Navigating the complex world of stainless welding rod selection is a critical skill for anyone engaged in the metalworking industry. This process demands a nuanced understanding of various welding rod types, their properties, and their best applications. Stainless welding rods are crucial for producing strong, durable, and corrosion-resistant welds, and selecting the right one can significantly impact the quality of your project. This article delves into the key considerations when choosing stainless welding rods, providing insights that reflect deep expertise and authority in this specialized field.
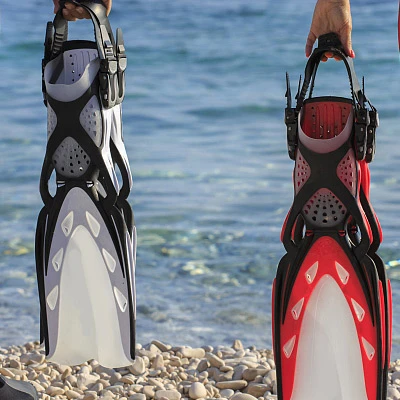
Stainless welding rods, also known as electrodes, are essential in creating robust joins in stainless steel materials. These rods are coated with flux, a substance that aids the welding process by stabilizing the arc and reducing splatter. The most commonly used stainless welding rods include 308, 309, 316, and 347 series, each offering unique properties suited for different types of projects.
When selecting a welding rod, the composition of the base metal is a primary consideration. For instance, type 308 is ideally suited for welding 304 stainless steel, one of the most widely used steels due to its excellent corrosion resistance and formability. This compatibility ensures a strong weld with minimal risk of cracking or corrosion. On the other hand, 309 is often selected when welding different types of steel together, such as stainless to mild steel, offering versatility and strength across various metals.
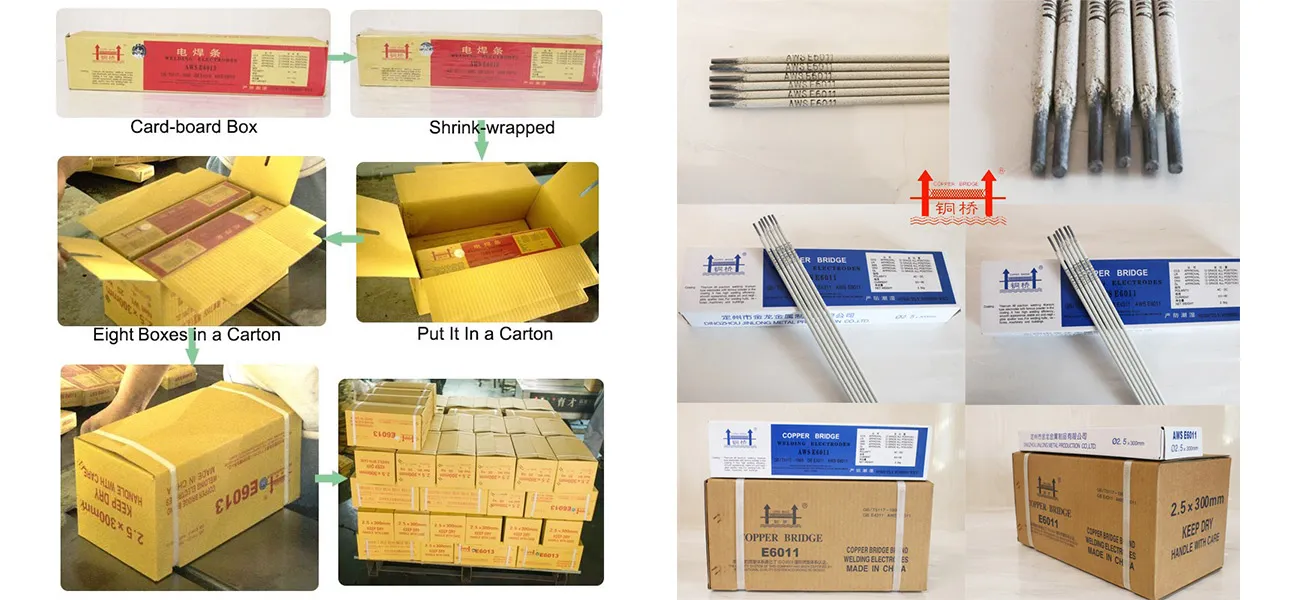
Equally important is the environment in which the welded object will be used. Type 316 rods are often chosen for projects exposed to harsh environments or chemicals, such as marine applications or chemical processing equipment. This is due to their added molybdenum content, which enhances their ability to resist chemical attacks and pitting corrosion. Meanwhile, 347 rods are ideal for high-temperature applications due to their ability to maintain strength and resist grain boundary carbide precipitation.
The diameter of the stainless welding rod also plays a critical role in the welding process. The right diameter affects heat input, penetration, and the overall quality of the weld. Smaller diameters are ideal for thin materials, allowing for greater control and precision. In contrast, larger diameters are suited for thicker materials where deeper penetration is necessary for a robust weld.
stainless welding rod chart
Professional welders should consider the welding position — flat, horizontal, vertical, or overhead — as different rods offer varying levels of performance across these positions. For instance, some rods are designed to be highly effective in out-of-position welding, providing versatility and efficiency.
Furthermore, the welding process itself—whether using MIG, TIG, or stick welding—also determines the appropriate rod selection. Each process has its unique strengths and limitations, affecting everything from ease of use to the final appearance of the weld. TIG welding, for example, is renowned for producing high-quality welds with exceptional finish, making it ideal for ornamental and precision applications.
It's essential to purchase welding rods from reputable suppliers known for quality control and standards adherence. This ensures consistency in the performance of the rods, which leads to better-quality welds. Checking for certifications and compliance with international welding standards also enhances trust in the product.
In conclusion, the selection of stainless welding rods involves a careful analysis of multiple factors, including material composition, environmental conditions, welding position, and the process itself. By understanding these parameters and choosing the right rods, metalworkers can achieve superior results, ensuring the integrity and longevity of their projects. Investing in quality materials and adhering to best practices not only enhances productivity but also builds a reputation for reliability and excellence in the metalworking industry.