Welding is an intricate craft that involves a variety of techniques and materials, each tailored to specific requirements and outcomes.
Central to this process are welding rods, which are essential consumables used to join metal pieces. Understanding the different types of welding rods and their applications enhances both the quality of work and the safety of the welder.
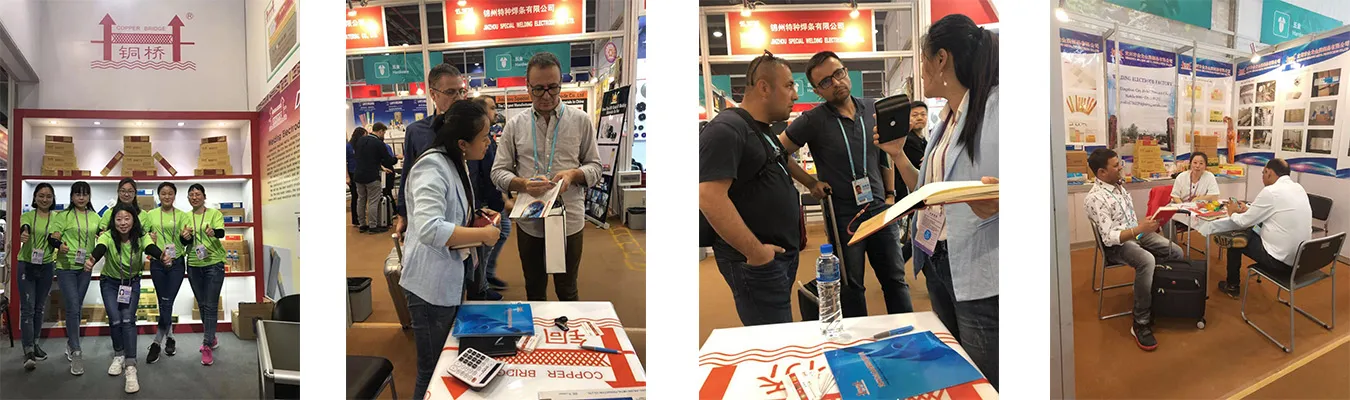
E6010 welding rods are commonly used for general-purpose welding, often in applications that require deep penetration such as pipe welding and structural applications. This type of rod is favored for its ability to weld in all positions and its robustness against rust, oil, and dirt, making it an excellent choice for fieldwork and projects requiring irregular or unclean surfaces.
Another versatile option is the E6011 welding rod, which shares similarities with E6010 in terms of its penetration capabilities and usability in various positions. However, E6011 rods differ in that they can be used with AC (alternating current), in addition to DC (direct current), providing more flexibility depending on the power source available. This feature makes the E6011 a go-to rod for household repairs and thin material welding.
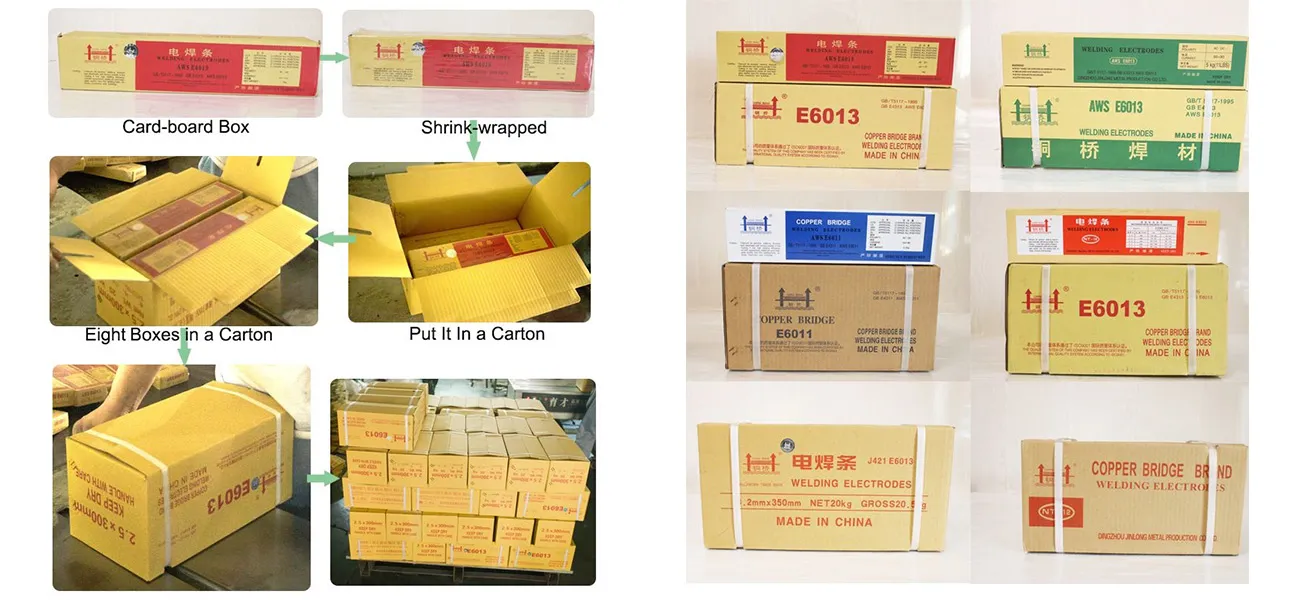
For projects demanding a smoother finish, E7018 welding rods are often the rod of choice. These rods provide a strong weld with less spatter, making them ideal for thick metal joins in applications like bridge construction and heavy-duty manufacturing. The low hydrogen content in E7018 rods minimizes the risk of cracking, ensuring durable welds that meet professional standards.
A more specialized rod, the E7024, is typically employed for welding in flat and horizontal positions. Known for its fast deposition rate, this rod is useful when efficiency is a key concern in production settings where long, continuous welds are required. Its high iron powder content ensures that thick and strong welds are created, suitable for heavy machinery and large-scale structural components.
types of welding rods and uses pdf
While selecting the appropriate welding rod, it is crucial to consider the material being welded. For example, stainless steel projects might require specialized stainless-steel rods, such as the 308L or 309L, which provide excellent corrosion resistance and are used primarily in food and chemical industry applications.
Equally important is understanding the environment in which welding takes place. Certain rods like E7018 need to be stored at specific temperatures in rod ovens to maintain their low hydrogen properties, ensuring optimal performance and reducing the risk of faulty welds.
Safety is paramount in welding. Each type of rod has different fume characteristics, and welders must use the correct protective equipment to prevent inhalation of harmful substances. Proper ventilation and personal protective gear, such as masks and gloves, are essential to ensure a safe working environment.
Mastering the diverse world of welding rods not only enhances a welder's skill set but also significantly impacts the quality and durability of projects. By comprehensively understanding each rod's unique characteristics and recommended uses, welders can execute their work with increased precision and reliability, meeting the high industry standards required in today's competitive markets.