Selecting the appropriate size of stainless steel (SS) welding rod is crucial for ensuring the quality and durability of welds in various fabrication projects. With years of experience in welding and a thorough understanding of the nuances involved, I've consolidated essential insights that can help both professionals and learners make informed decisions. This discussion encompasses practical experiences, expert tips, authoritative guidelines, and trustworthy advice concerning SS welding rod sizes.
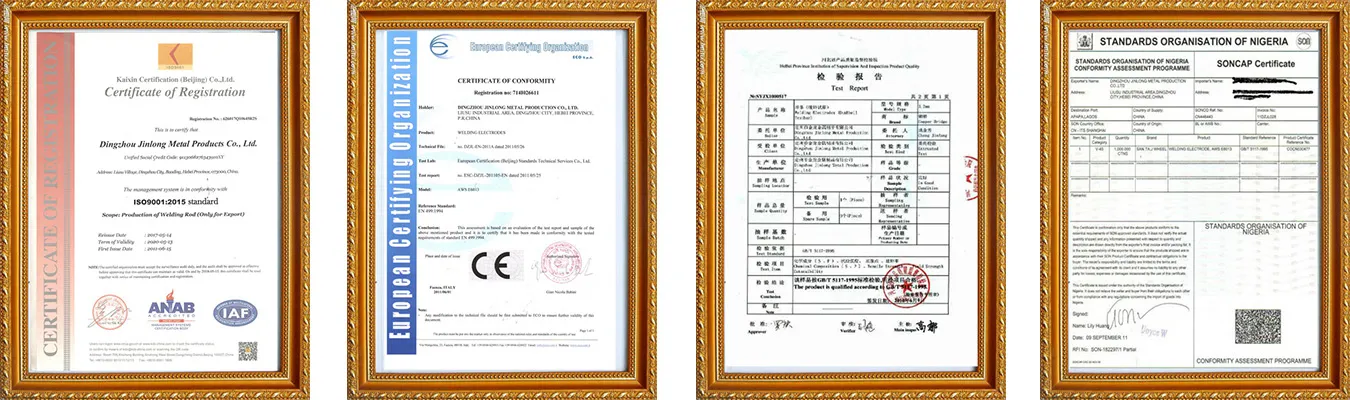
Understanding stainless steel welding is akin to mastering an art. The finer the details attended to, the more superior the outcome. One of the primary considerations is the diameter of the welding rod, which significantly influences the welding process and outcome. A well-chosen size ensures stronger welds, reduces material wastage, and minimizes defects. These insights stem from decades of firsthand interactions with folks in the field who have perfected the art of welding stainless steel.
The size of the welding rod you choose is generally determined by the thickness of the material being welded. For instance, a basic rule of thumb in professional welding circles is that the rod thickness should be approximately the same as the material thickness to ensure strong and consistent welds. If you're welding a stainless steel sheet that is 3mm thick, opting for a 3mm welding rod is ideal. This alignment prevents issues that commonly surface when the rod is too thin, leading to weak welds, or too thick, causing unnecessary burns and distortions.
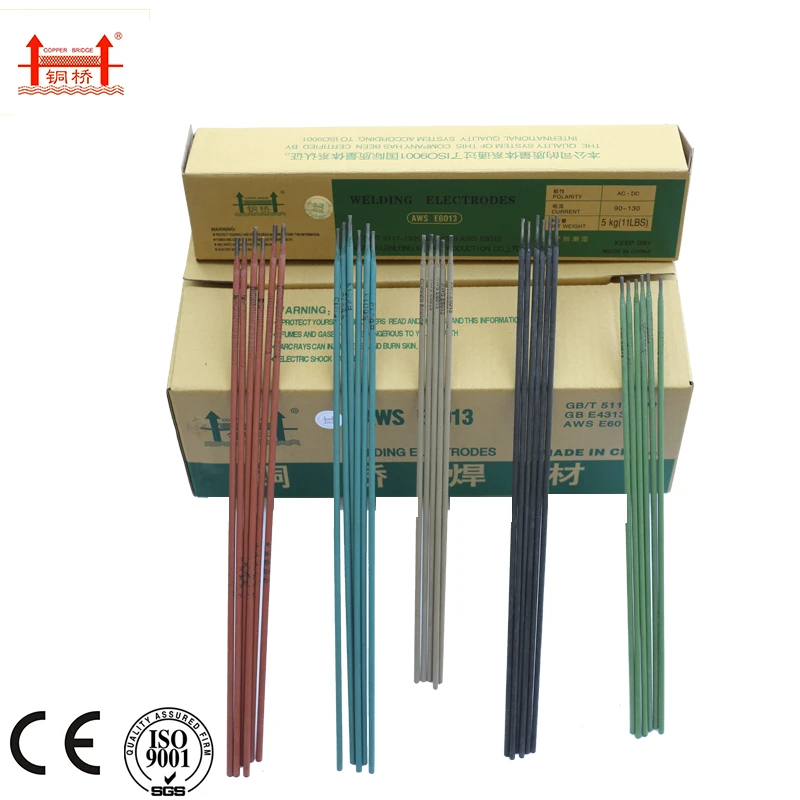
However, real-world scenarios often demand more nuanced considerations. Professional welders, for instance, might opt for a slightly thinner rod when the welding task involves intricate or detailed work, allowing for more control and precision. Conversely, thicker rods might be utilized for welding heavier, bulk materials to provide the necessary weld pool without extensive filler material.
The choice of rod size also hinges on the welding process employed. Techniques such as TIG (Tungsten Inert Gas) and MIG (Metal Inert Gas) have varied rod and wire size requirements due to their specific characteristics. Expert welders know that in TIG welding, smaller diameter rods are typically used to provide better control over the weld pool, catering especially to delicate and fine welding tasks. Whereas in MIG welding, the wire is fed automatically, and the selection of wire thickness is guided by machine settings and the thickness of the material.
ss welding rod size
Beyond the technicalities of size, the expertise extends to understanding the alloy composition of the SS welding rod itself. Familiarity with the base metals in the project ensures compatibility, minimizing issues such as corrosion, porosity, and cracking. For example, using a 308-grade stainless steel rod is advisable for welding 304 stainless steel base metal. Such attention to detail is a hallmark of skilled professionals aiming to achieve seamless, durable, and aesthetically pleasing welds.
Incorporating state-of-the-art welding equipment also plays a significant role in optimizing the use of different rod sizes. Advanced welding machines now include functions that automatically adjust settings based on rod diameter, thereby reducing human error and enhancing weld quality. Those experienced in the field recommend leveraging these technologies to complement traditional skills, ensuring efficiency and precision.
Ultimately, selecting the right SS welding rod size is about harmonizing the material's needs with the welder's technique. Proper training and continued learning are key to mastering this skill. Many industry veterans advocate for hands-on practice and learning from seasoned welders to gain real-world insights that surpass textbook knowledge.
In conclusion, the journey to achieving optimal weld quality is paved with informed decisions, attention to detail, and a relentless pursuit of excellence. By leveraging an expertise-rich approach—considering aspects of rod size, material compatibility, and equipment technology—one can consistently deliver welds that stand the test of time. Investing in this knowledge not only enhances craftsmanship but also solidifies one's reputation as a trusted authority in stainless steel welding.