Selecting the right material and technique for welding projects plays a crucial role in determining the outcome, longevity, and strength of the weld itself. TIG welding, or Tungsten Inert Gas welding, especially when working with stainless steel, stands out due to its precision and reliability. If you're exploring quality welds for industries such as automotive, aerospace, or even food processing, understanding the intricacies of TIG stainless welding proves invaluable.
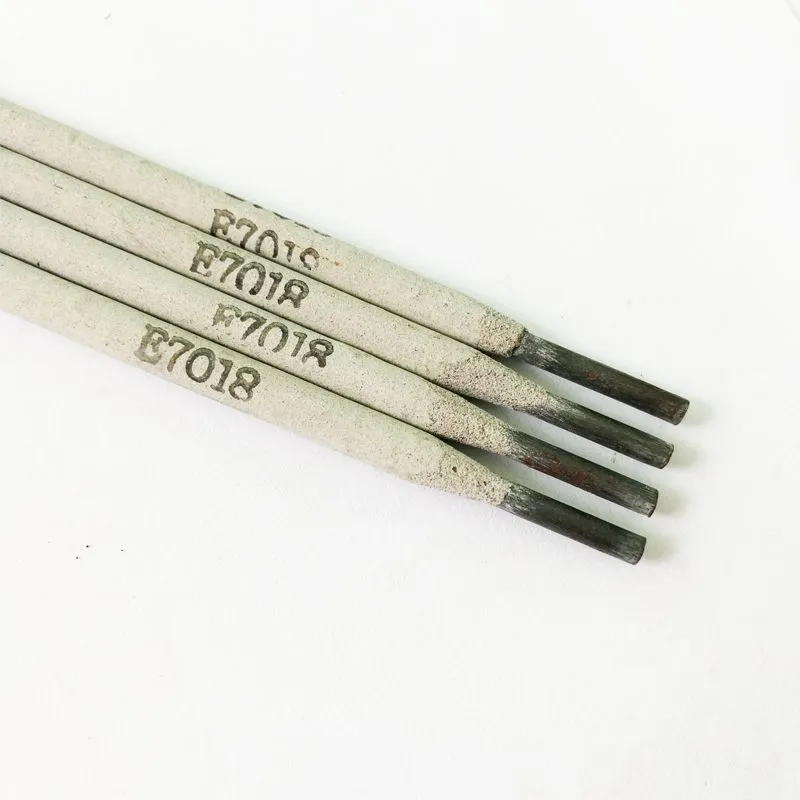
TIG stainless welding is a revered technique among professionals for its ability to produce clean, high-quality welds with excellent aesthetics and minimal spatter. The technique involves using a non-consumable tungsten electrode, which ensures that the weld pool remains uncontaminated, a key consideration when working with materials like stainless steel that demand both structural integrity and an immaculate surface finish.
Experience is the backbone of mastering TIG welding with stainless steel. Setting the correct parameters, such as the optimal current, which for stainless typically ranges between 50 to 100 amps depending on thickness, requires hands-on experience. Veteran welders appreciate how TIG welding offers control over the heat input, allowing them to minimize the risk of distortion and ensuring that the chromium oxide layer in stainless steel remains intact. This layer is essential for corrosion resistance, a definitive attribute of stainless steel that makes it sought after in many industries.
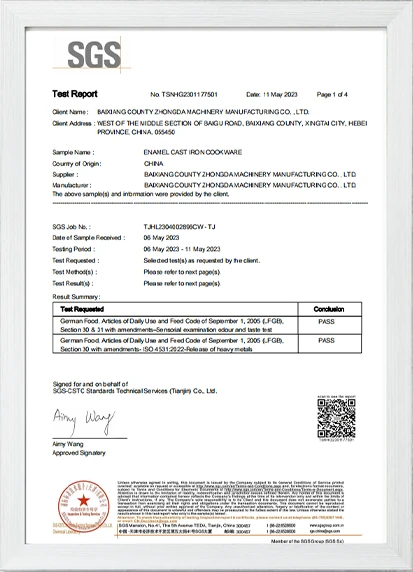
Expertise in TIG welding stainless requires a nuanced understanding of the material's thermal conductivity and expansion properties. Stainless steel has a lower thermal conductivity than other metals like aluminum, meaning it retains heat longer, and this knowledge helps welders adjust their technique accordingly. Experts often employ back purging, shielding both sides of the weld with an inert gas, usually argon, to achieve a more robust and oxidation-free outcome. This attention to detail not only enhances the weld’s strength but also its aesthetic finish, a crucial factor in high-end manufacturing.
tig stainless
Authoritativeness in this domain stems from leveraging technology and advanced methodologies. Digital welding interfaces that allow for parameter memory storage and real-time adjustments cater well to TIG stainless welding. Knowledge dissemination through workshops and certification programs led by industry authorities further enhances skill levels. Such programs emphasize practical application alongside theoretical knowledge, which can be pivotal in reducing the learning curve and improving weld quality more rapidly than through experience alone.
Trustworthiness in TIG stainless welding is cemented through consistent, high-quality output. Adherence to industry standards and guidelines, such as those set by the American Welding Society (AWS), ensures that processes are up to mark and comply with safety and quality norms. Furthermore, a trustworthy welding service ensures transparent communications with clients regarding material suitability, project timelines, and cost implications, thereby fostering long-term professional relationships and repeat business.
The journey from a novice to a proficient TIG stainless welder requires dedication, continuing education, and a robust understanding of both theoretical principles and practical nuances. By investing in quality equipment, like tungsten electrodes of varied sizes and pure argon as a shielding gas, welders set the stage for achieving more precise and effective welds. Moreover, the efficient upkeep of this equipment ensures that weld quality does not degrade over time, thus maintaining credibility and trust.
In conclusion, TIG welding on stainless steel is more than just a method; it is an art governed by science. It demands attention to detail, patience, and an evolving skill set to keep up with material and technological advancements. As industries increasingly rely on stainless steel for its strength and resistance to corrosion, mastering TIG welding not only opens doors to numerous opportunities but also establishes a benchmark for quality and expertise in the field. Such mastery ensures that the welds not only meet but exceed quality and aesthetic expectations, thereby contributing to the ongoing quest for innovation and excellence in manufacturing.