When it comes to welding, the choice of the right electrode is critical to achieving superior results. The 3 4 7018 welding rod is a staple in the welding industry for many reasons, and understanding its applications, benefits, and specifications can significantly enhance your projects. This article aims to provide a comprehensive look into the 3 4 7018 welding rod, focusing on its practical applications and why it is a preferred choice among professionals.
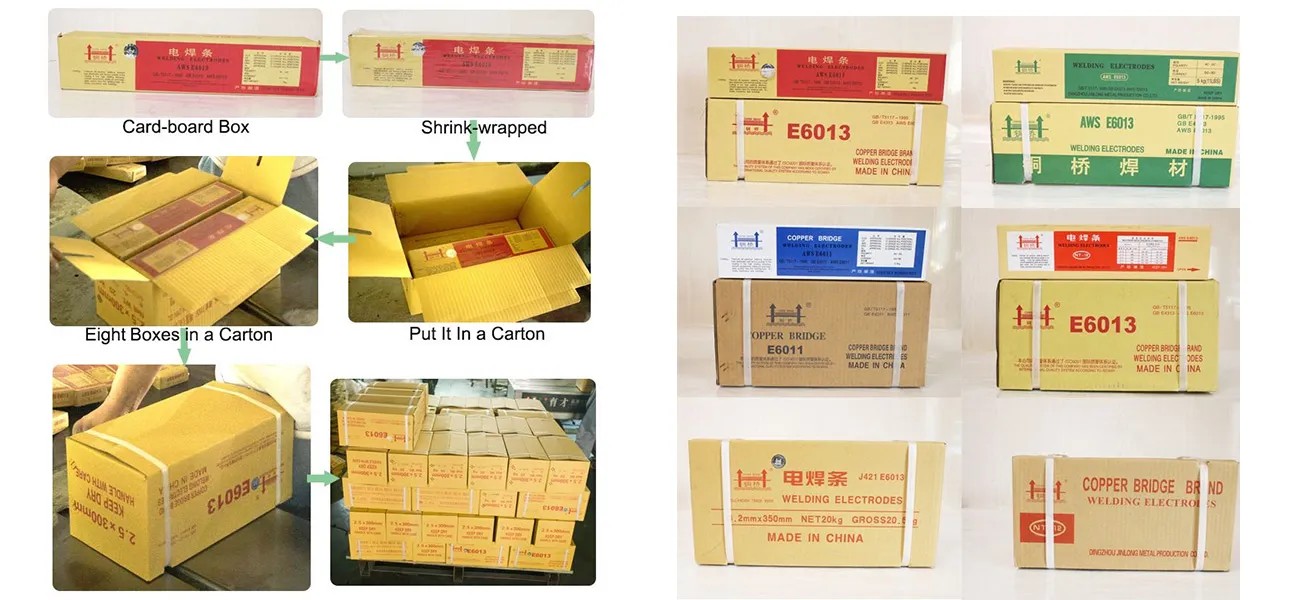
The 7018 welding rod is renowned for its low-hydrogen content, which reduces the risk of cracking in the weld area. This characteristic is particularly important in environments where structural integrity is paramount. The 3 4 specification indicates the rod's diameter, which is ideal for medium to large-scale projects. Its thickness allows for the creation of strong welds while accommodating the depth needed for substantial pieces of metal.
Professionals in the field appreciate the 7018 rod for its adaptability across various steel grades, including low, medium, and high carbon steels. Its performance is also notable when working with structures exposed to dynamic loading conditions. Bridges, skyscrapers, and pipelines are some structures that benefit significantly from the robust welds formed by 3 4 7018 rods.
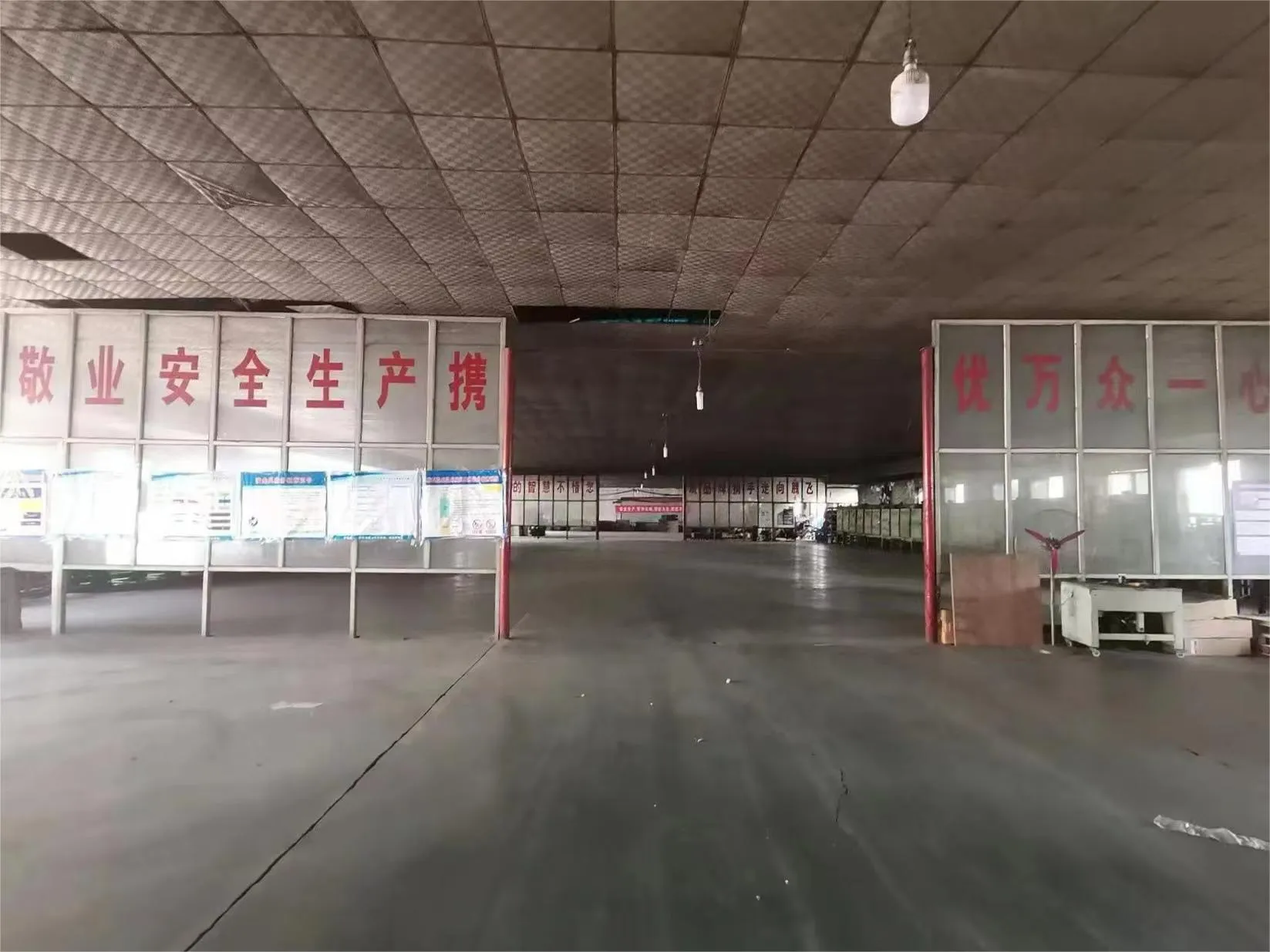
Another key advantage of the 3 4 7018 rod is its operational efficiency. It works well with both AC and DC currents, providing flexibility in different welding environments and for welders with varying skill levels. Its user-friendly nature means that even those newer to welding can achieve professional results. The arc produced is stable and smooth, minimizing spatter and allowing for a cleaner welding environment. Additionally, the slag is easy to remove, which saves valuable time during the clean-up phase.
In terms of expertise, welders must be aware that the 7018 rod requires proper storage to maintain its low-hydrogen properties. Exposure to moisture can lead to hydrogen embrittlement, compromising the strength of the weld. Therefore, maintaining these rods in a warm, dry environment—preferably in a rod oven—is crucial for preserving their integrity.
3 4 7018 welding rod
From an authoritative perspective, the American Welding Society (AWS) endorses the use of 7018 rods in critical applications.
Their standards are widely regarded as benchmarks for welding practices. Following these guidelines ensures that the welds not only meet industry expectations but also exceed them in terms of durability and safety.
Regarding trustworthiness, the 3 4 7018 welding rod has consistently demonstrated its reliability in various industrial applications. Companies repeatedly turn to this electrode to meet the demands of rigorous structural projects, attesting to its trusted status in the field.
In difficult welding conditions, knowing you have a dependable welding rod can make all the difference. The 3 4 7018 is dependable, offering excellent penetration, strong bonds, and versatility that few other electrodes can match.
In conclusion, the 3 4 7018 welding rod is a product defined by its high performance, reliability, and adaptability, making it indispensable to the skilled welder. Whether embarking on a complex commercial construction project or simply looking for dependable performance, this welding rod stands out as a top choice. Understanding and leveraging the strengths of the 3 4 7018 can lead to significant improvements in weld quality, ultimately fueling success in all your welding endeavors.