In the intricate and demanding world of welding, choosing the right electrode is pivotal for achieving high-quality results. When discussing CI welding electrodes, the focus is on understanding their composition, uses, and benefits, with an emphasis on real-world application and expert insights that underline their significance in varied industries.
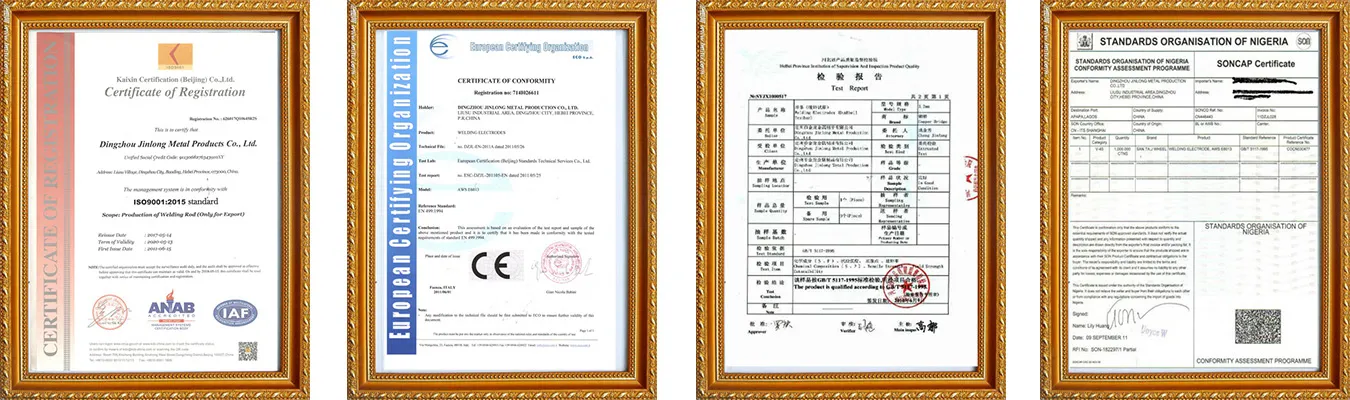
CI welding electrodes, or cast iron welding electrodes, are specifically designed for joining cast iron parts. Cast iron, known for its excellent machinability and wear resistance, presents unique challenges during welding due to its brittle nature. Selecting the right electrode is crucial to overcoming these challenges and ensuring a durable and effective weld.
Experience in using CI welding electrodes reveals that the nickel-based types are often preferred due to their ability to handle the high carbon content of cast iron efficiently. These electrodes minimize cracking risks by absorbing carbon and reducing carbide formation, ensuring a smoother, more reliable weld. Welders frequently encounter situations where post-welding machining is required. In such cases, machinable nickel-iron electrodes emerge as indispensable tools due to their composition, which allows for easy post-process modifications.
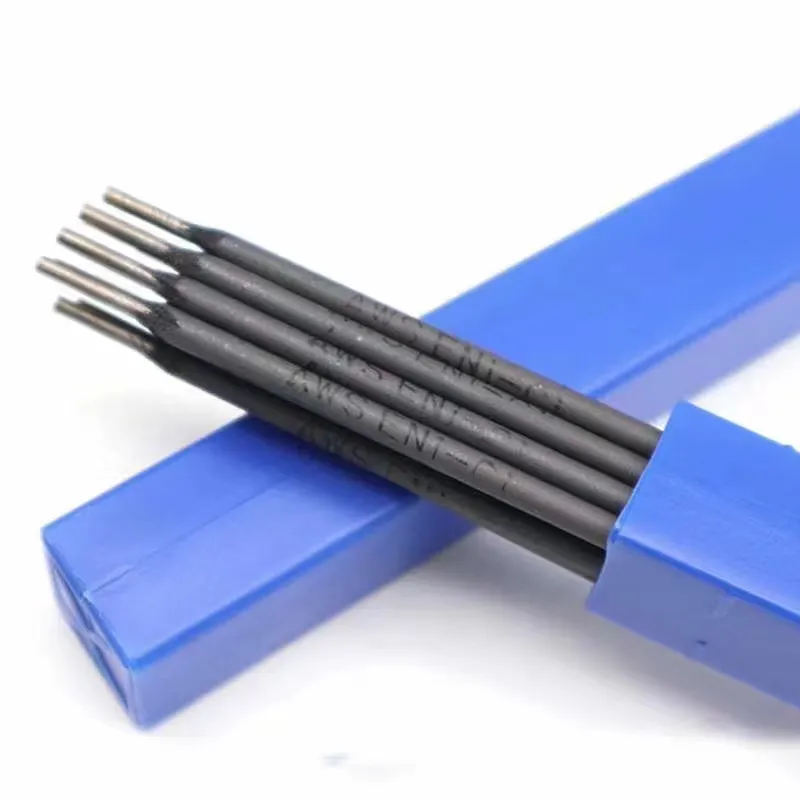
Expertise in the field highlights the importance of preheating and post-weld cooling as key practices when working with CI welding electrodes. The preheating process, typically ranging from 300°F to 500°F, aids in reducing thermal shock and prevents the cast iron from cracking during welding. Post-weld cooling, on the other hand, should be gradual to mitigate the stresses induced by rapid temperature changes. It is through these expert-recommended procedures that welding professionals can achieve optimal results with CI electrodes.
ci welding electrode
The authority of CI welding electrodes lies in their proven effectiveness across various applications. Industries such as automotive, heavy machinery, and construction frequently employ these electrodes to repair engine blocks, gear housings, and pipe fittings. The demand for CI electrodes is often driven by their ability to provide high-strength joints and their versatility in bonding cast iron with dissimilar metals, such as steel. This versatility is a testament to their authoritative standing in the welding community.
Trustworthiness in the performance of CI welding electrodes is established through rigorous testing and adherence to industry standards. Reputable manufacturers ensure their products meet stringent quality checks, providing assurances regarding consistency and performance. The traceability of these electrodes also contributes to their trustworthiness, allowing end-users to rely on high-quality standards and the durability of their applications.
When selecting CI welding electrodes, it is imperative to consider factors such as the type of cast iron being welded, joint design, and the intended application. Knowledgeable welders understand that each project might require a different approach, emphasizing the importance of consulting technical data sheets and manufacturer recommendations. The correct choice ensures not only successful welds but also minimizes downtime and reduces costs associated with material failure.
In conclusion, CI welding electrodes are integral in managing the complexities associated with welding cast iron. Through a blend of practical experience, technical expertise, authoritative usage across industries, and reliance on quality assurance, these electrodes stand out as reliable partners in achieving superior welding outcomes. Industry veterans and newcomers alike must appreciate the nuances of working with these electrodes to harness their full potential and advance the standards of welding technology.