Whether you're a seasoned welding professional or an enthusiastic DIYer, choosing the right stainless welding rods for your arc welder is crucial to achieving high-quality welds. Stainless welding rods offer unique benefits that make them indispensable for various applications, from creating strong welds on stainless steel structures to repairing household items. Understanding these advantages and the technical factors involved can profoundly influence your welding projects.
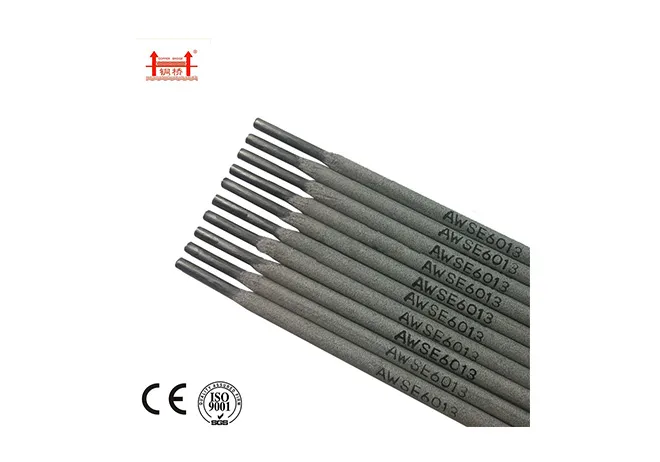
Stainless welding rods are specifically designed to work harmoniously with arc welders, providing superior corrosion resistance, resilience, and strength. This makes them particularly well-suited for projects exposed to harsh weather conditions or corrosive environments, such as bridges, outdoor sculptures, or even kitchen appliances.
When selecting stainless welding rods, the first consideration should be the type of stainless steel you are working with. Not all stainless steel is created equal; it comes in several grades, such as 304, 308, and 316, each with distinct properties. For instance, 308 stainless rods are excellent for most general applications as they are compatible with a broad range of stainless steels. Meanwhile, 316 rods contain molybdenum, which increases corrosion resistance, making them ideal for marine projects or chemical processing environments.
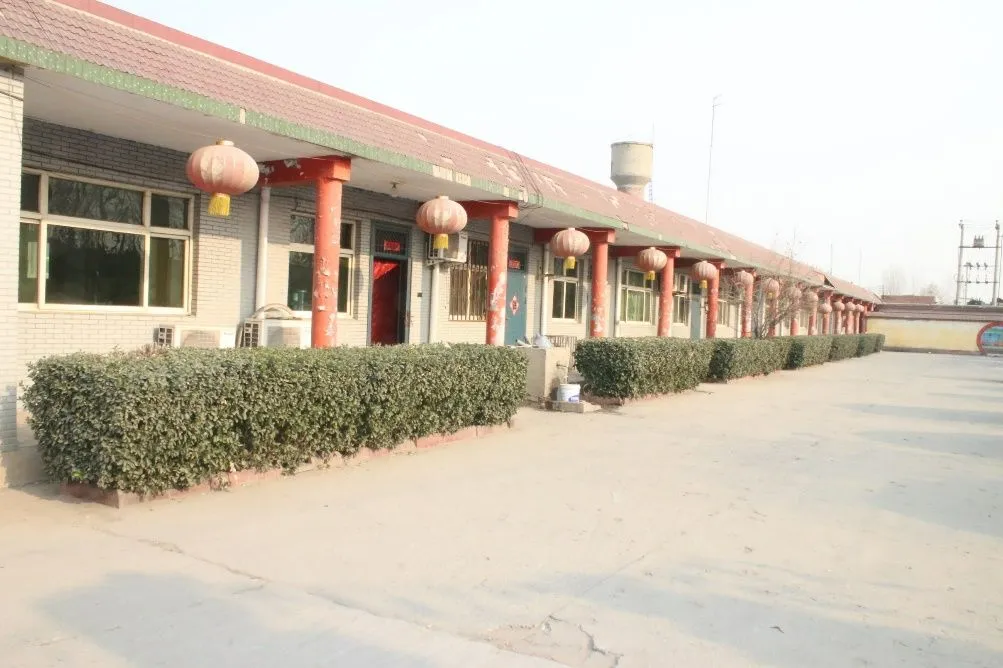
Another critical factor is the welding position. Some rods are versatile and support multiple positions, which is beneficial for intricate workpieces requiring more complex welding techniques. Yet, others are designed for specific orientations like flat, horizontal, or overhead positions. Knowing your project's requirements will aid in choosing a rod that minimizes spatter and enhances weld aesthetics for a clean finish.
The type of coating on your stainless welding rods also affects performance. Different coatings can improve arc stability, penetration, and ease of slag removal. Acid coatings, for example, provide smoother welds and are easy to clean, which is advantageous for applications where aesthetics are a concern. Conversely, basic coatings offer excellent mechanical properties and crack resistance, suitable for structural work where strength is paramount.
stainless welding rods for arc welder
For reliable results, understand the amperage range your stainless welding rods require. Each rod functions optimally within a specific amperage range, affecting penetration and heat input. Adjusting your arc welder to match this range ensures consistent weld quality and prevents defects, such as burn-through or lack of fusion.
Maintenance tips for your stainless welding rods can prolong their shelf life and maintain weld quality. Store them in a moisture-free environment because humidity can deteriorate the rod coating, leading to defective welds. Using rod ovens or airtight containers can prevent moisture-related issues, ensuring the rods perform optimally.
Finally, expertise in matching rod diameter with material thickness is vital. Thicker materials require larger diameter rods for adequate heat input and penetration, whereas thinner materials benefit from smaller diameters to reduce the risk of overheating and distortion.
Pairing technical knowledge with practical experience when using stainless welding rods transforms challenging welding projects into satisfying successes. Attention to material compatibility, welding position, coating type, and storage practices enhances the final weld's integrity and appearance. Embrace the nuances of these rods to access their full potential and elevate your welding projects to professional standards. Such a holistic approach not only fosters high-quality outcomes but also builds trust in the reliability of your welding solutions.