Precision, durability, and efficiency are paramount in the realm of welding, where the choice of electrodes can significantly impact the quality of work. Among the numerous electrodes available, the 6013 welding electrode stands out due to its versatile application and favorable characteristics. Understanding its specifications is crucial for both amateurs and seasoned professionals aiming to achieve high-quality welds.
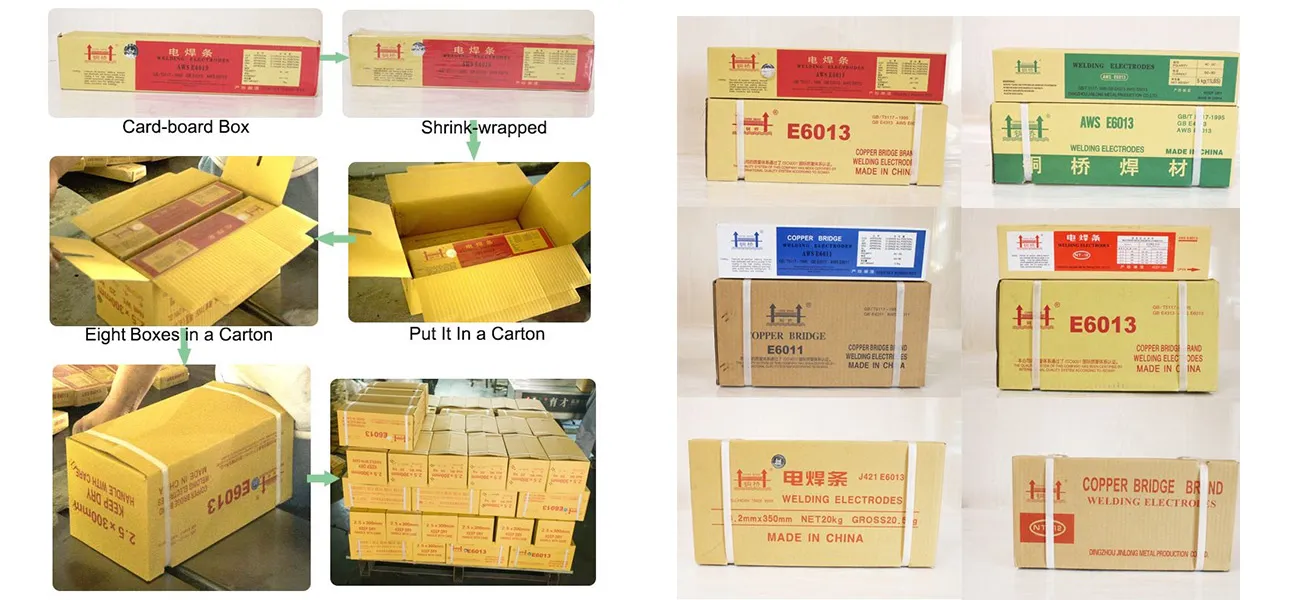
The 6013 electrode is distinguished by its composition and coating, which contribute to its unique properties. Classified under the AWS (American Welding Society) designation, the ‘60’ indicates a tensile strength of 60,000 pounds per square inch. This strength is ideal for welding mild steel and ensures robust welds that can withstand substantial stress. The ‘1’ in 6013 signifies its all-position capability, which provides welders with the flexibility to work effectively whether the project requires flat, horizontal, vertical, or overhead welding positions. The final digit, ‘3’, points to its rutile coating, known for facilitating smooth welds with minimal spatter and a fine finish.
One of the critical aspects of the 6013 electrode is its ease of use. This electrode type is celebrated for its ability to work on less-than-perfect surfaces, making it possible to weld through rust, paint, or minor surface contaminants without compromising the integrity of the weld. Such versatility is invaluable in fieldwork and repair situations where surface cleanliness is challenging to maintain. This aspect enhances its reliability and trustworthiness in demanding environments.
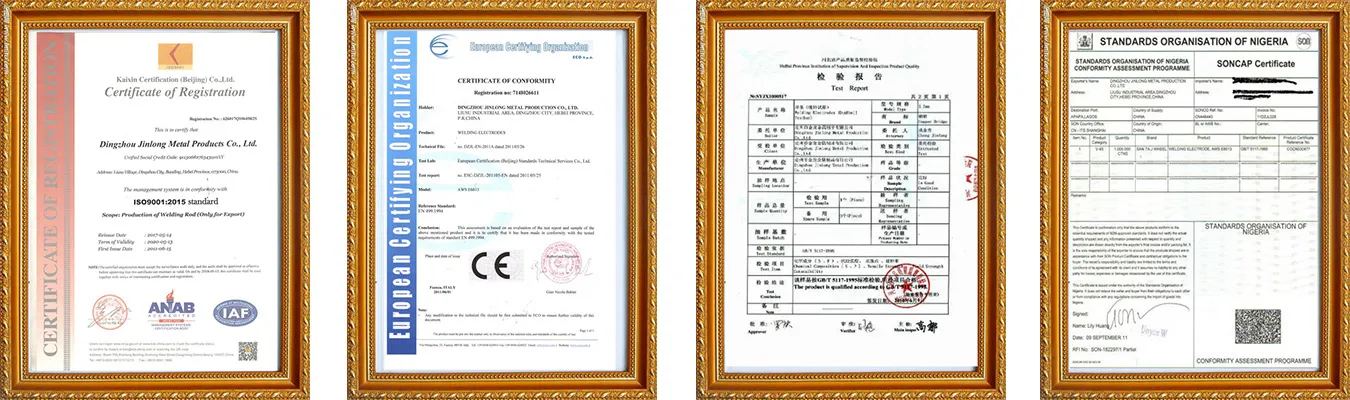
From a professional standpoint, the 6013 electrode's smooth and stable arc makes it highly regarded for aesthetic welds. The electrode produces an appealing bead profile with shallow to medium penetration, which is ideal for projects requiring a clean finish without deep and aggressive penetration that might compromise thinner materials. Therefore, it is often the preferred choice for welding thin sheet metal, automotive bodywork, and tubular structures, where precision and appearance are as critical as strength.
welding electrode 6013 specification
Safety is another domain where the 6013 specification excels. Its rutile-based flux coating not only aids in stabilizing the arc but also generates a protective slag that shields the molten weld pool from atmospheric contamination, thus ensuring a sound weld. This protective feature minimizes the inclusion of oxides and nitrides in the weld, preserving its strength and integrity. Moreover, the slag is readily removable, contributing to a cleaner work environment and reducing post-weld cleanup time, which enhances productivity.
In addressing professional demands, the 6013 electrode presents itself as an authoritative solution in the welding industry. Its consistent performance across various welding conditions has cemented its reputation among industry veterans. Welding technicians and engineers rely on its reliable performance to meet the rigorous standards of construction, repair, and maintenance tasks.
In conclusion, the 6013 welding electrode embodies a blend of strength, application versatility, and aesthetic capability. It stands as a testament to the sophisticated engineering and design knowledge that underlies modern welding technology. Recognized for its uniquely balanced properties, it continues to serve as an indispensable tool for achieving meticulous and durable welds, backing its authoritative role in welding applications worldwide. For those committed to delivering superior craftsmanship, the 6013 electrode remains a trustworthy choice, supported by years of innovative development and field-tested performance.