When it comes to welding, the choice of the right welding rod can make or break the strength and durability of your welds. For professionals and hobbyists alike, understanding the difference between various types of welding rods is crucial. One of the debates that often arises is the choice between the 3/32 inch and 1/8 inch welding rods. Each has its specific uses and advantages, and selecting the appropriate one can significantly impact your project's outcome.
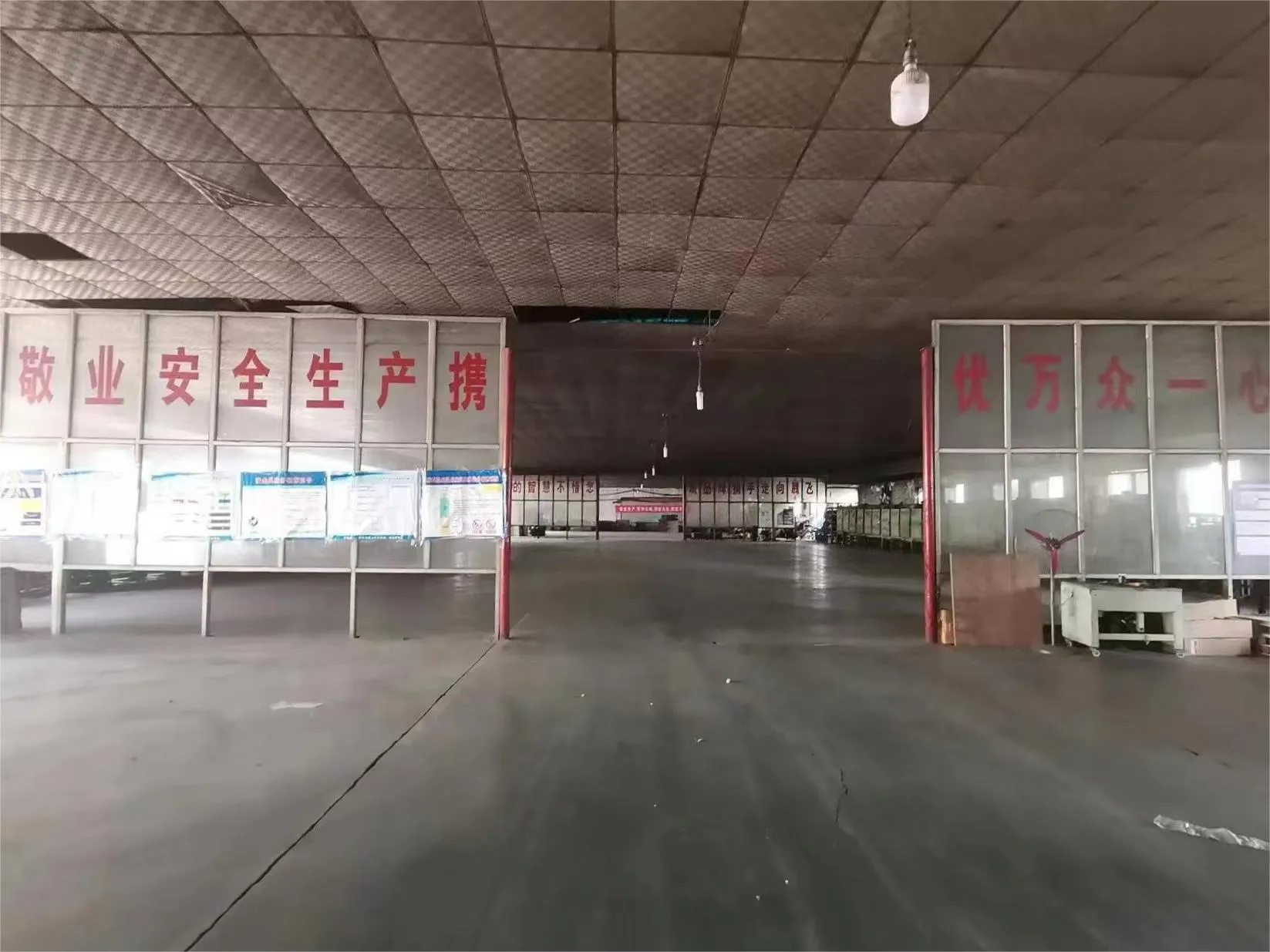
The 3/32 vs 1/8 welding rod discussion starts with understanding the basic composition and use cases for each. The size of the welding rod, indicated in inches, refers to its diameter, with the 3/32 inch rod measuring approximately 2.
4mm and the 1/8 inch measuring roughly 3.2mm. This might seem like a minor difference, but in welding, precision is key.
Let's delve into the unique characteristics and best practices for using each rod size.
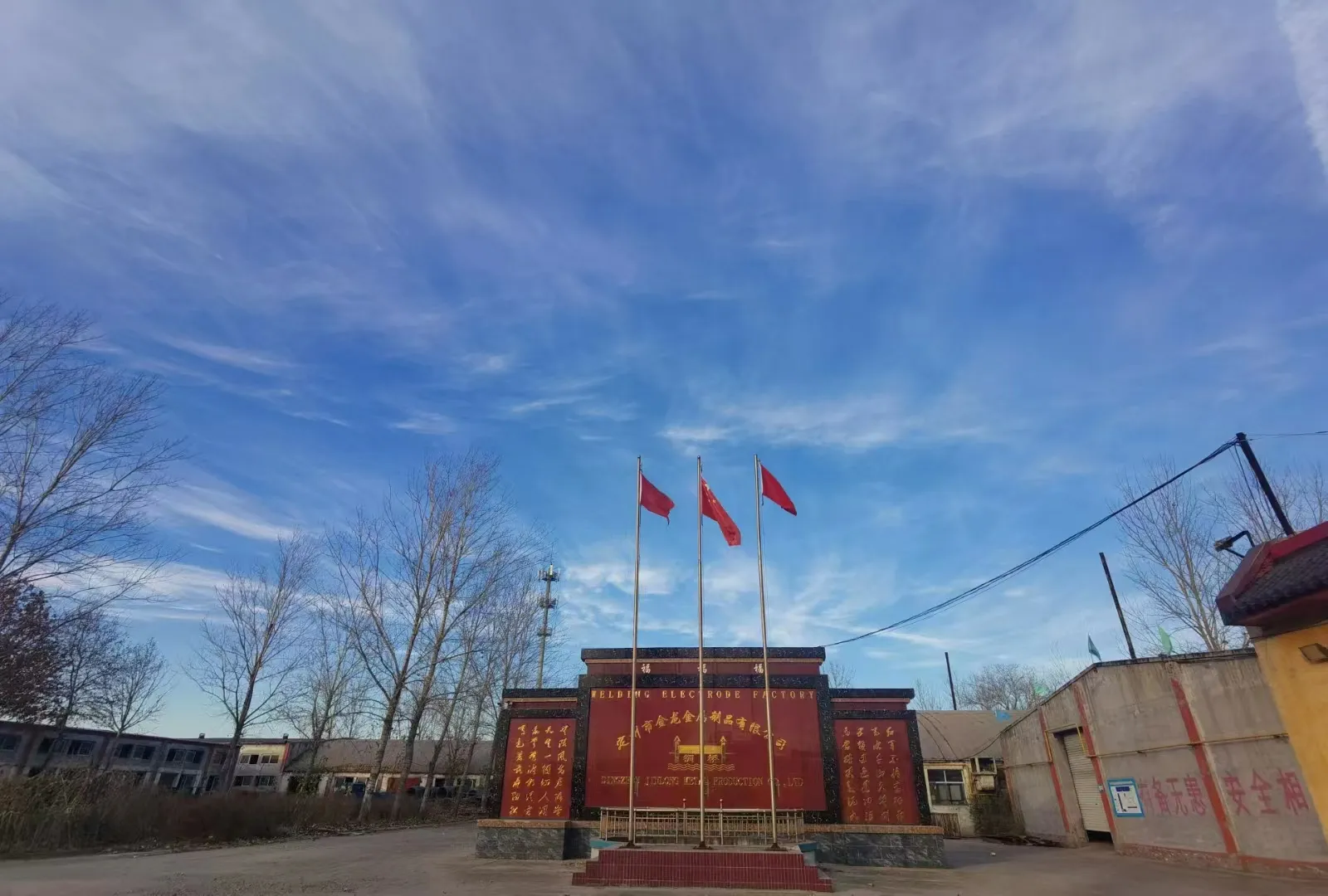
3/32 Inch Welding Rod Precision and Versatility
The 3/32 inch welding rod is favored for its precision and control, making it ideal for projects where finesse is more important than brute strength. It's frequently used for welding thin metals due to its smaller size, which requires less heat and provides better control. This makes it an excellent choice for intricate welds where attention to detail is paramount.
Typically, this rod is the go-to choice for applications in automotive repair, where thin gauge metals are prevalent. Home hobbyists also find the 3/32 inch rod advantageous due to its ease of use with a standard AC/DC welder, offering them the flexibility to work on a variety of DIY projects without needing high-end equipment.
One real-world example of its application could be in the repair of a car's exhaust system, where the thin walls of the exhaust pipes demand a rod that can create a smooth, clean weld without compromising the material integrity.
1/8 Inch Welding Rod Strength and Durability
On the other side, the 1/8 inch welding rod is synonymous with power and is the preferred choice when working with thicker materials. This rod’s larger diameter means it can handle more current, which in turn allows for deeper penetration and stronger welds. Consequently, it's widely used in structural projects, heavy machinery repair, and construction where the strength of the weld is of utmost importance.
3 32 vs 1 8 welding rod
Professionals in the field often rely on these rods when constructing steel buildings or repairing large farm equipment. For instance, if you're tasked with welding a large metal beam, the 1/8 inch rod is the perfect choice due to its superior ability to fuse thick metals securely.
Additionally, the 1/8 inch rod's robust performance is not limited to heavy-duty applications; it also excels in creating large, long welds efficiently, enhancing productivity in commercial settings.
Expert Insight into Welding Rod Selection
Industry experts assert that choosing between the 3/32 inch and 1/8 inch rods should boil down to the material thickness and the nature of the job at hand. However, mastering the use of both allows a welder to tackle a broader scope of projects with confidence and ease.
In a laboratory test setting, experiments consistently show that using the wrong rod size for a task can lead to suboptimal weld strength, increased porosity, and unsatisfactory finishes, emphasizing the importance of educated rod selection.
The Authority of Trustworthiness in Welding Practices
Lean into trusted resources and standards set by authoritative bodies like the American Welding Society (AWS) for guidelines on best practices and welding rod specifications. Their research and published guides can serve as a benchmark for selecting the optimal rod for various projects, ensuring both safety and quality.
In Conclusion
The ongoing use and selection of either the 3/32 inch or 1/8 inch welding rod substantially impact the efficiency and outcome of welding projects. Each type brings its unique set of strengths that cater to specific project requirements, aligning with industry standards for quality and durability. Understanding the fundamental distinctions and applications of these welding rods will elevate your welding proficiency and project success.