Nickel 99 electrodes have garnered attention in various industries for their distinct properties and versatility, making them indispensable for specific applications. Their unique composition, primarily comprising 99% nickel, endows them with unparalleled features that cater to professional welders, industrial fabricators, and even DIY enthusiasts who demand high precision and reliability.
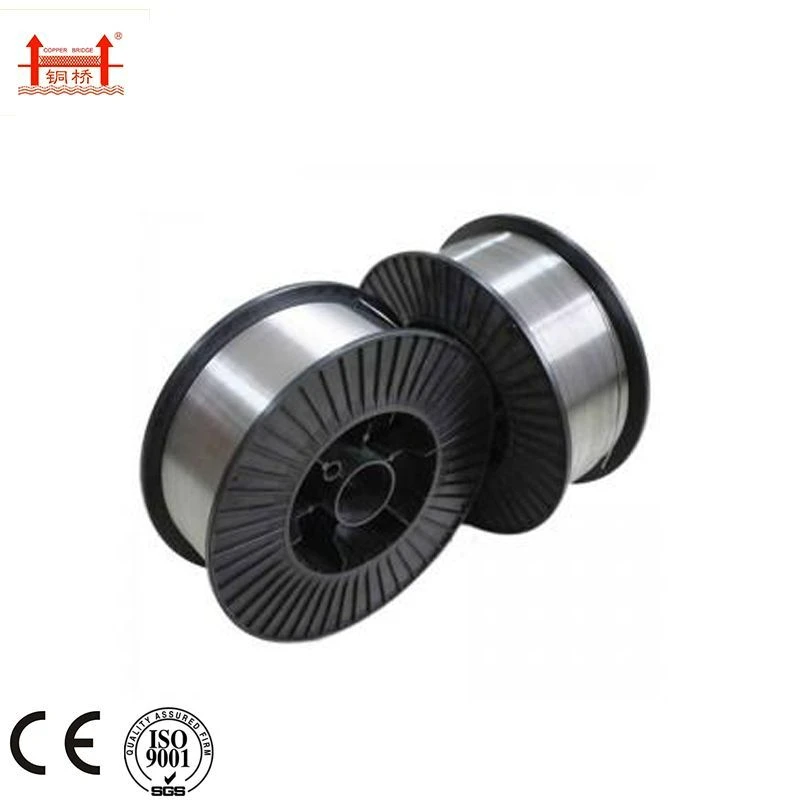
One of the standout characteristics of Nickel 99 electrodes is their exceptional corrosion resistance. This makes them particularly favorable for applications exposed to harsh environments, such as marine settings and chemical processing facilities. The high nickel content inherently combats rust and oxidation, preserving structural integrity over prolonged exposure. Consequently, professionals in these industries frequently prefer Nickel 99 for its longevity and low maintenance costs, thus ensuring safety and operational efficiency.
Furthermore, the ductility and malleability of Nickel 99 electrodes enable superior weld formation with reduced cracking risks. Metallurgical expertise reveals that the electrochemical properties of nickel facilitate smoother and more consistent welds. This trait is instrumental when working with cast irons and is acknowledged in welding communities as a game-changer for joining dissimilar metals or repairing metal parts, including those considered difficult or near impossible to weld with standard electrodes.
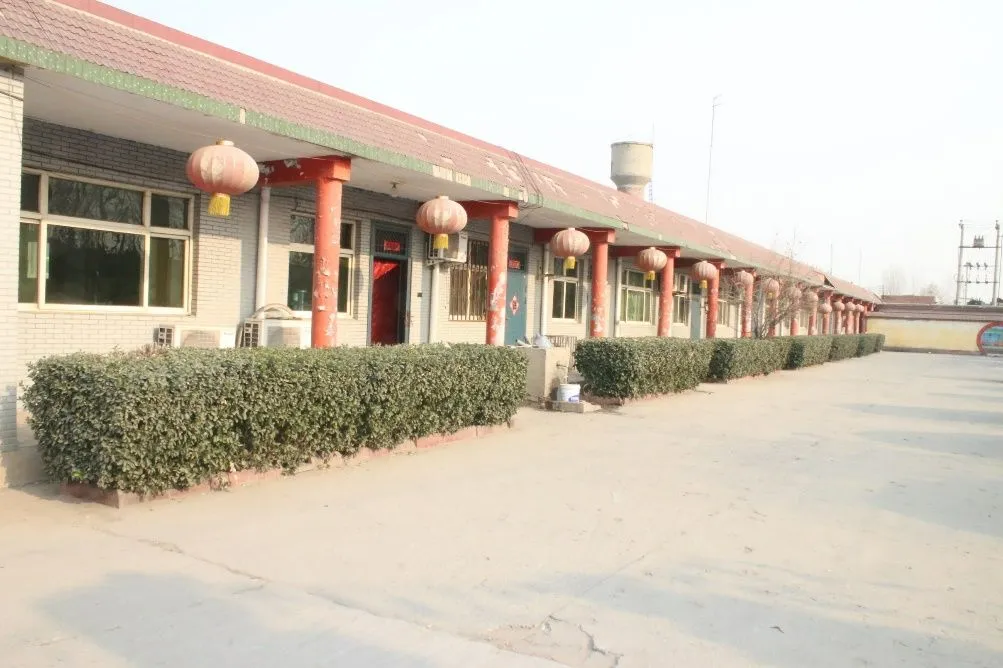
Professional expertise extends beyond basic application. The welding process using Nickel 99 electrodes demands a nuanced understanding of the material properties it is being applied to. Experienced welders emphasize the importance of pre-heating and controlled cooling when working with certain alloys. This mitigates thermal shock, ensures coherence in metal structure, and optimizes the mechanical strength of the weld. Such knowledge demonstrates the level of expertise required to exploit the full potential of these electrodes, inevitably enhancing the credibility and dependability of the outcome.
The reliability of Nickel 99 electrodes is underscored by industry certifications and endorsements from leading manufacturers. Trustworthy brands meticulously test their electrodes to comply with rigorous international standards, ensuring product consistency and predictability in performance. Consumers benefit from transparent documentation and support offered by these manufacturers, reinforcing trust and encouraging informed usage of the product.
nickel 99 electrode
In construction and structural engineering, Nickel 99's role is crucial. The ability to join cast iron to other metals without compromising the integrity of the junction is invaluable, especially in renovating or repairing heritage structures. This capability not only preserves historical aesthetics but also modernizes facilities with invisible reinforcements that extend durability without sacrificing appearance.
Energy sectors also leverage Nickel 99 electrodes for their resilience in high-temperature applications. Pipelines and power plants undertaking repair and maintenance work benefit from the electrode's ability to withstand thermal cycling, minimizing down-time and expanding operational longevity. Expert assessments often recommend Nickel 99 in instances where alternative materials fail to meet the robust demands of contemporary energy infrastructures.
In the medical field, the biocompatibility of nickel-based alloys used in prosthetics and surgical tools translates indirectly to the selection of welding materials. While Nickel 99 electrodes are not used directly in these domains, their stable and inert properties ensure that any indirect application—such as in the manufacture of medical devices that interact with these welds—is uncompromised in terms of patient safety and device efficacy.
Ultimately, the authority of Nickel 99 electrodes within the welding community is well-established. They are celebrated not just for their intrinsic properties but also for the expertise they extract from professionals enhancing their skill set. Reviews and tutorials by welding experts and institutions globally confirm the electrodes’ proficiency across varied scenarios, reinforcing their integral role in contemporary metalworking and fabrication industries.
As developments in material science evolve, Nickel 99 electrodes continue to be at the forefront of innovative applications. Their enduring relevance and adaptability ensure they maintain a significant presence, upheld by the unwavering trust professionals place in their ability to deliver excellence in precise and demanding environments.