Embarking on the journey of welding can be both intricate and rewarding, especially when delving into the specialized realm of 3/32 stainless steel welding rods. These rods, renowned for their precision and reliability, are indispensable tools for experts who demand high quality and durability in their projects. Understanding their unique characteristics and applications is crucial for anyone seeking to excel in the field of welding.
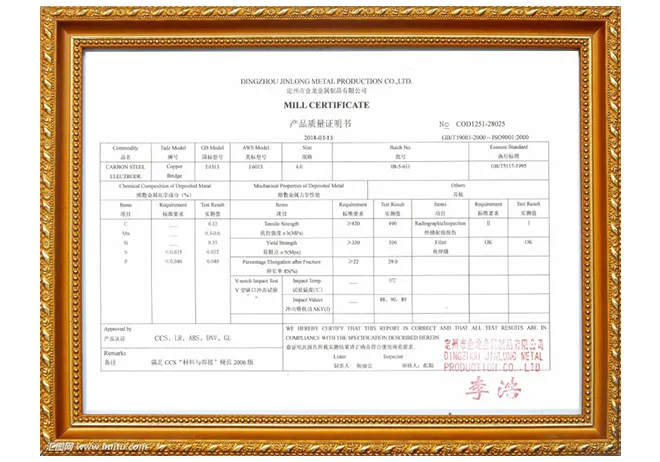
Selecting the right 3/32 stainless steel welding rod can significantly influence the quality and durability of your welds. These rods are typically used in scenarios requiring strong resistance to corrosion and oxidation, a quality that stainless steel is renowned for. The 3/32 size, in particular, is favored for its versatility and ability to provide precise welds in both thin and medium gauge materials, a perfect choice for tasks that demand meticulous detail.
The chemical composition of these rods ensures superior toughness and strength. Typically engineered with a core of stainless steel alloy, they are often coated with a flux that facilitates the welding process by creating a protective gas shield and slag during welding. This characteristic aids in the prevention of atmospheric contamination, which can compromise the integrity of the weld. The rods are usually engineered to perform efficiently with alternating current (AC) or direct current (DC), offering versatility in different welding machines and settings.
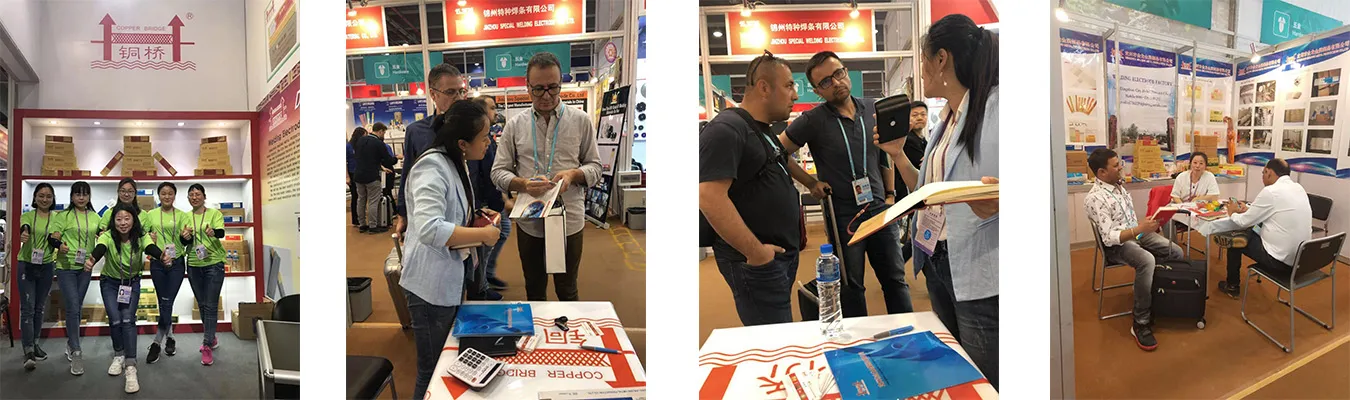
Expert welders often choose 3/32 stainless steel rods for projects that require a clean, aesthetic finish. For instance, they are commonly employed in the food and beverage industry, where equipment must meet stringent hygiene standards and maintain a sleek appearance. The automotive and aerospace sectors also rely on these rods for constructing components that withstand harsh environmental conditions without succumbing to rust or decay.
In terms of technique, welding with 3/32 stainless steel rods demands precision and skill. The welder must meticulously control the heat input to avoid warping or weakening the material. It’s important to maintain a balanced approach, ensuring the weld pool remains stable and manageable. This requires practice and a deep understanding of how temperature affects the stainless steel at a molecular level.
3 32 stainless steel welding rod
Another factor critical to the welding process is the preparation and cleaning of the base materials. Stainless steel surfaces must be free of contaminants such as oil, grease, or dirt, which can otherwise lead to poor weld quality. The completion of each weld pass should be followed by slag removal and cleaning to prepare for subsequent passes, thus ensuring a strong bond and high-quality finish.
Investing in the right equipment is pivotal. Quality welding machines, appropriate safety gear, and essential tools like wire brushes and grinding wheels should be prioritized to achieve optimal results with 3/32 stainless steel rods. Moreover, maintaining a well-ventilated workspace is vital for safety and efficacy, as certain fumes emitted during the welding of stainless steel can be harmful if inhaled over prolonged periods.
In terms of product availability, prominent brands offer 3/32 stainless steel welding rods, and expert reviews and feedback can serve as a reliable guide for selection. It is beneficial to consult with local suppliers who understand your specific project requirements and can provide insights based on your technical needs.
Ultimately, the success of using 3/32 stainless steel welding rods hinges on a combination of skilled technique, appropriate equipment, and a nuanced understanding of material properties. Welders who master these elements can produce high-quality, reliable, and aesthetically pleasing welds that stand the test of time. As technology advances and new methods and materials are introduced, keeping abreast of current trends and developments in welding rod technology is essential for maintaining an edge in this dynamic field.