Understanding the nuances of selecting the right stainless steel welding rod is crucial for ensuring the quality and longevity of any welding project. This steel category is revered for its resistance to corrosion, heat, and chemical damage, making it a popular choice for various industrial applications. For experienced welders and novices alike, referring to a stainless steel welding rod chart can be incredibly beneficial.
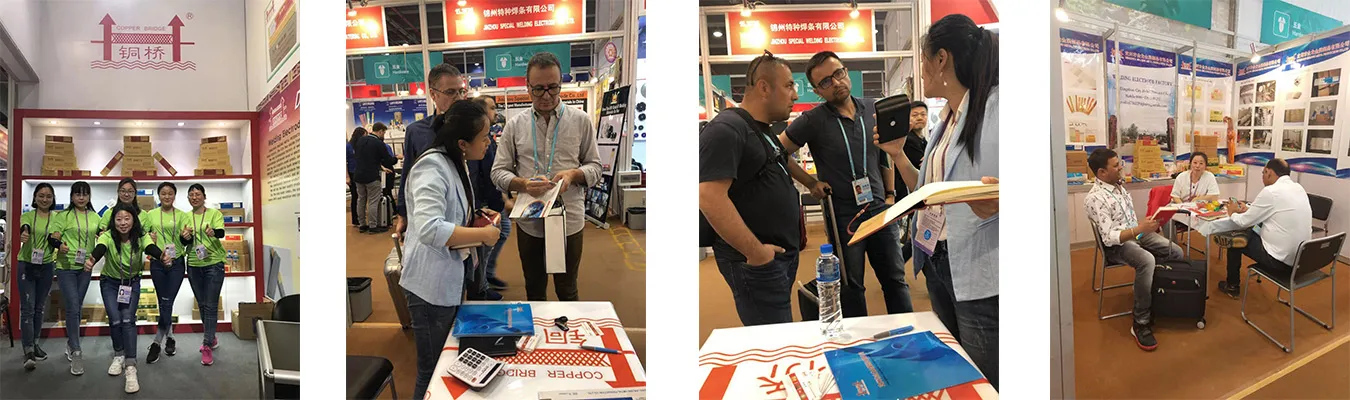
Choosing the correct welding rod begins with understanding the different types of stainless steel rods available. Stainless steel rods are primarily categorized based on their chemical compositions which directly influence their application and performance attributes.
1.
Austenitic Stainless Steel Rods
These rods are perhaps the most commonly used. Known for their excellent corrosion resistance and superior workability, they are ideal for projects requiring resilience in challenging environments. Grades such as 308, 309, and 316 reflect varying proportions of chromium, nickel, and molybdenum to meet specific needs. For instance, a 316-grade rod is typically used in marine or chemical processing applications due to its superior corrosion resistance.
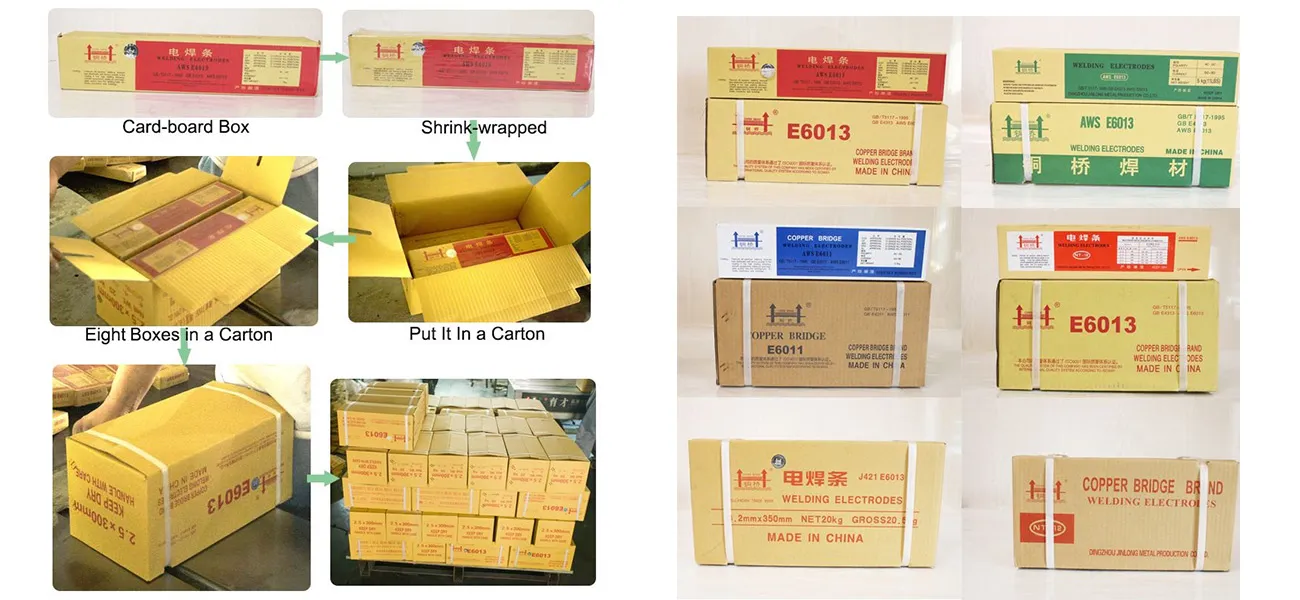
2. Ferritic Stainless Steel Rods
Typically less ductile than austenitic rods, ferritic stainless rods offer high resistance to stress corrosion cracking. For applications that demand enhanced resistance to oxidation and thermal fatigue (such as exhaust systems), these rods come into play. Examples include the 409 and 430 grades, which are utilized in automotive and kitchenware products.
3. Martensitic Stainless Steel Rods
Known for their high strength and moderate corrosion resistance, martensitic rods are often used in applications demanding high wear resistance and low thermal expansion. These rods offer the benefits of hardened and tempered steel making them suitable for the production of cutlery and surgical instruments.
A comprehensive understanding of the welding environment is also essential to rod selection. Factors such as the welding process (MIG, TIG, or stick), the position of the weld, and the base metal's thickness and specification play pivotal roles in which rod to choose.
stainless steel welding rod chart
For instance, in situations requiring TIG welding, such as automotive bodywork or food processing equipment manufacturing, the TIG process accommodative the use of thinner materials and often calls for rods that provide clean, precise welds (like the 316L grade for exceptional resistance against chemical threats).
Understanding the welding chart isn’t just about matching numbers, though. It requires an appreciation of how these rods perform during the process. Welders need to consider deposition rates, post-weld treatments, and potential exposure conditions. For heavy fabrication, wherein structural integrity is paramount, choosing a rod based on the tensile strength and ductility provided by the chart ensures that parts meet operational expectations without premature failure.
In industries such as petrochemical processing or power generation, where high pressure and temperature ratings are common, using a well-suited welding rod mitigates risks associated with part deterioration over time.
Given the integral role these rods play, leveraging the advices of expert metallurgists can amplify one's comprehension of the chart. These professionals provide insights drawn from rigorous testing and vast industry experience, ensuring the most informed rod choice possible.
This wealth of knowledge becomes significantly crucial when dealing with advanced alloys or when transitioning between different material compositions. Stainless steel welding rod charts, when interpreted correctly, can be invaluable tools, offering welders the roadmap needed to achieve robust, efficient, and safe outcomes.
Ultimately, the trustworthiness of a project's outcome is directly linked to the careful cross-referencing of material specifications with practical, tested parameters offered in these charts. When embraced alongside prudent craftsmanship and technology, these rods uphold the enduring principles of precision and reliability.