The commercial landscape is constantly evolving, and businesses frequently seek products that can offer solutions tailored to specific needs. The mention of 7018 vs 6010 likely brings to mind welding, a critical aspect in various industries such as construction, manufacturing, and repair. Understanding the differences between E7018 and E6010 welding rods not only enhances operational efficiency but also ensures safety and product quality.
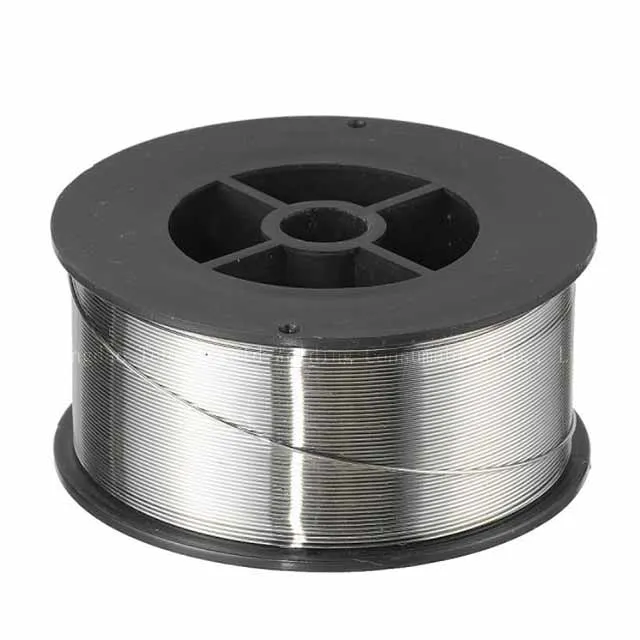
E7018 and E6010 rods are popularly utilized based on their unique properties and contributions to welding tasks. To make informed decisions in selecting between these, one must delve into their characteristics, applications, advantages, and potential limitations.
E7018 electrodes are low-hydrogen rods known for producing high-quality welds with excellent mechanical properties. These rods are renowned for their versatility and are often preferred for welding structural steel and mild steel applications. The low-hydrogen composition of E7018 minimizes the chances of weld cracking, ensuring durable joins. This makes them an authoritative choice especially in critical welding applications where strength and resilience are paramount.
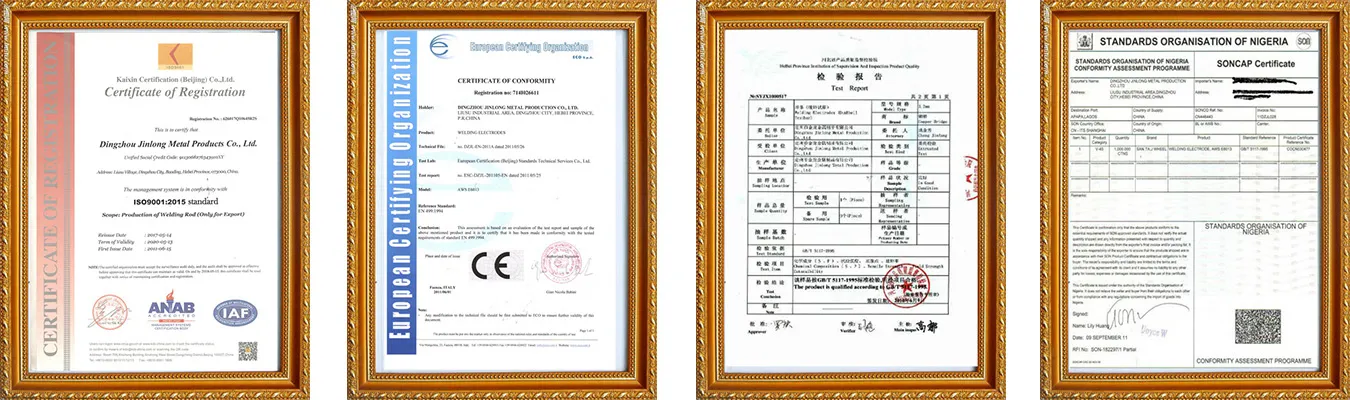
On the other hand, E6010 electrodes are characterized by their deep penetration capabilities and versatility in various positions. These rods excel in situations where pristine joints are required, especially in pipe welding and work involving out-of-position welds. Notably, E6010 rods produce a forceful arc and have the ability to weld through rust, oil, and paint, offering a level of trustworthiness in diverse working environments.
Differences between E7018 and E6010 also arise in terms of the techniques required for optimal usage. E7018 requires a cleaner surface and more controlled welding conditions to prevent porosity and other defects. The riddle lies in dry storage conditions to preserve their low-hydrogen properties. Conversely, E6010 rods can operate effectively even in less-than-ideal conditions due to their aggressive arc characteristics.
7018 vs 6010
The expertise required for each varies as well. E7018 welding calls for careful preparation and processes to ensure that joints are as intended. Experience in maintaining constant voltage to avoid defects like undercut or incomplete fusion is vital. In welding circles, proficiency in handling E7018 is often seen as a badge of expertise, given the technique sensitivity required.
E6010 welding demands a different form of skill, leaning more towards versatility and adaptability. Being able to control the arc and penetration in various positions is crucial. This rod is preferred among welders who require mobility and adaptability in their welding practice. The trust placed in E6010 is attributable to its performance under diverse conditions, making it indispensable for specific sectors like pipeline installation where pipe fit-up can significantly vary.
When deciding which rod to choose, the intended application is crucial. For shop welding and projects where stability and strength are of utmost importance, E7018 holds a higher authority. For fieldwork demanding flexibility and quick adaptation to changing conditions, E6010 is often the preferred choice.
In conclusion, both E7018 and E6010 rods come with their distinct merits and are designed to meet various welding requirements. Understanding the differences and drawing from authentic user experiences can elevate the outcome of welding projects. Choosing the right rod should be a decision informed by the specific conditions and demands of the task at hand. The choice between E7018 and E6010 is not a matter of one being superior, but rather which is more appropriate for the job at hand, ensuring safety, durability, and utmost quality.