When choosing welding electrodes, one might encounter the designation AWS A5.
1 E6010. To the untrained eye, this may appear as a random alphanumeric sequence, yet it is a key identifier that offers a wealth of information about the electrode's chemical properties, usability, and the nature of work it is best suited for. Understanding the nuances of this designation not only fuels efficiency in welding processes but also enhances safety and durability in the resulting structures.
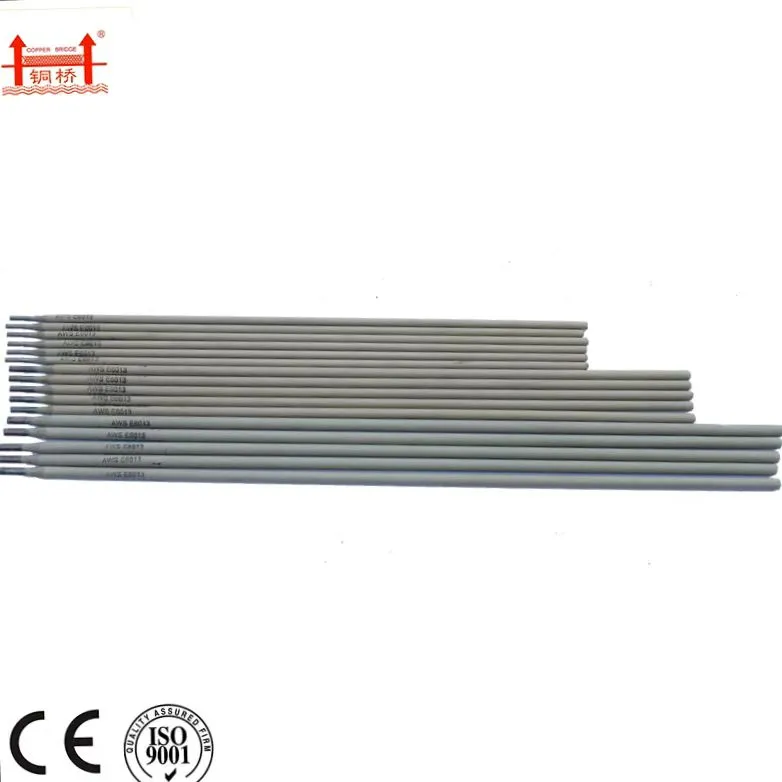
The American Welding Society (AWS) machine-readable standard establishes a systematic framework for welding filler metals classification. The AWS A5.1 E6010 designation falls under this comprehensive umbrella, providing consistency and quality assurance across various environments and applications. With precision and reliability being paramount in welding tasks, choosing the correct electrode is critical.
The E in the AWS A5.1 E6010 identifier signifies an electrode, a key component in the welding process that conducts current, enabling the arc that melds materials. Numbers following this letter provide insights into the electrode's tensile strength potential, positions it can weld, and the type of current with which it operates best.
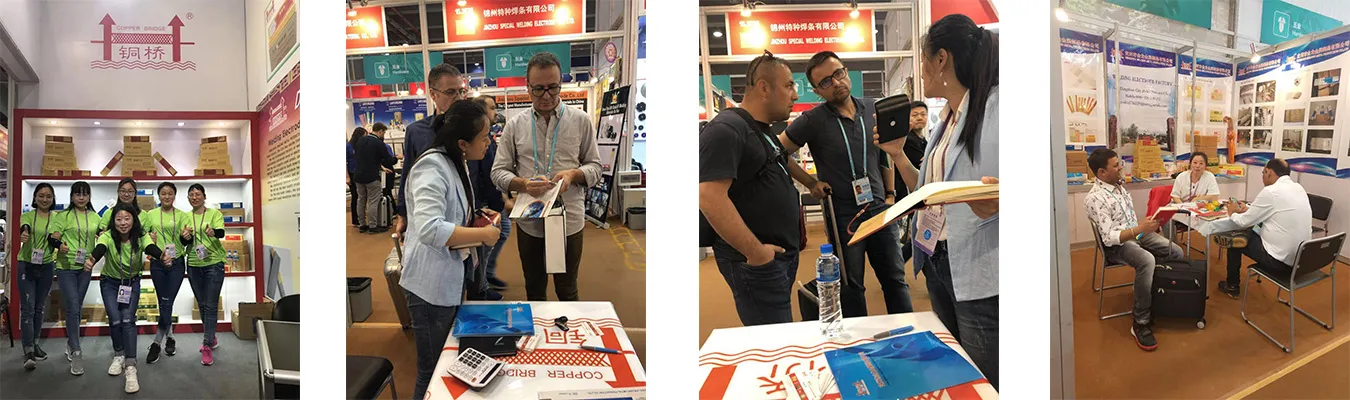
E6010 electrodes possess a tensile strength of 60,000 psi, indicating their capacity to withstand substantial stress before deformation. For welds in construction environments or infrastructure projects, this supports creating enduring and reliable joints capable of withstanding variable and demanding conditions. These electrodes excel in structural fabrications where durability is non-negotiable.
The third digit, 1, showcases versatility in applications, representing the electrode’s capability to weld in all positions flat, horizontal, vertical, and overhead. This adaptability is vital in on-field welding projects, which often demand flexibility without compromising weld quality. E6010 electrodes, therefore, are a reliable choice in complex welding scenarios across diverse industries.
The final 0 in E6010 reveals the necessary current type direct current, with a focus on the electrode's stability and penetration ability. E6010 electrodes are typically characterized by deep penetration and forceful arc, beneficial for welding jobs that involve painted, rusted, or dirty surfaces. They yield strong, high-integrity bonds quickly, thus optimizing productivity in time-sensitive projects.
aws a5 1 e6010
One vital attribute of E6010 electrodes is their cellulose-based coating, which contributes to their deep penetration trait. This coating generates a gas shield during welding, which protects the molten metal's integrity, ensuring consistent, high-quality welds even under less-than-ideal conditions. It gives E6010 electrodes an edge in pipeline welding and construction industries that frequently grapple with adverse environments.
Despite the evident advantages, the effective use of E6010 electrodes necessitates skilled operation. Mastery of techniques such as whip and pause movements is critical to control the rapid solidification and ensure uniformity in the weld deposit. These skills, combined with a sound understanding of welding dynamics, allow operators to maximize the potential of E6010 electrodes, leveraging their unique qualities to achieve exceptional results.
Moreover, safety cannot be overstated in welding operations. The electrodynamics of E6010 may expose operators to spatter and fumes, thus appropriate protective gear and equipment are imperative. Prioritizing safety ensures the workforce can operate at optimum performance levels without compromising health or safety standards.
Incorporating AWS A5.1 E6010 into a welding setup not only adheres to industry regulations but also elevates operational productivity and efficiency. Given the significant implications of poorly executed welds, such as infrastructural failures or costly redesigns, investments in understanding and optimizing the use of quality electrodes is a decision that pays dividends.
In conclusion, the AWS A5.1 E6010 electrode represents more than just a component in welding; it is emblematic of the rigor and precision needed in modern manufacturing and construction sectors. Through understanding each facet of its designation — spanning tensile strength, positional versatility, current requirements, and coating composition — businesses can enhance their operations, ensuring every weld meets the highest standards of precision, strength, and safety. This focus on expertise, authority, and trust underscores a commitment to excellence that aligns seamlessly with both industry expectations and organizational goals.