When delving into the world of welding, one might encounter the 6013 welding rod, a pivotal tool revered by both novices and seasoned professionals. Known for its versatility and effectiveness, the 6013 electrode holds a special place in the industrial sector. This article will explore the specific uses, benefits, and best practices associated with the 6013 welding rod, underscoring its importance in various applications.
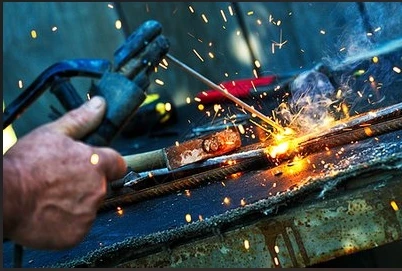
Widely celebrated for its usability in multiple welding positions, the 6013 welding rod is often the go-to choice for projects requiring shallow penetration. This characteristic makes it ideal for welding thin materials, such as sheet metal, without risking the burning through of materials. Used extensively in the fabrication of automobiles, home appliances, and other light-to-medium gauge steel projects, the 6013's mild penetration allows welders to work with finesse and precision.
The ease of use associated with the 6013 electrode is one of its most appealing attributes. Featuring a rutile-based coating, this welding rod produces a smooth arc and is forgiving to mistakes, making it a prime candidate for beginners learning to control their welding technique. The coating also contributes to an easily manageable slag, which is simple to clean, resulting in aesthetically pleasing welds. For professional welders, this feature ensures efficiency and time savings, as less time is spent on cleaning post-weld.
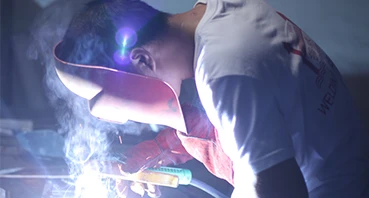
Performance is another aspect where the 6013 excels. Known for producing stable arcs, the rod allows for a smooth transition between beads, reducing spatter and creating uniform depositions. This stability is crucial in projects where the appearance and structural integrity of the welds are paramount, such as in the manufacturing of consumer products that demand both durability and aesthetic appeal.
Reliability and trustworthiness are further underscored by the 6013 welding rod's adaptability to various electrical outputs. Standing as a true testament to versatility, the 6013 functions seamlessly with both AC and DC welders, hence offering flexibility for different working environments. This versatility makes it a preferred choice in fieldwork where conditions and equipment can be unpredictable.
what is a 6013 welding rod used for
Safety and storage are often overlooked but critical components of working with welding rods. It's essential to store the 6013 rods in a dry environment to prevent the coating from absorbing moisture, which could adversely affect performance. Following manufacturer guidelines for storage and usage ensures the rods remain effective and reliable.
Harnessing the full potential of the 6013 welding rod requires understanding subtle nuances. Professionals often emphasize controlling speed and technique to maximize the quality of welds. Slower travel speed allows the rod to properly penetrate the material, while excessive speed can lead to defects like porosity or insufficient fusion.
Seasoned welders also suggest experimenting with different amperages to fine-tune the arc characteristics. While typical amperage settings range from 60 to 120 amps, contingent on material thickness, testing within this range helps achieve optimal performance tailored to project requirements.
In summary, the 6013 welding rod stands as a versatile, reliable choice for various welding applications. Its ease of use and adaptability to different settings make it an ideal tool for both novices and seasoned professionals. Leveraging the full potential of this electrode calls for a mindful approach to maintenance, technique, and safety, reinforcing its reputation as an essential element in the welding landscape.