Selecting the right welding rod is crucial for achieving high-quality welds, especially for tasks requiring precision and reliability. The 7014 welding rod, particularly the 3/32 size, is a versatile choice for many welders—both hobbyists and professionals alike. Renowned for its strength and ease of use, this rod is a staple in many workshops. Understanding its specifications, applications, and best practices for use can enhance your welding projects significantly.
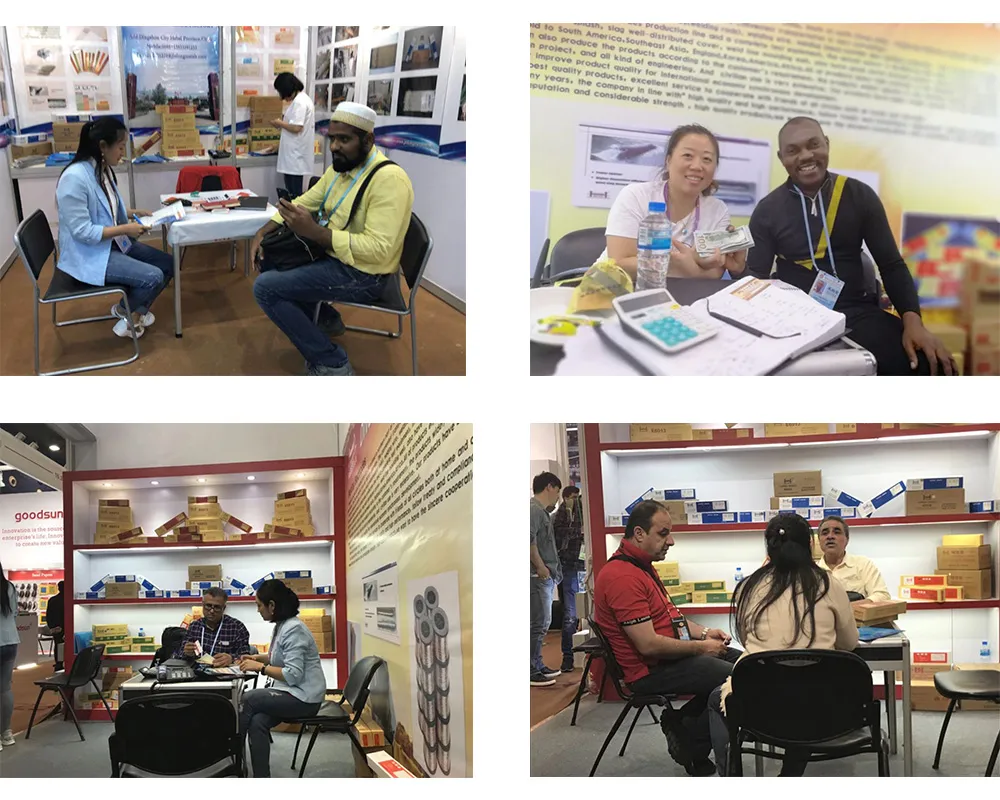
Crafted with a coating of iron powder and titania, the 7014 welding rod operates on both AC and DC currents, making it adaptable across various power supplies. This feature alone marks it as a versatile tool for a wide array of welding tasks, ranging from small household repairs to more demanding industrial applications. It is crucial to understand, however, that the amperage setting is integral to optimizing its performance—specifically within the 3/32 size, which typically requires a range of 70 to 100 amps. The accurate current setting ensures strong bond formation without the common pitfalls of spatter and burn-through.
When working with the 7014 rod, the welder can appreciate its smooth arc, making it suitable for welding in different positions, including flat, horizontal, vertical, and overhead. This rod's thick coating creates a protective slag layer, which not only shields the molten weld pool from contamination but also contributes to the rod's excellent deposition rate. The result is clean welds with minimal cleaning required, ideal for users who need both speed and efficiency.
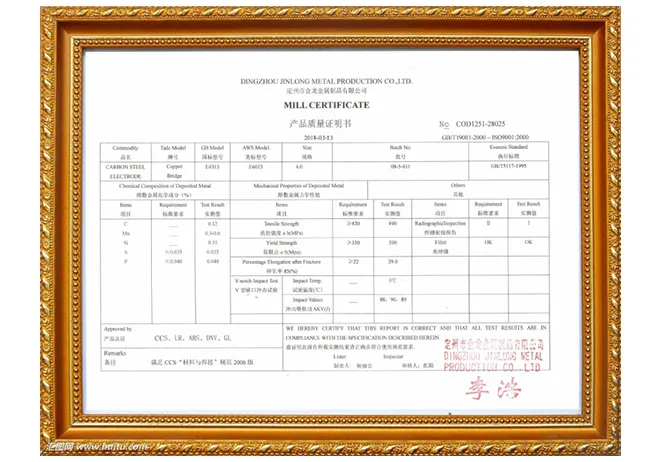
The industry values the 7014 welding rod for its tensile strength, recorded at approximately 70,000 psi. Such strength is an assurance for the integrity of the welded joint, which is essential in applications where safety is paramount. For projects involving mild steel, the 7014 rod offers a reliable solution, providing strong, ductile joints that withstand regular stress and strains commonly encountered in structural components.
7014 welding rod 3 32 amps
When considering the fabrication of projects such as agricultural equipment, steel structures, or general loading frameworks, the predictability of the 7014 rod's performance adds to its appeal. Furthermore, its user-friendly nature extends to beginners who are building their skills. The rod's melting characteristics reduce the likelihood of excessive weld buildup, which is often a challenge for learners.
Safety, of course, remains paramount when operating any welding equipment. While using the 7014 rod, ensure that you adhere to best safety practices such as wearing appropriate personal protective equipment (PPE), including welding helmets, gloves, and aprons. Protecting oneself from electromagnetic fields and maintaining an adequately ventilated workspace are principles that go hand-in-hand with achieving excellent welding results.
Apart from safety measures, ensuring the welding machine is calibrated correctly for the specific rod size and desired outcome cannot be overstressed. Taking the time to practice on scrap material aids in fine-tuning the settings, ensuring both the arc stability and bead appearance meet expected standards.
The 7014 welding rod, with its high usability, mechanical properties, and ease of handling, remains a reliable tool in any welder's inventory. For those new to the craft as well as seasoned professionals looking for consistency, its benefits are evident. Commitment to regular practice and a deep understanding of each unique piece of material being worked on will unlock the full potential of this welding rod, creating strong, durable connections ready to meet today’s diverse welding challenges. With the right technique and conditions, the 7014 rod represents not just a choice of tool, but a pathway to excellence in welding craftsmanship.