Stainless steel welding rods are indispensable tools in any professional welder's arsenal, providing the versatility and strength needed to tackle diverse projects. Among various types, each offers unique properties catered to specific applications, ensuring optimal performance and durability. Understanding the intricacies of these welding rods requires expertise, as each type is designed to meet precise demands and conditions.
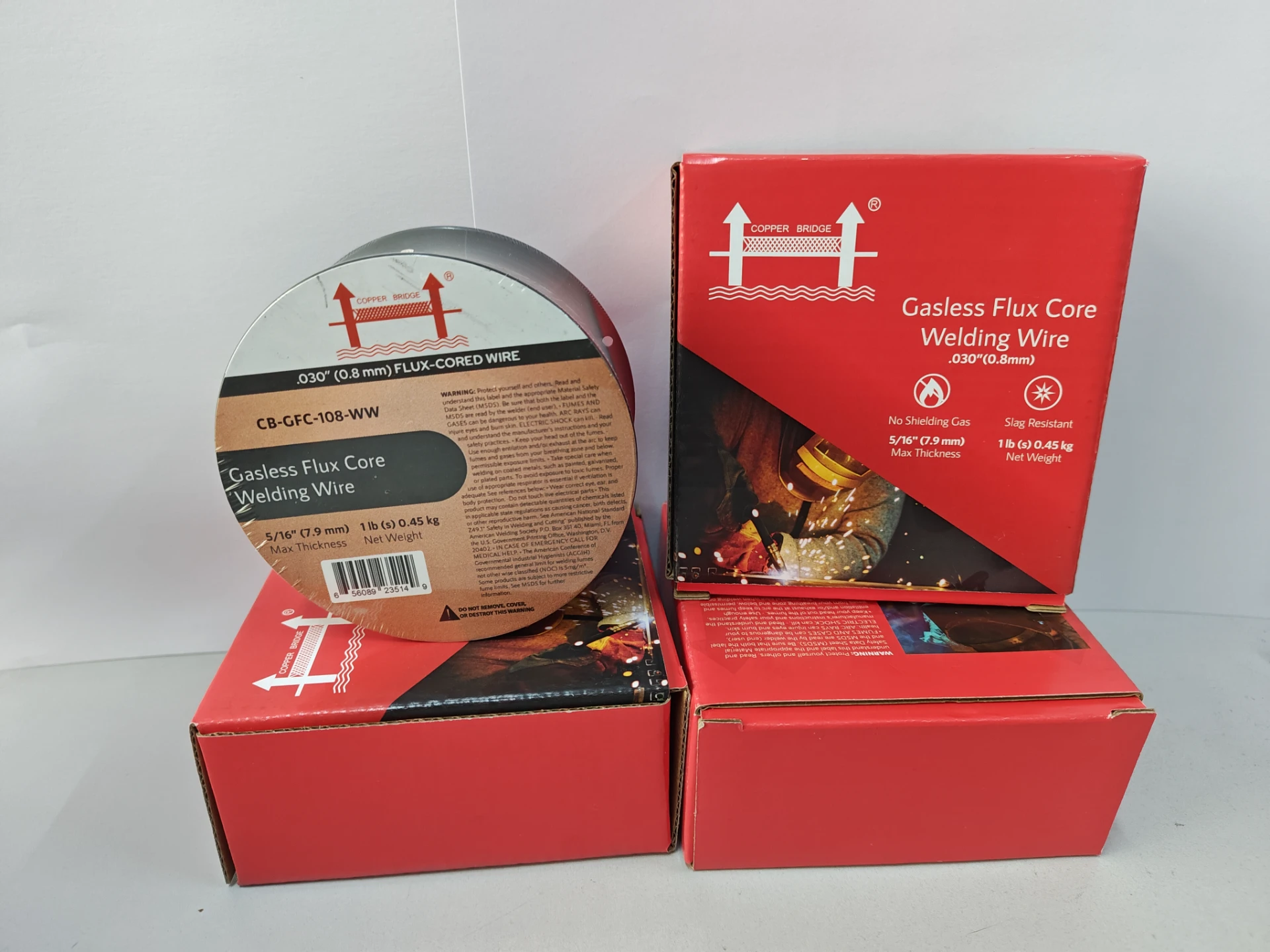
The 308L stainless welding rod is renowned for its outstanding ability to weld stainless steel grades 304 and 304L. Its low carbon content minimizes carbide precipitation, reducing the risk of intergranular corrosion, which is crucial for applications involving food processing equipment and pharmaceutical machinery. Its versatility and strength make it the go-to choice for industries seeking reliable, clean, and aesthetically pleasing welds.
Meanwhile, the 309L rod serves a unique purpose, primarily used for joining stainless steel to mild or low alloy steel. Its duplex stainless steel properties make it ideal for applications that require superior strength and corrosion resistance, such as in power plants and chemical factories. The extra chromium and nickel in the 309L rod not only fortify the bond between dissimilar metals but also increase the durability of the welds under high thermal stress.
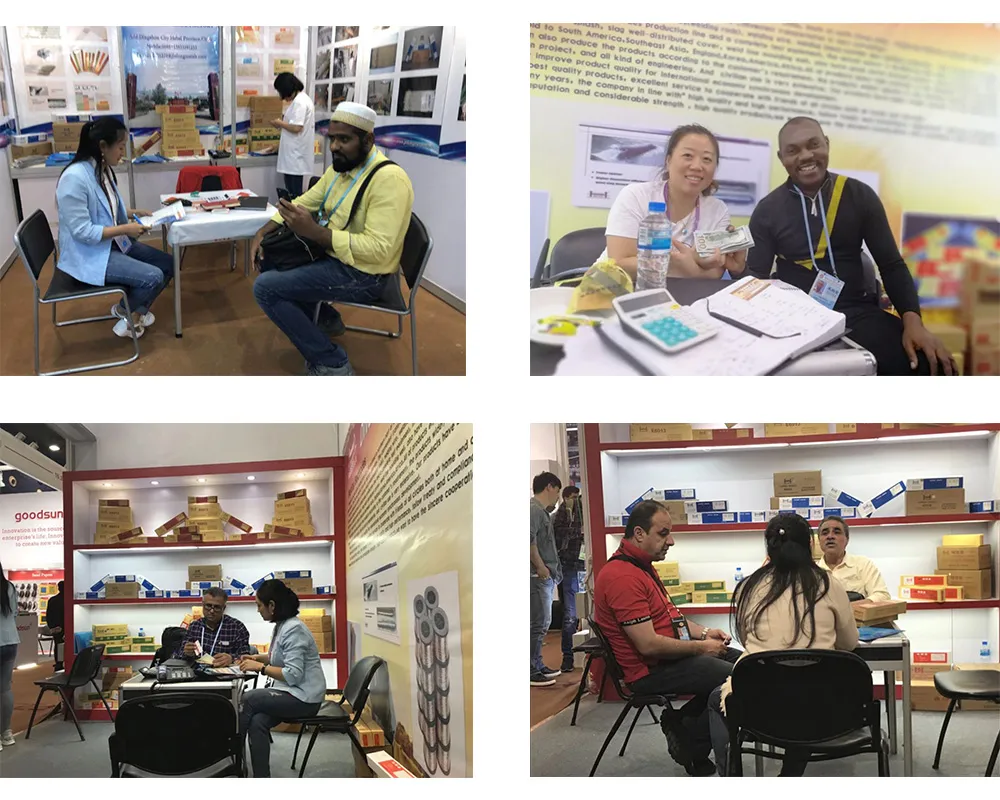
For applications needing high resistance to heat scaling and oxidation, the 310 stainless welding rod is unmatched. It excels in high-temperature environments, capable of withstanding harsh conditions in furnace and heat exchanger components. This rod's composition ensures weld integrity and longevity even at temperatures reaching 1200°C, demonstrating unmatched reliability in intense industrial applications.
Introducing the 316L stainless steel welding rod, a product revered for its exceptional molybdenum content that enhances corrosion resistance, especially against chlorides and other industrial solvents. This property makes it particularly valuable in marine environments or chemical processing plants, where resistance to salt and acidic materials is crucial. Welders rely on the 316L rod to achieve robust and corrosion-proof joints, ensuring the safety and functionality of structures in harsh conditions.
stainless welding rod types
The 347 stainless welding rod stands out for its addition of niobium, which stabilizes the weld against intergranular corrosion. This feature is vital in applications involving high temperatures and prolonged exposure, such as in aerospace and petrochemical industries. The presence of niobium helps in maintaining structural integrity, thereby extending the lifespan of components exposed to cyclic temperatures.
Each type of welding rod is engineered to meet specific challenges, ensuring precision and efficiency in every project. Factors like the alloy composition, tensile strength, and thermal expansion characteristics play critical roles in selecting the appropriate rod for a task. For professionals, understanding these nuances is crucial, as the wrong choice can lead to structural weak points, compromising safety and performance.
Building trust and credibility in welding necessitates not just the selection of the correct rod, but also adherence to strict quality standards and consistent training. As industry standards evolve, staying informed on new technologies and methodologies is vital. Leaders in the welding industry prioritize continuous learning and adapt to innovations to maintain their expertise and authoritativeness.
The trustworthiness of a welding product lies in its certification and compliance with international standards, which instill confidence in both manufacturers and consumers. Products tested rigorously under diverse conditions are deemed reliable, equipping professionals with the assurance of excellence in every weld.
Thus, the exploration of stainless welding rod types reveals a landscape where precision, expertise, and innovation converge, driving growth and efficiency across industries. Welder proficiency, combined with high-quality products, ensures that structures remain safe, durable, and reliable, earning trust and validation in the complex world of modern manufacturing.