Selecting the right welding rod is crucial for any welding project, as it determines the quality, strength, and usability of the finished joint. Among the most popular options are the 6011 and 7018 welding rods, each possessing unique characteristics that suit different applications. This article delves into the essential qualities of these rods, helping you make an informed decision while emphasizing the importance of firsthand experience, professional expertise, authority, and trustworthiness in the field of welding.
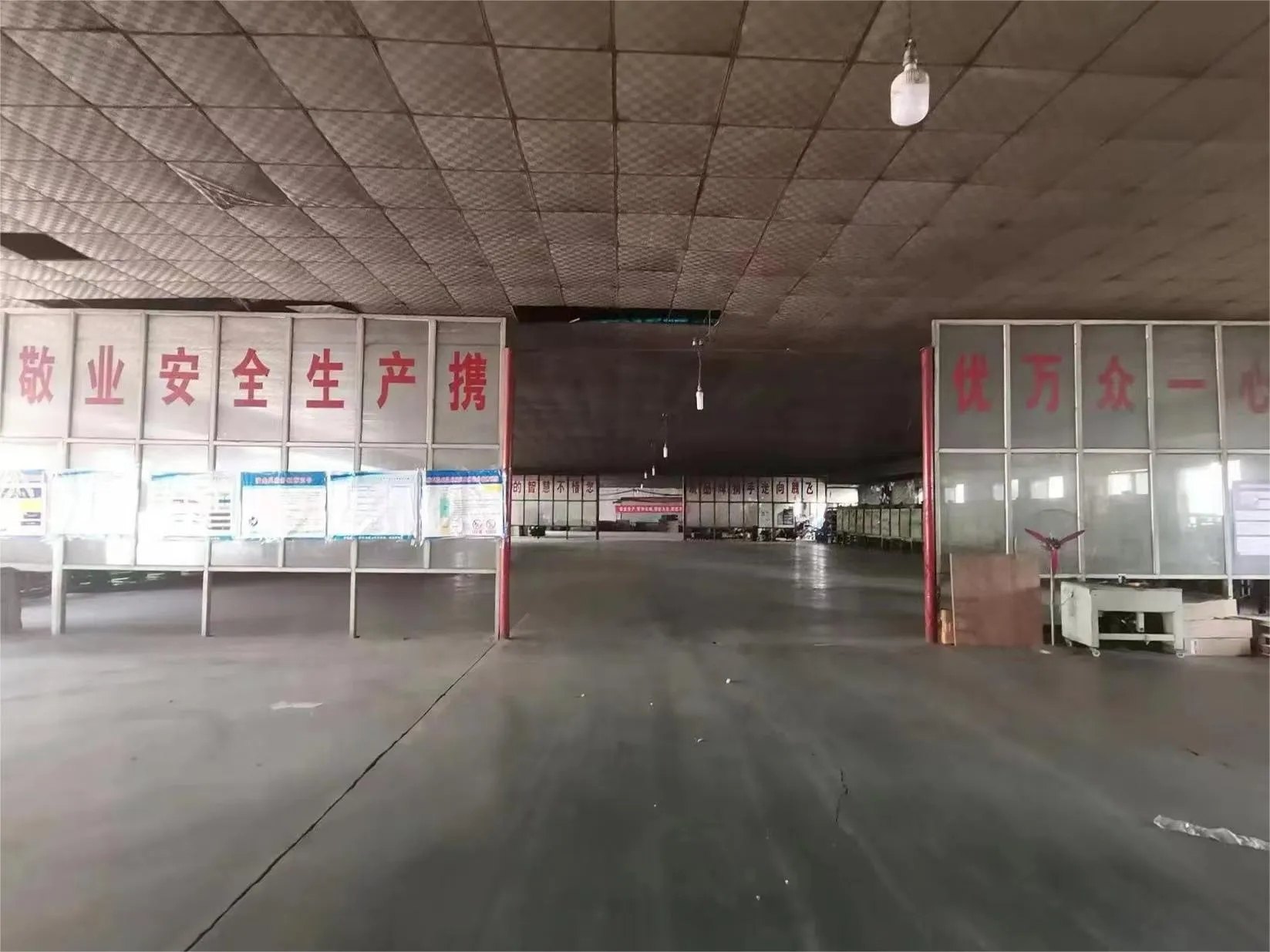
The 6011 welding rod is renowned for its versatility and adaptability in various welding environments. One of its standout features is the deep penetration it provides, making it particularly effective for welding on rusty, dirty, or painted surfaces. This makes the 6011 an excellent choice for maintenance and repair work, where conditions may not always be ideal. Additionally, the 6011 performs exceptionally well with both AC and DC currents, providing further flexibility for welders working with different types of welding machines.
Working with 6011 rods is an experience in itself. Welders often appreciate how it allows for great travel speed, which is beneficial for efficiency without compromising the integrity of the weld. The ability to maintain a stable arc further underscores its utility in less controlled environments, making it a staple in workshops and field operations alike. For beginners, mastering the 6011 can provide a solid foundation in arc welding due to its forgiving nature regarding surface conditions and easy slag removal.
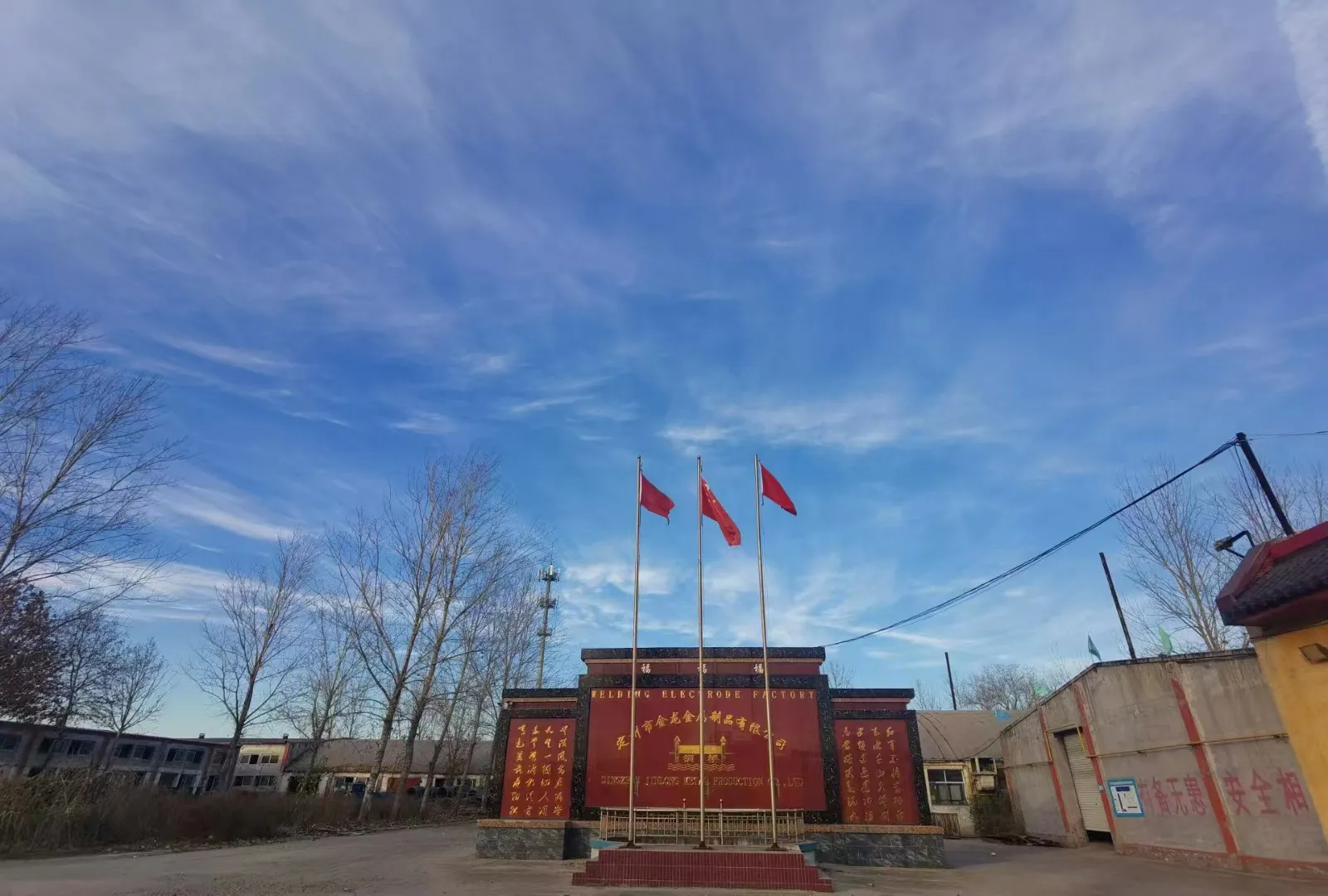
In contrast, the 7018 welding rod is a low-hydrogen electrode, famous for creating smooth and aesthetically pleasing welds. Its popularity is anchored in the high tensile strength it provides, which is critical for structural steel applications. The 7018 is often the go-to rod for critical welding projects that demand reliability and strength, such as bridges, pressure vessels, and high-rise constructions. This makes it a favorite among professionals who prioritize weld quality and structural integrity.
6011 or 7018 welding rod
7018 rods excel in producing less spatter and easier slag removal, which contributes to clean and neat welds. However, it requires more precise handling, as it generally works best with DC current. For those new to the 7018, maintaining proper storage is essential to prevent moisture absorption, which can lead to hydrogen-induced cracking. Adequate training and adherence to storage guidelines are paramount, underscoring the rod's demand for professional expertise and robust knowledge.
Ultimately,
choosing between the 6011 and 7018 welding rods depends on your specific project requirements and working conditions. The 6011 rod is optimal for work that involves adverse surface conditions or accessibility issues. Meanwhile, the 7018 is unrivaled in applications where weld quality and appearance are non-negotiable, requiring expertise that aligns with its specific usage demands. Both rods play indispensable roles in the arsenal of a welder, reflecting the critical intersection of experience and expertise in the field.
A comprehensive understanding of these welding rods accentuates your ability to execute projects with authority and trustworthiness, ensuring that your welding endeavors meet professional standards. These rods not only demonstrate the diversity of material properties but also highlight the importance of selecting the right tools based on informed choices underpinned by industry knowledge. Whether you're engaged in a high-stakes industrial welding task or a routine repair job, the 6011 and 7018 rods offer the reliability and performance necessary to complete tasks confidently.