Choosing the right welding electrode for joining mild steel to cast iron is a task that demands a nuanced understanding of metallurgy, welding techniques, and material properties. The unique challenges presented by these two materials arise from their distinct compositions and thermal behaviors. Recognizing the significance of these challenges, seasoned welders know that opting for the most suitable electrode is pivotal in ensuring the integrity and longevity of the weld joint.
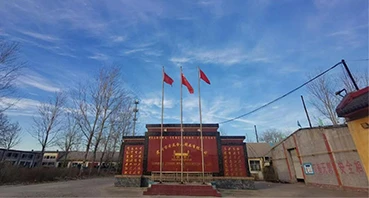
Firstly, it's essential to understand that mild steel and cast iron have very different carbon contents, which significantly affect their weldability. Mild steel,
with its low carbon content (typically less than 0.25%), is highly ductile and easy to weld. In contrast, cast iron generally contains 2-4% carbon, making it brittle and prone to cracking during and after welding due to thermal stress and expansion differences. Therefore, the primary consideration in electrode selection is to mitigate these inherent risks.
Nickel-based electrodes surface as a top choice for such applications. The appeal of nickel as a filler material lies in its superb ability to absorb thermal stresses, thus reducing the likelihood of cracking. Specifically, electrodes like ENiFe-CI or ENi-CI are often recommended. These electrodes offer excellent fusion between the mild steel and cast iron, accommodating the differences in thermal expansion. The high nickel content enhances the ductility of the weld pool and the final joint, ensuring a more robust bond.
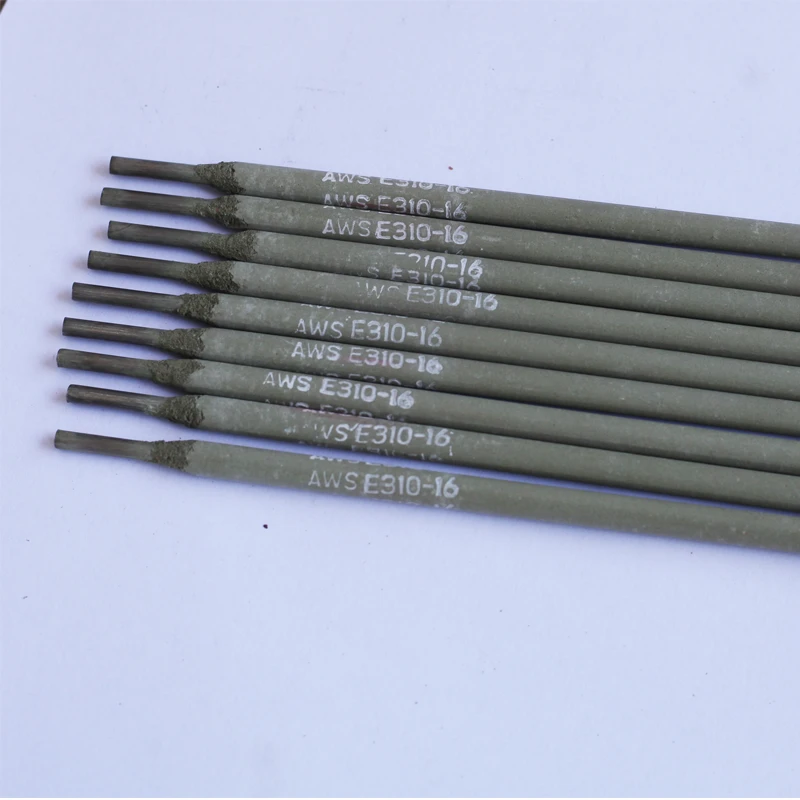
Before striking the arc, preparation is key. Cleaning the surfaces is imperative. Rust, oil, paint, or any other contaminants must be thoroughly removed, as these can lead to porosity or inclusions within the weld. Additionally, preheating the cast iron—usually to about 250 to 500 degrees Fahrenheit—serves to reduce the temperature gradient between the arc and the base material, thereby minimizing the risk of thermal shock and cracking. The preheat temperature may vary depending on the thickness of the materials and specific casting characteristics.
Welding technique further compounds the success of this endeavor. Experts favor stringer beads over weaving, as they concentrate heat input in a narrow area, reducing overall thermal stress. Moreover, employing a low heat input helps in controlling the temperature, thereby preventing the cast iron from reaching a critical temperature range where it becomes more susceptible to cracking.
mild steel to cast iron welding electrode
Post-weld heat treatment (PWHT) is another critical factor in ensuring the durability of the weld. Gradual cooling of the welded joint is advisable. The use of insulation materials like fire blankets to control the cooling rate can help in transitioning smoothly from welding temperature to ambient temperature. This step is crucial as rapid cooling can introduce unwelcome residual stresses and potential fractures in the weld and surrounding base materials.
From an authoritative perspective, adhering to standardized practices outlined by organizations such as the American Welding Society (AWS) and consulting with certified welding inspectors can significantly enhance the credibility and success of a welding project. Utilizing documented procedures and specifications ensures that each step meets the industry’s stringent quality and safety standards.
For professionals involved in the production and maintenance across industries—ranging from automotive to heavy machinery—where the welding of dissimilar metals like mild steel and cast iron is unavoidable, the emphasis on employing the correct electrode cannot be overstated. Maintaining a meticulous approach to electrode selection, material preparation, welding technique, and post-weld treatment guarantees not only a functional joint but also one that withstands the rigors of its intended application.
In conclusion, the complex nature of welding mild steel to cast iron necessitates an informed approach where experience, expertise, and authority blend to build trustworthiness in welding practice. Each weld, influenced by material characteristics and application demands, reinforces the appreciation of specialized knowledge and attention to detail required to perform such tasks successfully. The adept selection and application of welding electrodes thus become more than just a procedural step—they transform into the crux of defining the quality and reliability of the weld.