TIG welding with stainless steel electrodes is an advanced welding technique revered for its precision and the high-quality welds it produces. As an experienced welder with years of practice, I can attest to the importance of mastering this process to ensure optimal results, particularly when dealing with the unique properties of stainless steel.
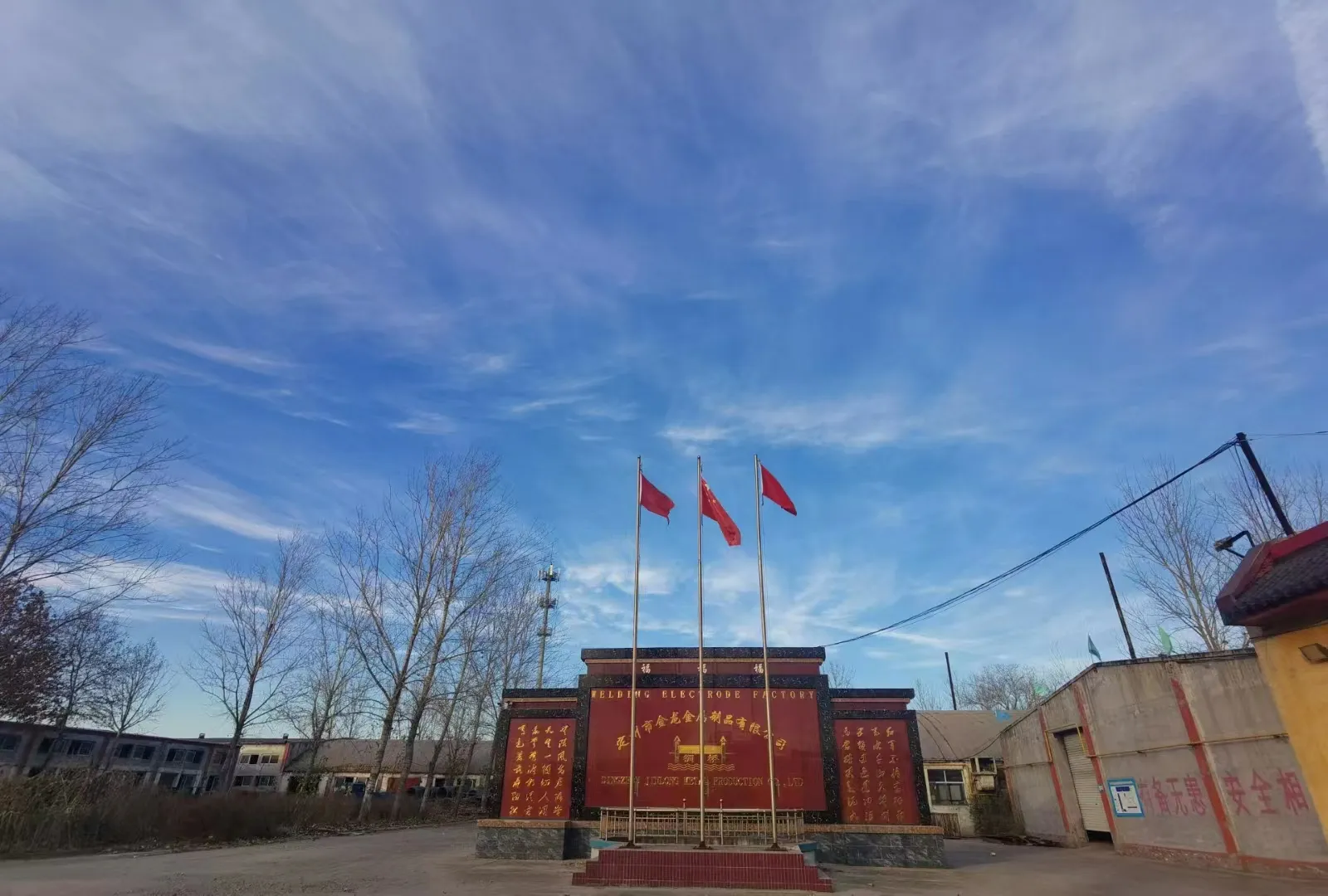
One of the key challenges faced when TIG welding stainless steel is managing heat input. Stainless steel, due to its low thermal conductivity, tends to retain heat, which can lead to warping or sugar contamination on the backside of the weld if not adequately controlled. Utilizing a lower amperage setting is critical to prevent these issues while maintaining a steady hand to ensure smooth and consistent welds. Unlike other metals, stainless steel demands a distinct balance between heat input and weld speed to prevent distortion and preserve the material’s corrosion resistance.
Choosing the correct electrode is another fundamental consideration in TIG welding stainless steel. A common choice is the thoriated tungsten electrode, appreciated for its durability and ability to handle high amperage. However, with growing awareness regarding health and environmental impacts, welders are increasingly turning to alternatives like ceriated or lanthanated tungsten, which provide comparable performance while being safer to use. Selecting the right electrode is paramount not only for the quality of the weld but also for ensuring operational safety and efficiency.
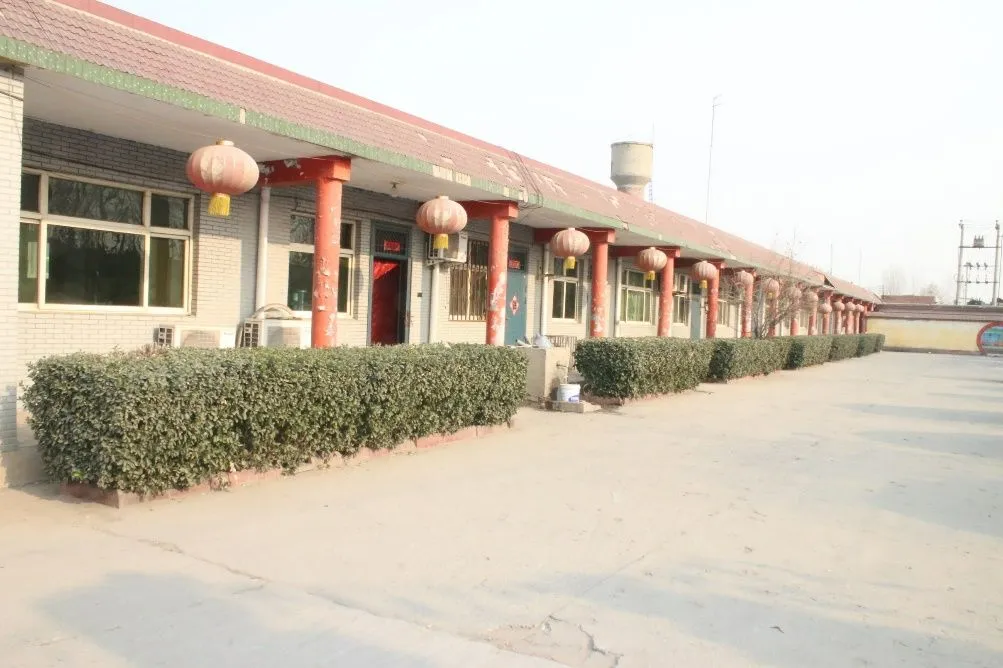
From a technical standpoint, filler material selection can significantly influence the weld’s quality. For stainless steel, it is essential to choose a filler rod that matches the base material to maintain its corrosion-resistant properties. For instance,
when welding 304 stainless steel, using 308L filler material is typically recommended. This strategy ensures the weld area does not become the structure’s weak point. Moreover, maintaining a clean workspace and ensuring all materials are free from contaminants cannot be overstated, as any impurities can compromise the quality and strength of the weld.
tig welding stainless steel electrode
Shielding gas choice plays a crucial role in the TIG welding process as well. Argon is commonly used due to its versatility and ability to provide a stable arc. For enhanced performance, especially in precision applications or when welding thicker stainless steel sections, a mixture of argon with a small percentage of hydrogen might be employed. This blend improves penetration and can increase welding speed. Nonetheless, careful attention to concentration is necessary to prevent embrittlement.
Quality TIG welding is as much about preparation as it is about execution. Prior to starting a weld, it is crucial to ensure that the stainless steel surfaces are free from oils, grease, and any form of oxidation. Employing a stainless steel brush or dedicated cleaning tools will assist in preparing the metal, thereby reducing the likelihood of defects in the weld.
While technique and equipment are vital, it’s the welder's expertise that ultimately determines the success of a TIG welding project. Developing a steady hand, practicing the control of the TIG torch, and having an intimate understanding of the behavior of stainless steel under heat are skills honed over years of experience. These proficiencies, combined with the correct tools and configurations, make for welds that are not only structurally sound but also aesthetically pleasing.
In conclusion, TIG welding stainless steel with the right electrodes is a nuanced craft that demands attention to detail, the right materials, and practiced skill. For any professional seeking to produce impeccable welds, understanding these factors is essential. By covering all aspects from electrode selection to preparation procedures, the meticulous welder can ensure not only the integrity and longevity of the weld but also uphold the highest standards of safety and quality.