Solid wire welding is an essential process in the realm of metal fabrication and manufacturing, offering a robust solution for joining metals with precision and efficacy. This technique, known for its versatility and strength, is widely utilized across various industries, and a deep dive into its application and advantages can equip professionals and businesses with the insights necessary to optimize their welding operations.
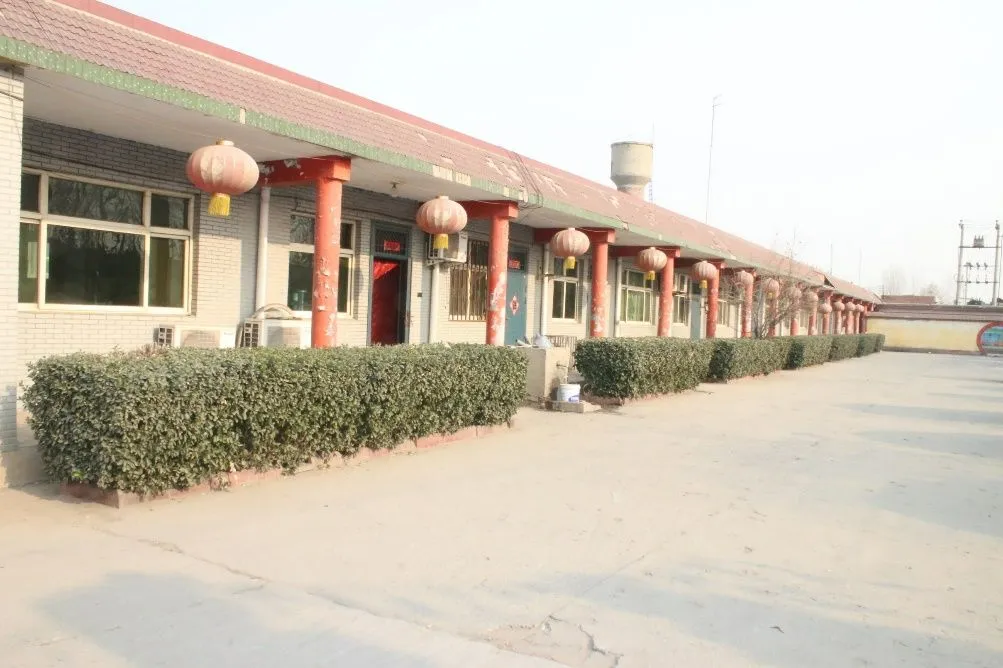
Experience, expertise, authoritativeness, and trustworthiness play crucial roles in understanding the intricacies of solid wire welding. From selecting the right wire to mastering the technique, each step demands a blend of skill and knowledge. This approach ensures both novice and experienced welders achieve optimal results, enhancing the structural integrity and quality of the finished product.
Solid wire welding involves utilizing a continuous wire feed along with a shielding gas to protect the weld from contamination. This method is renowned for its ability to produce clean,
high-strength welds with minimal spatter. In the spectrum of welding techniques, solid wire welding stands out for its efficiency and adaptability, capable of handling a variety of metals including carbon steel, stainless steel, and aluminum.
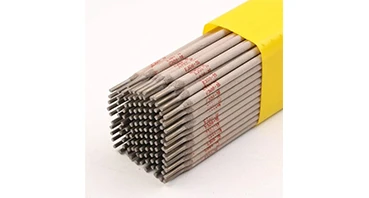
The expertise required for solid wire welding begins with an understanding of material properties and the specific requirements of the welding project. Selecting the appropriate wire diameter and composition is paramount, as it directly influences the weld's strength and durability. Additionally, the choice of shielding gas plays a crucial role in protecting the integrity of the weld; argon-rich mixtures, for instance, are often preferred for their ability to produce smooth and clean finishes.
Mastering solid wire welding also requires proficiency in setting and maintaining the right parameters—amperage, voltage, and travel speed—each of which impacts the heat input and, consequently, the quality of the weld. Experienced welders possess the acumen to adjust these settings in real-time, adapting to variables such as material thickness and joint configuration.
solid wire welding
Authoritativeness in this domain is evidenced by adherence to established welding standards and practices. Organizations such as the American Welding Society (AWS) provide comprehensive guidelines and certifications that uphold the quality and safety of welding operations. Professionals who align their techniques with these standards demonstrate a commitment to excellence and responsibility, reinforcing their credibility in the industry.
Trustworthiness is built through consistent performance and adherence to safety protocols. A trustworthy welding process is one that consistently delivers strong and reliable bonds, ensuring the longevity and safety of the structures in which they are employed. Reliable welds are critical in sectors such as automotive, aerospace, and construction, where structural failure could have catastrophic consequences.
Incorporating solid wire welding into a manufacturing process can significantly enhance productivity and efficiency. The continuous wire feed mechanism reduces downtime associated with replacing consumables, while the minimal cleanup associated with this technique allows for faster workflow transitions between tasks. This efficiency translates into cost savings, making solid wire welding an economically attractive option.
In conclusion, solid wire welding offers a powerful, reliable, and efficient method for metal joining that meets the rigorous demands of modern industry. The process’s success hinges on a foundation of experience, expertise, authoritativeness, and trustworthiness, all of which collectively ensure that welded products not only meet but exceed industry standards. By leveraging these principles, businesses can harness the full potential of solid wire welding, producing superior-quality welds that stand the test of time.