Welding is an essential process across various industries, requiring precision, skill, and the right materials to ensure strong, durable joints.
A key component in arc welding is the electrode, and among the most widely used is the E7018 electrode. Its popularity stems from its versatile nature and reliability in producing high-quality welds. Understanding the specifications and applications of the E7018 electrode is crucial for welders looking to achieve optimal results in their projects.
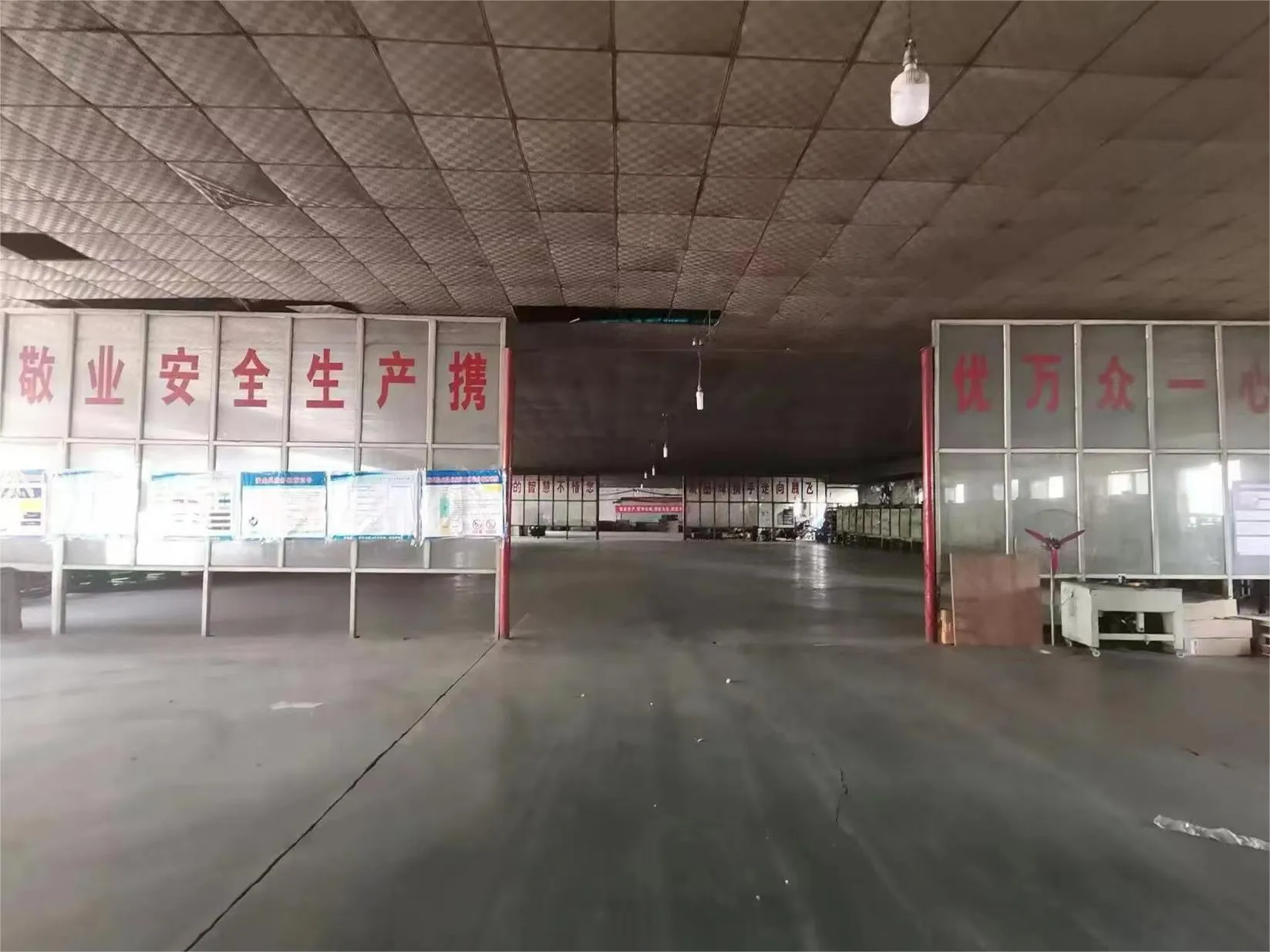
The E7018 electrode is a low-hydrogen, iron powder type filler metal, which provides welds with exceptional mechanical properties. To break down its identification the 'E' signifies that it is an electrode, '70' indicates a tensile strength of 70,000 psi, the '1' denotes its position usability which is all positions, and the '8' points to the coating type and current compatibility. These aspects make it an ideal choice for welding carbon and low-alloy steels.
A notable advantage of the E7018 electrode is its low-hydrogen content. Reducing hydrogen levels is vital as it minimizes the risk of hydrogen-induced cracking, which can be detrimental to the integrity of the weld. For this reason, E7018 electrodes must be stored in a dry environment and sometimes preheated before use to maintain their low-hydrogen properties. This meticulous handling ensures the electrode performs optimally, leading to less porosity and better fusion with the base metal.
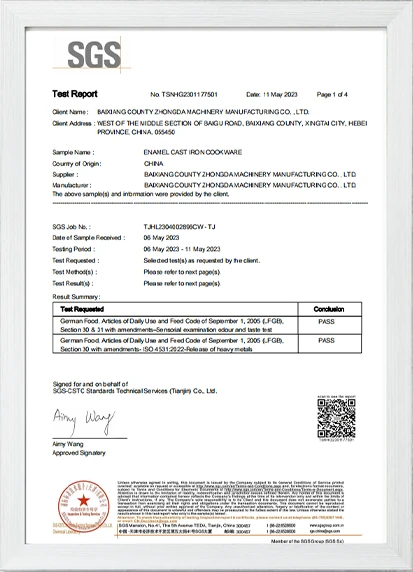
In terms of application, the E7018 is celebrated for its adaptability. It can be employed in structural welding, such as in the construction of buildings, bridges, and ships. Moreover, it is suitable for joining thick metal sections due to its high deposition rate and ability to produce a smooth, strong weld bead. This is particularly beneficial in projects where the reliability of the weld is non-negotiable. Users often find its smooth arc and easy-to-remove slag contribute to a cleaner job and save time in post-welding cleanup.
The E7018 electrode is not only about technical specifications but also about better workplace safety and environment. Because of its efficient and less fume-producing nature compared to other electrodes, welders can work under safer and cleaner conditions. This aspect aligns with modern industry standards that increasingly prioritize environmental sustainability and occupational health.
welding electrode e7018 specification
From a technical expertise perspective, mastering the use of E7018 electrodes involves understanding its behavior under various current settings. It operates best under DC+ (direct current, electrode positive) but can also be used with AC, providing welders with flexibility depending on the equipment available. Adjusting the welding parameters, such as amperage, based on the thickness of the workpiece and electrode diameter, is crucial for achieving the desired penetration and fusion.
Despite its broad applicability, it's imperative that welders conduct preliminary tests and practice to refine their technique with E7018 rods, particularly when transitioning from other electrode types. This ensures consistent adherence to project specifications and the production of structurally sound welds.
Given the E7018 electrode's robustness and versatility, its reputation as a reliable option in the welding industry is well-deserved. However, like all tools, its true potential is unlocked through knowledge and expertise. Welders armed with an understanding of this electrode’s specifications and handling can confidently tackle projects with the assurance of quality workmanship. Industries and workshops relying on the E7018 can achieve not just structural integrity, but also economical and timely project completion with reduced rework.
In summary, the E7018 welding electrode is a testament to the advances in metallurgical technology, suitable for a wide range of applications while ensuring high-quality, durable welds. By integrating this electrode into regular practice and understanding its specific requirements, welders and industry professionals can elevate the standard of their work, sustaining the ever-evolving demands for stronger, safer, and more reliable welded structures.