For professionals in the welding industry, the choice of electrodes is crucial, particularly when it comes to welding stainless steel. When selecting arc welding electrodes specifically designed for stainless steel, understanding the composition, functionality, and application scenarios is essential.
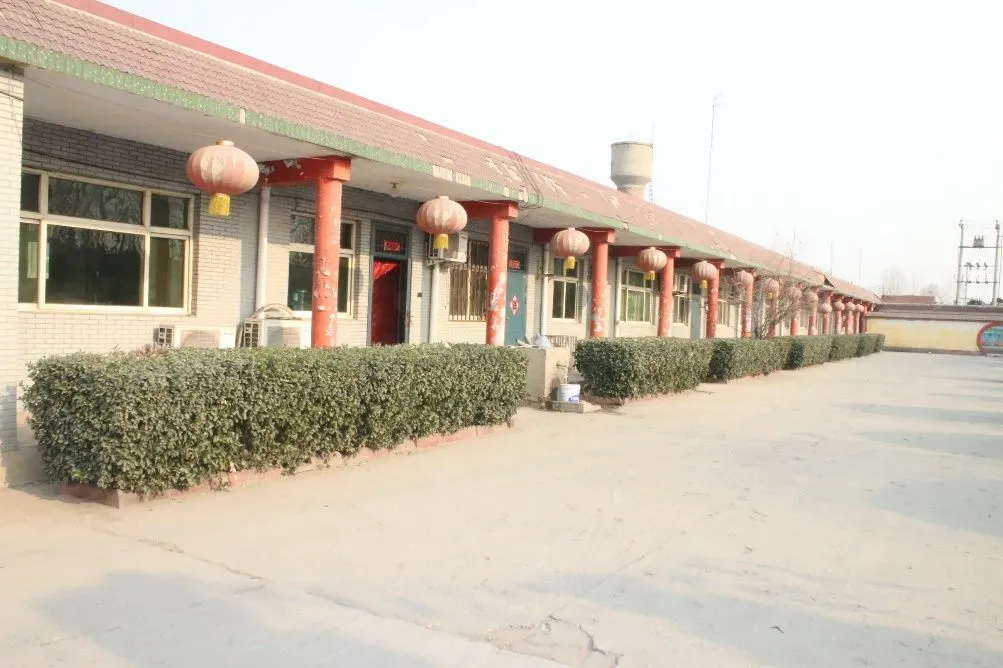
Arc welding is among the most efficient methods for joining metal. However, stainless steel, with its unique properties, demands specialized electrodes to ensure optimal results and longevity of the weld. The right electrodes not only enhance performance but also guarantee the weld's integrity under stress and over time.
Stainless steel is prized for its corrosion resistance, aesthetic appeal, and mechanical toughness. However, its thermal conductivity and expansion rates create challenges during welding. Selecting a suitable electrode helps mitigate these challenges. With over two decades of experience, I’ve seen how pivotal electrode choice can be in defining the success of a welding project.
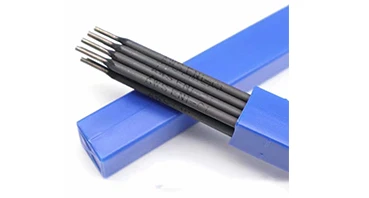
The primary factor in choosing electrodes for stainless steel is their composition. The electrode should match the base metal type to ensure similar corrosion resistance and mechanical properties. For example, austenitic stainless steels, the most common stainless steel group, often require electrodes with a similar or ideally matched chromium-nickel composition. An ER308L electrode, popular for general-purpose applications, meets such needs effectively, minimizing the potential for carbide precipitation and intergranular corrosion due to its low carbon content.
Equally important is the electrode's coating type. The coating influences arc stability, slag removal, and penetration depth—key components in developing a robust weld. Most stainless steel electrodes use basic coatings, which are known for their clean welds and stronger resistance to cracking, making them ideal for critical and high-pressure weld applications.
Versatility and suitability of electrodes are determined only partially through composition and coatings. The welding positions they support are also crucial. An electrode supporting all-position welding can save time and resources in complex assembly scenarios. Experienced welders value this versatility when dealing with intricate joint configurations where positional adjustments are frequent.
arc welding electrodes for stainless steel
Further exploration into stainless steel arc welding electrodes also probes the reliability and trustworthiness of the manufacturer's claims. With counterfeiting and subpar electrodes circulating in the market, relying on established and credible manufacturers ensures electrode quality and compatibility. Brands with ISO certification or rigorous testing procedures offer increased reliability to seasoned professionals demanding the best results.
Professionals also factor in the electrode's storage life and conditions. Stainless steel electrodes can absorb moisture quickly, compromising their effectiveness. Proper storage—ideally in a climate-controlled environment—is recommended to prevent water absorption that can lead to hydrogen-induced issues during welding.
Personal experience has demonstrated that integrating testing welds during project preparation minimizes potential issues. It not only verifies the electrode’s performance on a small scale but also allows for adjustments in technique or electrode selection. This testing ensures reduced downtime and heightened efficiency once the actual project commences.
Moreover, environmental considerations have grown in importance as industries strive for sustainability. Some manufacturers are moving towards eco-friendly production processes that reduce their carbon footprint. Welding professionals dedicated to integrating sustainable practices can opt for electrodes from these environmentally-conscious brands, further bolstering the eco-friendliness of stainless steel installations.
In conclusion, selecting appropriate arc welding electrodes for stainless steel is as much about technical know-how as it is about aligning with reputable manufacturers and mindful practices. The right electrodes not only align with the specific stainless steel grade but are also suited to the environment and welding techniques necessary for each project. With meticulous selection informed by personal expertise and enduring manufacturer credibility, welders ensure that their projects are both professionally sound and sustainable.