In the realm of welding, the choice of welding rod can significantly impact the quality and durability of a project. Among the variety of options available, the 410 welding rod stands out as a specialized tool, particularly for projects involving hardenable martensitic stainless steel. This article delves into the characteristics and applications of the 410 welding rod, enveloping you in a profound understanding of its professional and authoritative standing in the welding industry.
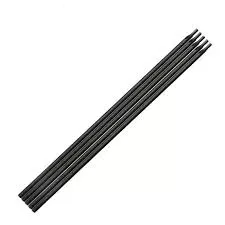
The 410 welding rod is specifically designed for welding AISI 410 stainless steel, a material recognized for its high strength, wear resistance, and corrosion resistance. These attributes make the welding rod an essential component in industries where the integrity and longevity of materials are pivotal. For instance, in sectors such as petrochemical, power generation, and aerospace, the 410 welding rod plays a crucial role in ensuring structural reliability and performance.
The welding rod contains approximately 12% chromium, which provides the necessary corrosion resistance required for many industrial applications. One of the unique features of the 410-grade welding rod is its ability to withstand heat treatments, thereby extending the versatility of projects it can be employed in. This characteristic makes the 410 welding rod particularly valuable in environments that subject materials to alternating cycles of high and low temperatures.
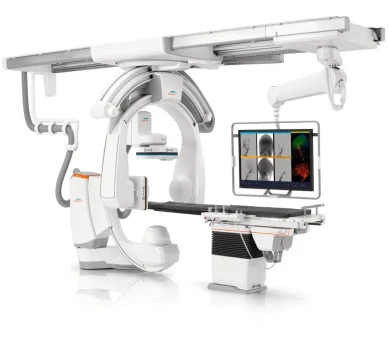
Experience builds trust, and in the realm of welding, experience translates into understanding the nuances of welding techniques. Using the 410 welding rod requires precision and specific preheating and post-heating treatments, making experienced welders invaluable when it comes to delivering a flawless finish. Preheating the materials before welding and a controlled cooling process after welding reduces the risks associated with stress corrosion cracking, ensuring the final weld retains its mechanical properties and resists wear.
410 welding rod
From a technical standpoint, the expertise involved in using the 410 welding rod cannot be overstated. It requires a deft hand and a meticulous approach to match the rod’s capabilities with the operational demands of a project. Welders must consider factors such as joint design, position of the weld, and environmental conditions, all of which influence the effectiveness of the 410 welding rod. Mastery in applying the correct techniques ensures the creation of robust welds that do not compromise the material integrity of the workpieces involved.
Authoritativeness in welding with the 410 rod also stems from the collective knowledge and research conducted over decades. Institutions and welding professionals continually expand the boundaries of knowledge around martensitic stainless steels and their applications, providing guidelines and standards for best practices. Adherence to these established practices is a testament to the authoritative nature of using 410 welding rods — a reflection of the continuous advancement in welding technology and its application to industrial challenges.
Finally, trustworthiness, a cardinal attribute, extends beyond the product itself to encompass the manufacturers and distributors of the 410 welding rods. Reliable manufacturers adhere to stringent quality controls, ensuring each rod produced meets the highest benchmarks of performance and safety. This reliability is vital in earning the trust of professionals who rely on these welding rods for critical applications across various industries.
In summary, the 410 welding rod embodies not only the sheer technical prowess required for its effective use but also an amalgamation of experience, expert knowledge, authority, and trust within the welding community. Its specialized properties make it indispensable in applications that demand longevity, strength, and resistance to corrosive elements, thereby underscoring its essential role in modern-day metallurgy and welding practices. As advancements continue in the field, the 410 welding rod remains a steadfast component, its legacy built upon decades of application and refinement in welding technologies.