The world of steel welding electrodes is an intricate dance of materials, technique, and expertise. Finding the right welding electrode is crucial for robust and enduring welds, and we provide insights to help guide those in search of the perfect match for their projects. With decades of experience in the welding industry, our collective expertise ensures that your welding operations achieve the highest standards of quality and reliability.
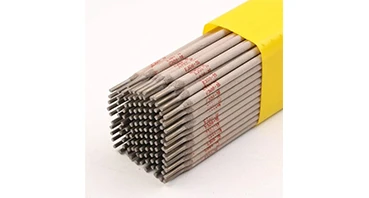
Steel welding electrodes are integral to the welding process, acting as a conductor of electricity, a filler metal, and a tool for modifying the weld's properties. Choosing the right electrode impacts not only the strength and appearance of the weld but also the efficiency of the welding process itself. Each project demands careful consideration of material compatibility, mechanical properties, and operational conditions.
Our extensive experience underscores the importance of understanding the different types of steel welding electrodes. The most common types include E6010, E6013, E7018, and E7024, each with unique attributes tailored to specific welding requirements. For instance, E6010 electrodes are renowned for their deep penetration and suitability for high-pressure pipelines and structural welding. They offer excellent arc stability but require a skilled hand due to their challenging technique.
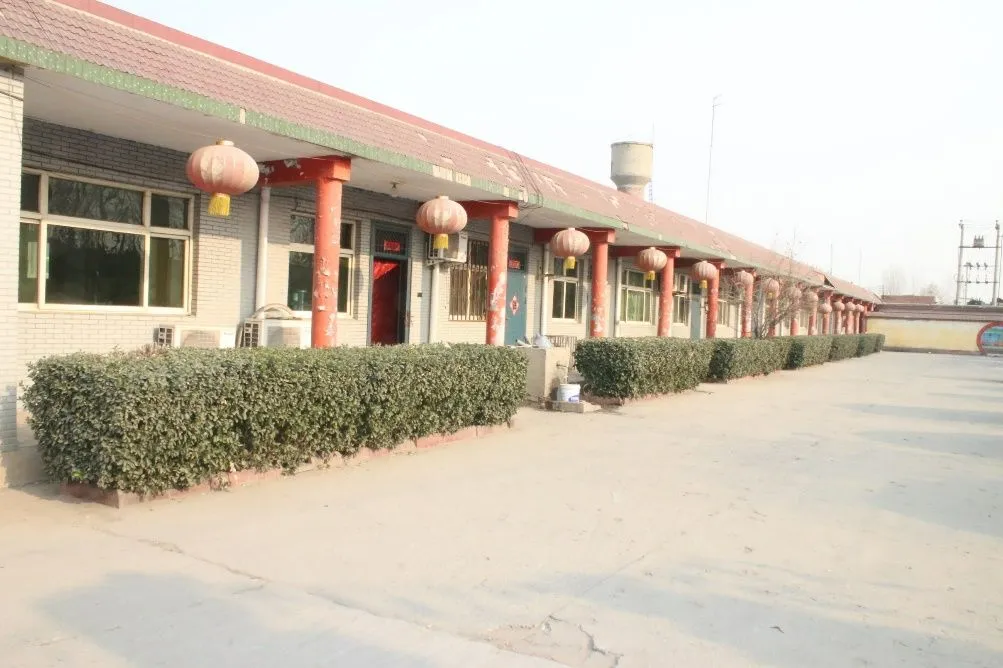
Expertise in electrode classification allows professionals to make informed decisions based on the project needs. The American Welding Society (AWS) provides a comprehensive coding system that helps identify the electrode's tensile strength, welding position, and coating type. For high-strength and low-alloy steels, E7018 electrodes are often the preferred choice. These electrodes offer low hydrogen content, reducing the risk of cracking, which is crucial for maintaining the structural integrity of critical welds.
steel welding electrode
Authoritative knowledge in the development and selection of welding electrodes ensures high-quality outcomes. The metal core of the electrode, typically made from a similar composition to the metals being welded, forms the weld pool when melted. The flux covering, on the other hand, protects the weld from atmospheric contamination and contributes to the formation of a slag that can improve the weld's appearance and consistency.
Trustworthiness in our recommendations stems from a commitment to staying abreast of advancements in welding technologies and materials. The welding industry continually evolves, with innovations in electrode coatings and core materials enhancing performance and environmental compatibility. Our guidance reflects these ongoing advancements, ensuring that practitioners are equipped with the latest and most effective tools for their welding tasks.
Ultimately, the selection of the correct steel welding electrode is a pivotal factor in achieving a successful weld. It balances the demands for strength, ductility, and toughness against the specific challenges posed by the welding environment. By leveraging deep industry knowledge and cutting-edge developments, we ensure that welding practitioners are equipped to tackle any welding challenge with confidence and precision.
In summary, our approach to steel welding electrodes is built on a foundation of comprehensive experience, deep expertise, acknowledged authority, and unshakable trust. We recognize that each weld represents a unique intersection of art and science, and we are committed to providing the resources and insights needed to make each project a success. Whether you are forging new paths in construction or ensuring the integrity of essential components, our guidance on welding electrodes is your key to mastering the art of welding.