stands out as a reliable choice for professionals seeking strength and durability. Understanding its applications and unique characteristics is essential for achieving optimal results.
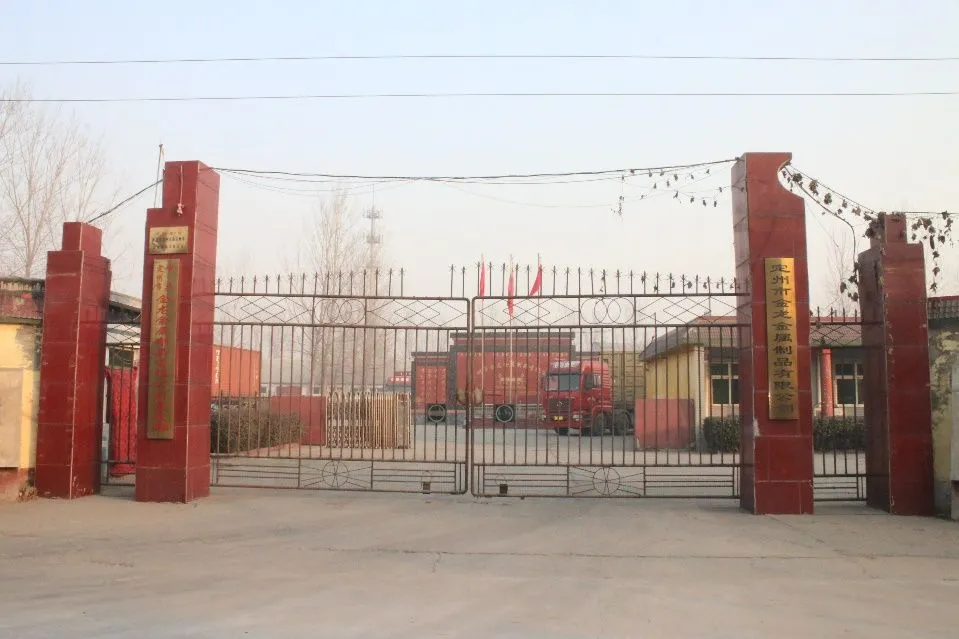
7018 welding rods are often categorized under low-hydrogen electrodes, which are designed to produce high-quality welds with minimal imperfections. Their low-hydrogen characteristics make them indispensable in scenarios where crack prevention is paramount. These electrodes are primarily used in structural steel welding, offering an exceptional balance between strength and ease of use.
The unique composition of the 7018 rods comprises an iron powder coating which contributes to the rod's distinctive properties. This coating not only facilitates a smooth arc that's easier to control but also ensures a cleaner weld. It's particularly beneficial when dealing with higher tensile strength steels, where maintaining the integrity of the weld is critical. The rod’s coating enhances its performance, ensuring that each weld has a consistent finish and exceptional mechanical properties.
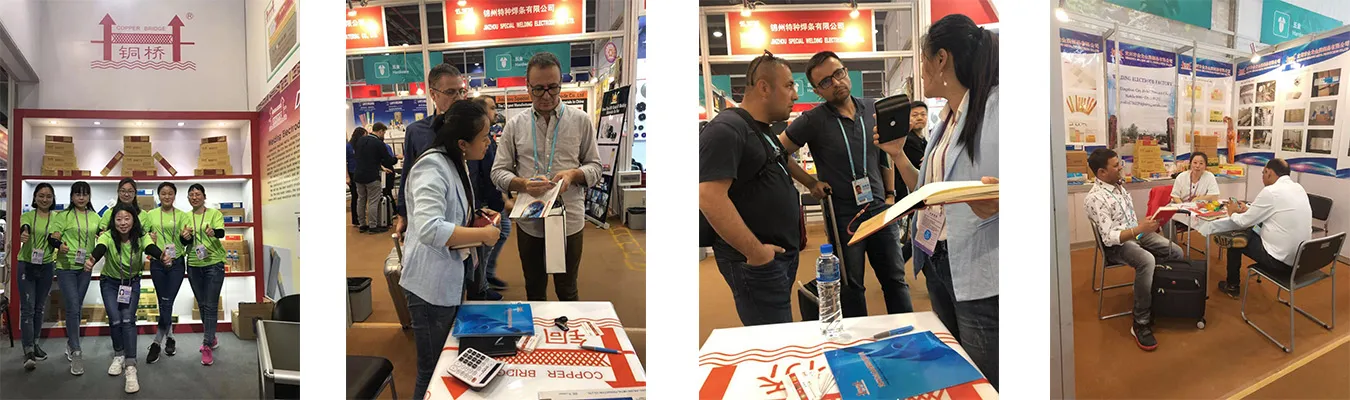
One of the key advantages of using 7018 welding rods is their versatility. These electrodes can be used in all positions, whether flat, horizontal, vertical, or overhead. This flexibility is a significant asset on construction sites, where welders often have to adjust their techniques on the fly. Such adaptability ensures that the 7018 welding rod remains a staple in both small-scale projects and large-scale infrastructure developments.
In terms of strength, the 70 in the 7018 designation indicates the minimum tensile strength the rod can withstand, measured in thousands of pounds per square inch. Thus, 7018 welding rods provide a robust result, capable of handling a tensile strength of up to 70,000 psi. Coupled with the “18” which signifies low hydrogen content and iron powder in the composition, these rods deliver a resilient and reliable weld, less prone to defects like porosity or cracking.
what are 7018 welding rods used for
Applications of 7018 rods are varied, ranging from the routine repair of machinery and automotive parts to more demanding tasks in bridge construction, shipbuilding, and the erection of high-rise buildings. Their ability to produce sound welds in critical structural applications makes them a favorite among engineers and welding specialists who need assurance of both performance and safety.
Another noteworthy feature of 7018 welding rods is their comparatively low sensitivity to impurities and dirt on the welding surface. While it's always best practice to clean the metal surfaces, these rods can tolerate minor contaminants than other electrodes might not, making them highly practical in environments where perfect surface preparation is challenging. This trait underscores their reliability in adverse conditions, such as outdoors or in less-controlled manufacturing environments.
Although these rods offer numerous advantages, proper storage is vital to maintaining their low-hydrogen characteristics. Exposure to moisture can compromise the rod’s efficiency and weld quality, leading to potential defects. It's recommended that 7018 rods be stored in sealed containers and kept in warm, dry conditions or even in dedicated rod ovens until used.
In conclusion, 7018 welding rods are a testament to both innovation and tradition in the welding industry, combining the best elements of usability, strength, and reliability. Their role in ensuring the structural integrity of countless projects around the world cannot be understated. For those in the welding profession, mastering the use of the 7018 is a step toward achieving exemplary results, representing both personal expertise and contributing to the overarching trustworthiness and credibility of the projects they work on.