Choosing the right welding rod for mild steel (MS) material is essential for ensuring strength, durability, and quality in any welding project. As an experienced welder or a newcomer looking to master the craft, understanding the nuances of welding rods can significantly impact your project outcomes.
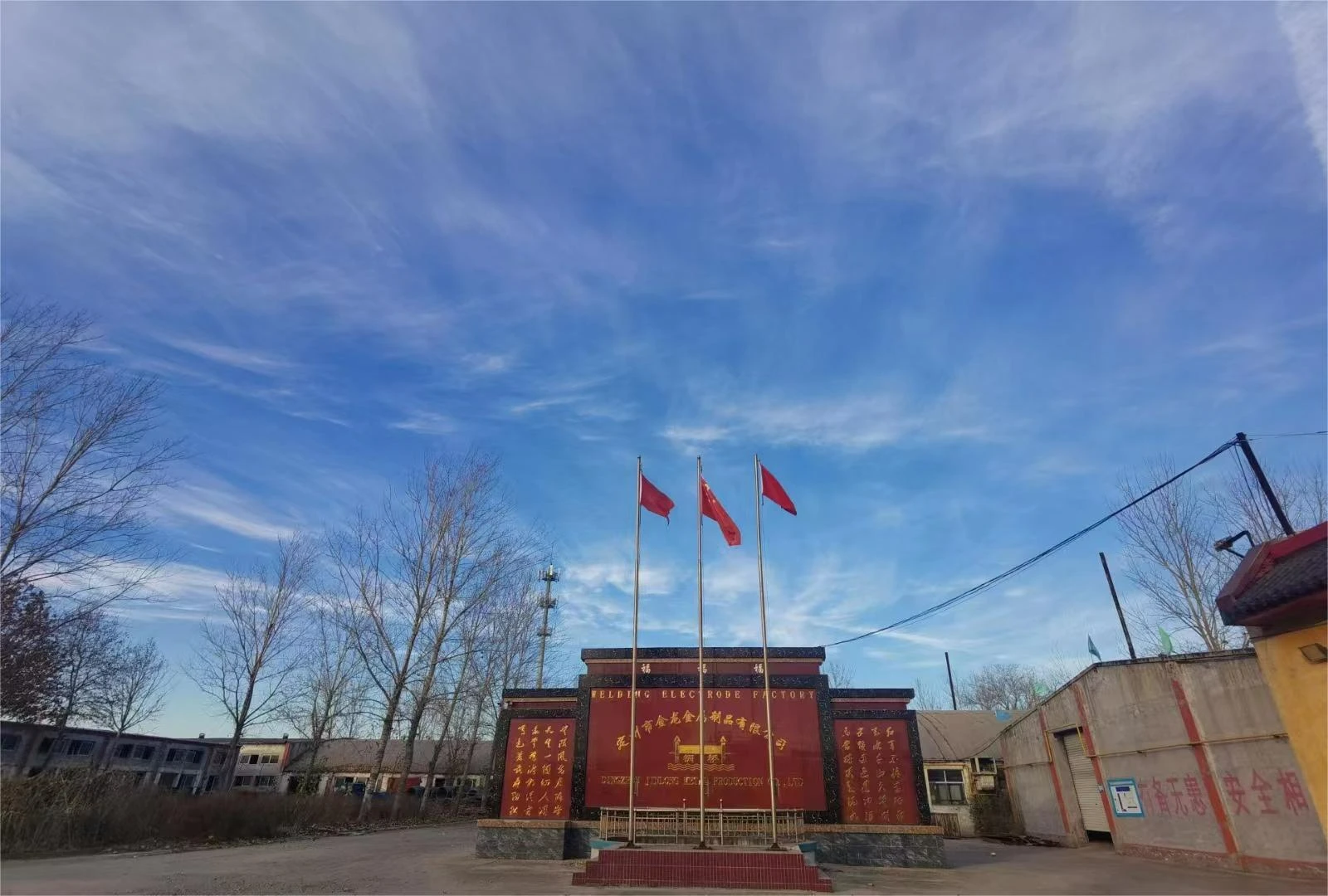
Mild steel, known for its excellent flexibility and versatility, requires specific welding rods that are compatible with its mechanical properties. E6013 and E7018 are two of the most commonly used electrodes for mild steel. Each has its distinct features tailored for varying welding conditions and preferences.
E6013 welding rods are renowned for their smooth, stable arc and ease of use. They are ideal for welding thin to medium sections of mild steel because of their shallow penetration. What sets E6013 apart is its ability to produce a soft arc with minimal spatter, making it an excellent choice for beginners. Moreover, these rods are highly adaptable, functioning well with both AC and DC power sources. This characteristic is especially advantageous when working in environments where power source availability might be inconsistent.
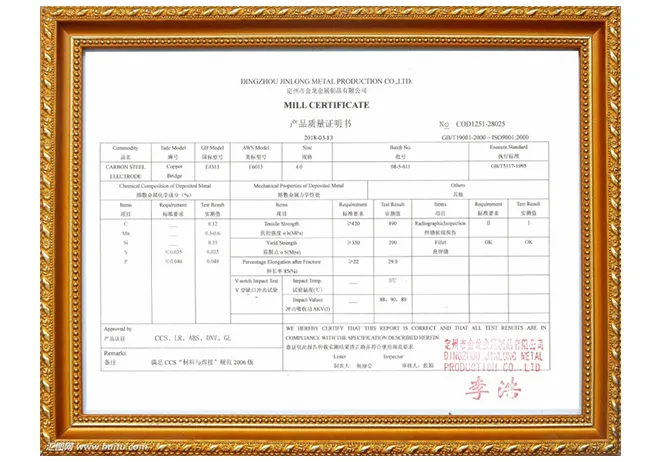
For projects requiring high durability and resilience, especially in critical structural applications, E7018 rods are preferred. These rods are low-hydrogen electrodes designed to minimize hydrogen-induced cracking. E7018 rods are engineered for excellent mechanical properties, particularly their high tensile strength. They are best suited for thicker sections of mild steel and projects that demand a highly reliable weld. The E7018 rods require a bit more attention to storage conditions, as they need to be kept dry to maintain their low-hydrogen characteristics. Nonetheless, their capacity to produce strong welds with a clean, smooth finish makes them a favorite among professional welders.
Welding mild steel with these rods isn't just about choosing between E6013 and E7018; it's about understanding the specific needs of your project. Consideration of factors such as the position of welding, whether vertical or horizontal, the operating environment, and post-weld treatment requirements are crucial. For instance, in positions where vertical or overhead welding is necessary, E7018's superior slag coverage and smooth arc transfer can make the process more manageable.
welding rod for ms material
The expertise in handling these rods extends beyond just selection. Proper technique includes maintaining the correct angle, travel speed, and arc length. For E6013, its forgiving nature in terms of travel speed allows welders a bit more leeway in adjustment, while E7018 requires precise control to harness its full potential due to its heavy slag formation.
Reliability and authority in welding practices can also be enhanced through a commitment to ongoing learning and adaptation to new techniques and technologies. This includes staying updated with the latest advancements in welding tools and materials. Regularly consulting with industry experts, engaging with welding communities, and participating in workshops and certifications can further elevate one’s proficiency and credibility in this field.
Trustworthiness in welding quality is built on a foundation of meticulous preparation and execution. This incorporates pre-weld preparation, ensuring precise fit-ups and thorough cleaning of base metals. Post-weld care, such as inspection and finishing, ensures that the welded structure meets the desired standards and specifications.
In conclusion, selecting the optimal welding rod for mild steel hinges on understanding the project's specific requirements and mastering the application of the rods in various scenarios. Whether opting for E6013 for its versatility and ease or E7018 for robust, high-strength applications, the right choice can significantly influence the success and quality of the welding project. For any welder aspiring to achieve excellence, consistent practice, knowledge sharing, and continuous education are key pillars that support the journey toward becoming a trusted authority in the welding domain.