Proper storage of 7018 welding rods is critical for maintaining their effectiveness and ensuring high-quality welds. As an experienced welder, understanding the nuances of rod storage can make all the difference in project outcomes. These electrodes, categorized as low-hydrogen, are highly susceptible to moisture absorption, which can lead to hydrogen embrittlement and compromised weld integrity if not handled correctly.
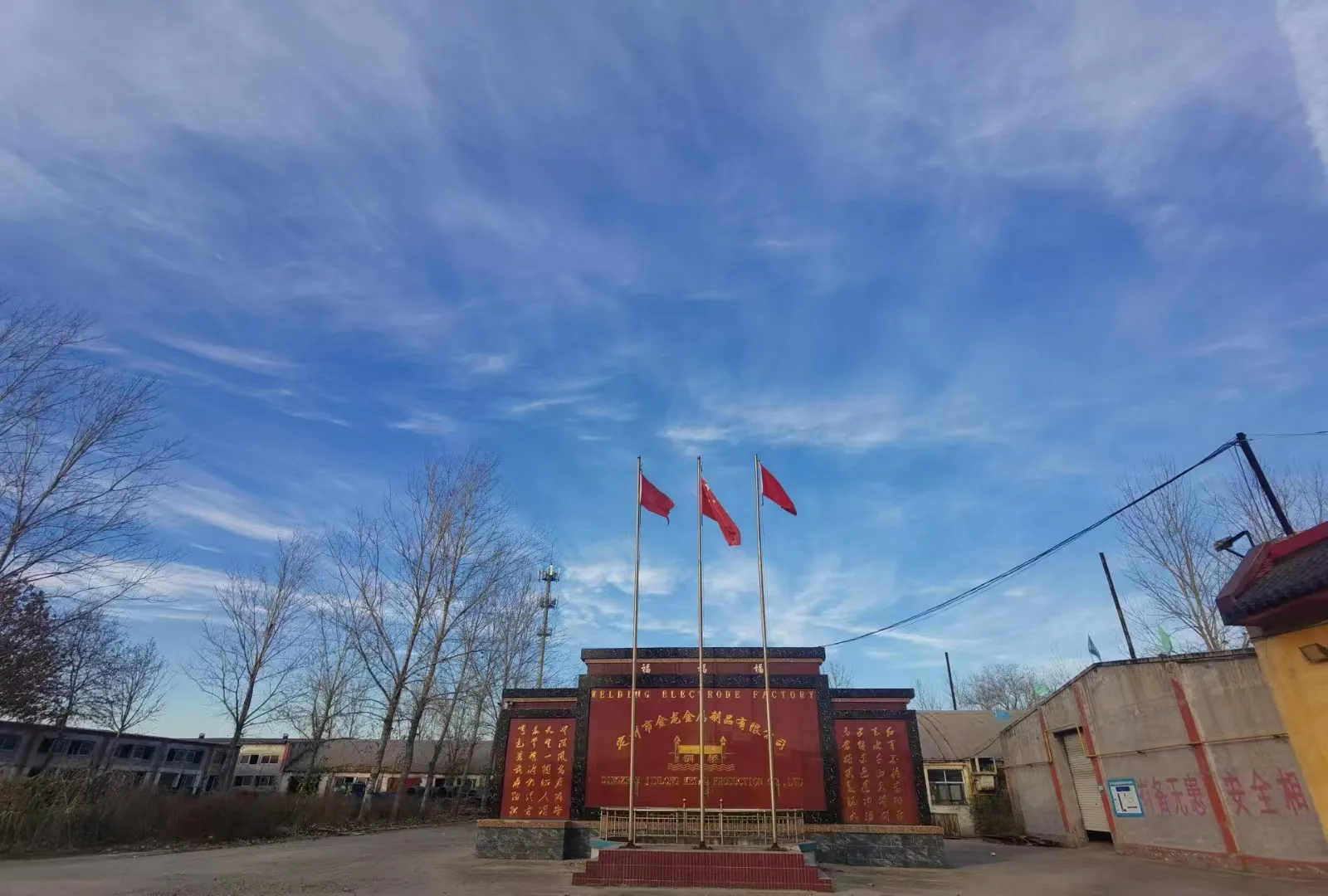
First, let's delve into the specifics of why 7018 rods require careful storage. These electrodes have a flux coating designed to minimize hydrogen content in the weld area, crucial for preventing cracks in the weld material. Exposure to moisture can increase the hydrogen levels significantly, thus defeating the purpose of using 7018 rods. Understanding this chemical aspect underscores the need for effective storage solutions.
The best practice for storing these rods starts with keeping them in their original airtight containers until you're ready to use them. Manufacturers typically ship 7018 rods in hermetically sealed cans, ensuring they remain dry until opened. Once the seal is broken, the responsibility lies with the welder to maintain the rods' integrity.

In a workshop environment, employing an electrode oven is essential. These ovens are specifically designed to maintain a consistent temperature and low humidity, which is ideal for storing 7018 rods after the original packaging is opened. The recommended temperature for storing these rods is between 250°F to 300°F (121°C to 149°C). This range prevents moisture absorption while being energy efficient. Investing in these ovens can be seen as a safeguard against potential welding defects that can arise from moisture-compromised rods.
storing 7018 welding rods
It's also worthwhile to mention that if the rods have already absorbed moisture, they can be reconditioned. This process involves baking them at a higher temperature for a specified period as recommended by the rod manufacturer. Typically, this is at 600°F (315°C) for one hour. However, not all rods can be reconditioned, and the number of times this can be done is limited, emphasizing that prevention through proper storage is the best policy.
Additionally, consider the importance of organization and labeling in your storage process. Keeping different types and diameters of rods clearly labeled and separated can prevent mix-ups and ensure that the correct rods are used for specific applications. This organized approach not only saves time but also enhances workflow efficiency and project accuracy.
Furthermore, trustworthiness in handling the storage of 7018 rods is also built upon regular assessments and adherence to manufacturer guidelines. Inspect your storage conditions and rods periodically for signs of moisture exposure, such as discoloration or a powdery residue on the rod’s surface. Consistent diligence in this regard establishes a professional standard and reinforces reliability in welding practices.
By implementing these expert storage techniques, you not only preserve the functionality of your 7018 welding rods but also safeguard the quality of your welds, enhancing the overall success of your projects. This strategic approach to rod storage—a blend of knowledge, expertise, and an unwavering commitment to best practices—will ensure long-term project success and establish your reputation as a skilled and trustworthy welding professional. Taking these steps demonstrates an authoritative command over materials performance, ultimately leading to superior outcomes and satisfied clients.