Choosing the right electrode size is critical in achieving successful welding outcomes. Experienced welders understand that the electrode size directly impacts the bead shape, penetration, and overall strength of a weld. This article explores the nuances of electrode sizes for welding, drawing upon real-world experience and authoritative knowledge to provide valuable insights for professional welders and DIY enthusiasts alike.
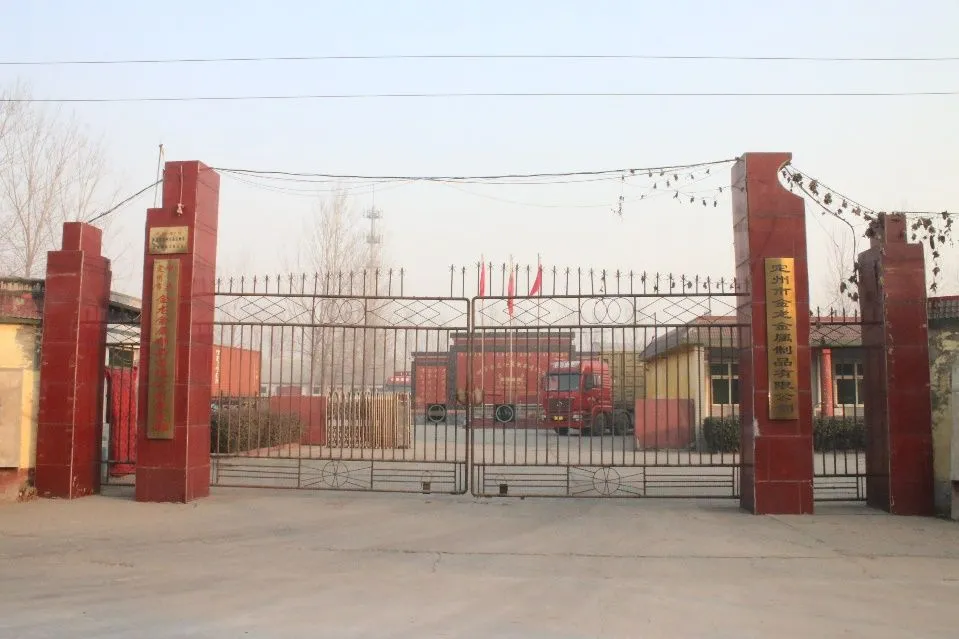
First, let's understand what electrodes are and their function in the welding process. Electrodes conduct the current necessary to perform the welding action, and they are consumed as the weld is created. The coating on the electrodes stabilizes the arc and protects the molten weld pool from atmospheric contamination. Electrode sizes vary to suit different materials, thicknesses, and types of welds.
When selecting an electrode size, the type of welding process you're engaging in is essential. Whether it’s Stick (SMAW), MIG, or TIG welding, each process has recommended electrode thicknesses for particular applications. Stick welding, for instance, utilizes electrodes ranging from 1/16 inch to 5/32 inch in diameter, depending on the task at hand. Heavier electrodes are typically employed in thicker materials needing deeper penetration.
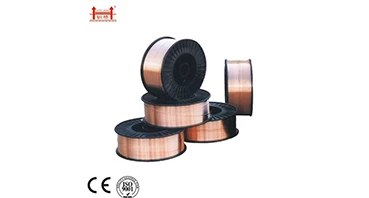
For Stick welding, the most common electrode sizes are 3/32 inch, 1/8 inch, and 5/32 inch. Experienced welders often suggest starting with a 3/32 inch electrode for practice on thinner materials due to its versatility and ease of control. For beginners looking to weld thicker materials, the 1/8 inch electrode is recommended. It provides a balance of deposition rate and control over the weld pool.
MIG welding utilizes consumable wire electrodes, with sizes generally ranging from 0.023 inch to 0.045 inch in diameter. The choice of wire size depends significantly on the thickness of the workpiece and the type of metal being welded. Thin metals like automotive body panels often require 0.023 inch wire, whereas structural steel work may necessitate 0.035 inch or larger. Proper wire size ensures effective heat control and minimizes the risk of burn-through or insufficient fusion.
In TIG welding, the electrodes are non-consumable and are usually made from tungsten. The diameter of tungsten electrodes ranges from 0.01 inch to 0.25 inch. Smaller electrodes are ideal for delicate tasks involving thin materials, such as aluminum or stainless steel, while larger electrodes are suitable for heavier tasks that require higher amperage and deeper penetration.
electrode sizes for welding
The thickness of the material being welded is another major factor in electrode selection. As a rule of thumb, the electrode should match the thickness of the metal being welded. For example, when welding a quarter-inch steel plate, a larger electrode, such as 5/32 inch in diameter, offers deep penetration and supports welding at higher amperages, thus providing stronger welds.
Temperature and welding position also influence electrode size choice. For overhead or vertical positions, smaller electrodes provide better control and reduce the risk of sagging or dropping molten material. In these positions, lower currents are often necessary, further supporting the use of smaller electrodes.
Experienced welders know the importance of trial and adjustment. Different welding machines can output varying current levels, even on the same setting, which necessitates testing electrode sizes under different machine settings to achieve optimal results. Documenting the settings and outcomes helps build a personal database that can act as a guide for future projects.
Lastly, always consult the manufacturer's guidelines for electrode use, as they make tailored recommendations for each specific electrode based on rigorous testing and validation protocols. Trusting these guidelines ensures consistency, quality, and safety in welding tasks.
By understanding and leveraging the dynamics of electrode sizes, welders can enhance their proficiency and produce stronger, more reliable welds across diverse projects. This knowledge stems from years of experience and is supported by technical expertise, ensuring welders meet the standards of authoritativeness and trustworthiness in their craft.