The 7013 welding rod is a hidden gem in the world of welding, fast gaining attention due to its unique properties that offer reliable solutions to various welding challenges. Understanding its uses not only elevates the quality of fabrication work but also enhances professional welding capabilities.
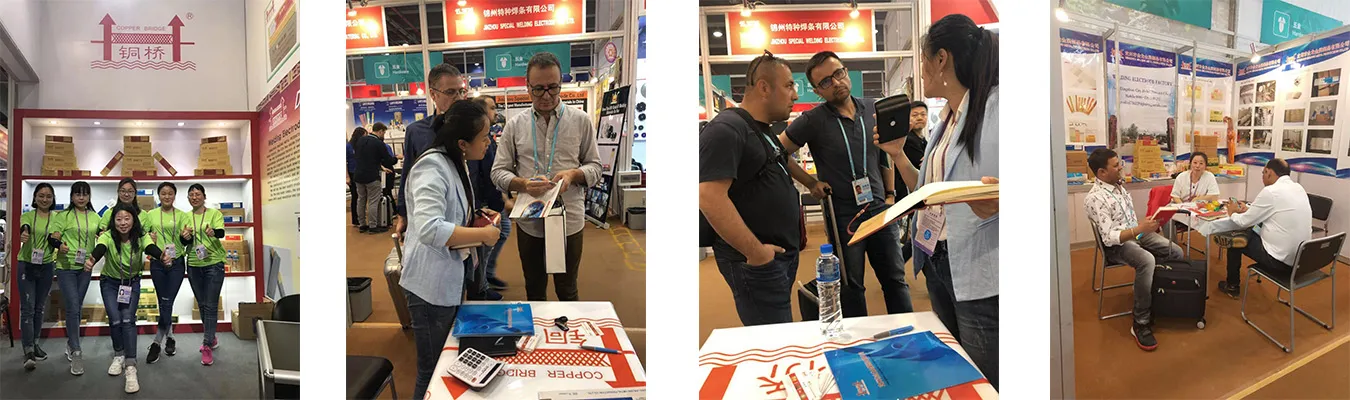
The 7013 rod is particularly lauded for its user-friendly characteristics, making it an attractive choice for both novice welders and seasoned professionals. Its distinctive coating and composition equip it with a smooth arc and minimal spatter, crucial for clean, efficient welds. Ease of use enhances precision, crucial for projects demanding high aesthetic and functional standards.
When tackling structural welding projects, the 7013 rod shines due to its commendable tensile strength and ductility. It can handle high-stress environments, making it ideal for constructing buildings, bridges, and other infrastructural elements where durability is paramount. This strength ensures welded joints resist fatigue and vibration, extending the lifespan of the structure.
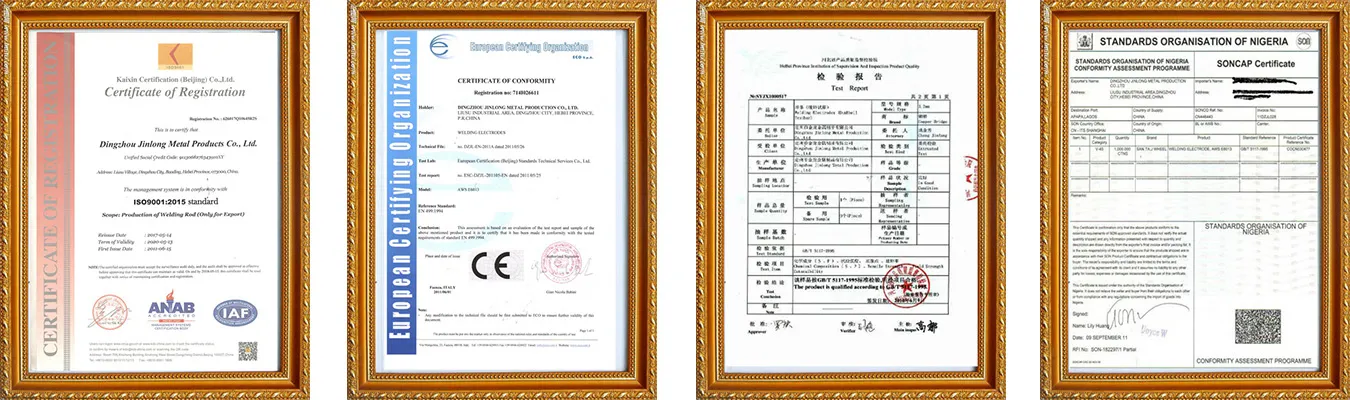
Additionally, this rod’s performance on vertical and overhead welds offers an advantage in automotive repair and shipbuilding. Its formulation enables it to perform consistently well in awkward positions, a common challenge in these industries. Welders can rely on the 7013 rod to deliver excellent penetration and consistent bead appearance, ensuring both safety and aesthetics.
The agricultural sector also benefits significantly from the versatility of the 7013 welding rod. Farm equipment and machinery often encounter harsh conditions, necessitating repairs and fabrication that can withstand exposure to various elements. The 7013 rod provides the durability required for such applications, allowing for maintenance and fabrication that improve equipment longevity and functionality.
7013 welding rod uses
In the manufacturing sector, where production efficiency and quality are critical, the 7013 welding rod appeals due to its fast-freeze characteristics. Quick-setting welds reduce downtime, while its ability to produce high-quality welds minimizes the need for rework. Therefore, manufacturers seeking to improve productivity and weld quality often rely on this versatile welding rod.
Moreover, the 7013 welding rod finds its place in decorative metalwork, where detail and finish are as important as structural integrity. Artists and fabricators appreciate this rod's ability to produce clean welds, which minimize grinding and finishing, preserving intricate details and reducing preparation time. This makes it a preferred choice for creating pieces where aesthetics cannot be compromised.
From a safety perspective, the 7013 welding rod’s relatively low fume emission contributes to a healthier working environment. This aspect is crucial for welders operating in poorly ventilated spaces. By choosing this rod, welding operations can adhere to safety regulations without compromising on quality or efficiency.
Investing in 7013 welding rods is not just a decision for a specific task. It is about expanding the toolkit with a versatile, reliable option poised to address a variety of welding challenges with excellence. Whether the priority is structural integrity, efficiency, or aesthetics, this welding rod stands ready to meet diverse demands.
In conclusion, the 7013 welding rod is a testament to innovation in welding technology. It leverages an excellent balance of user-friendliness, strength, and versatility. Welders across industries can improve their craft by integrating the 7013 rod into their repertoire. By doing so, they not only enhance their work quality but also increase the safety and efficiency of their operations. The ever-evolving demands of welding require solutions that adapt seamlessly, and the 7013 welding rod delivers just that, establishing itself as an indispensable asset in the toolkits of those who shape the world with metal.