Stick welding, or shielded metal arc welding (SMAW) of cast iron is a uniquely challenging yet rewarding task, demanding a deep understanding of metallurgy and proficiency in technique. Cast iron's high carbon content, which generally ranges from 2 to 4 percent, makes it prone to cracking and requires special attention during the welding process.
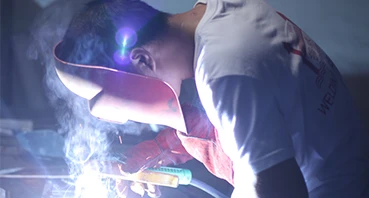
One crucial component of stick welding cast iron is electrode selection. Nickel-based electrodes, such as AWS EniFe-CI or V2 Welding Rods, are highly recommended due to their ability to handle cast iron's expansion and contraction during heating and cooling. Nickel acts as a buffer that absorbs stress, reducing the possibility of cracks. Moreover, nickel electrodes are ideal for cold welding, where you can weld in short bursts, allowing the material to cool between passes, minimizing heat buildup and stress.
Pre-heating is another critical step in stick welding cast iron, which mitigates the risk of thermal shock. The temperature range for pre-heating cast iron is generally between 500°F and 1200°F, with factors such as the cast iron's thickness and composition influencing the exact temperature. Pre-heating ensures that the welded area and its vicinity expand uniformly, reducing tensile stress during cooling. For hefty castings, slow and uniform pre-heating is essential to prevent crack initiation.
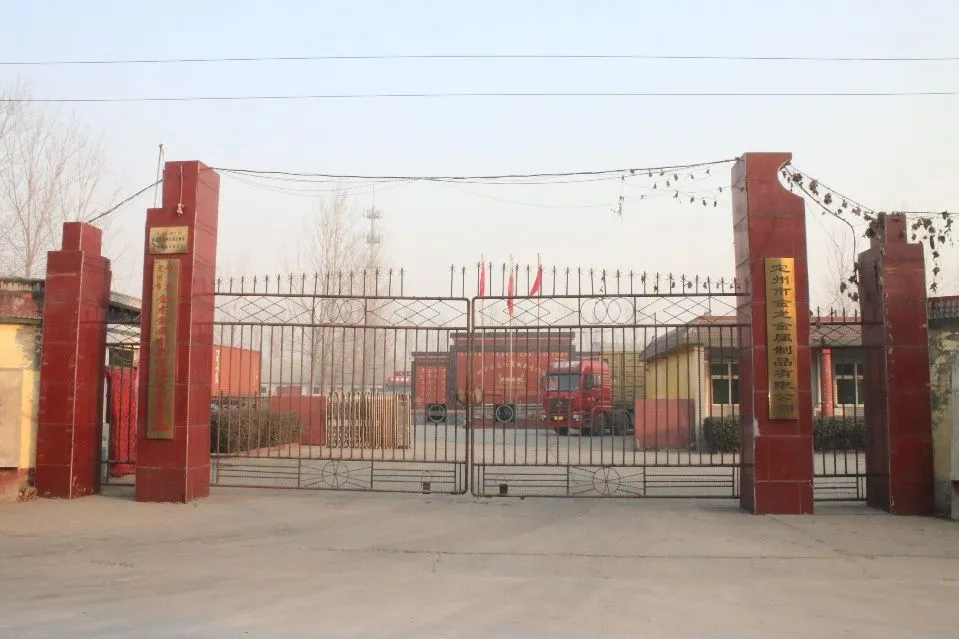
Successful stick welding also necessitates controlled cooling. Post-weld treatments such as slow cooling can be achieved by wrapping the cast iron in an insulating blanket. This process decreases the temperature gradient across the welded workpiece, ensuring it cools uniformly, which is vital in preventing cracking.
Experience underscores the importance of joint preparation. Clean and properly beveled joint surfaces improve fusion and penetration. Arc length should be kept short to stabilize the arc, maintaining greater control over heat input and reducing spatter. Standard practice recommends a weaving technique to ensure even distribution of heat and filler material across the joint.
stick welding cast iron
Equally important is constant observation of the molten pool's color and behavior, which offers feedback on the weld quality. Proper observation helps in determining whether adjustments in travel speed or current settings are necessary to maintain an optimal welding environment.
Expertise in metallurgy imparts an understanding of the different types of cast iron, such as gray, ductile, and malleable iron, and influences how each should be approached in welding. Gray iron, identified by its graphitic microstructure, is the most commonly welded type, yet it demands careful consideration regarding its brittleness and reactivity. Ductile iron, with its spherical graphite inclusions, offers greater flexibility but requires awareness of its mechanical properties under heat stress. Understanding these differences lends authority to the welding process, allowing the welder to tailor techniques accordingly.
Authority in stick welding cast iron is also demonstrated through compliance with industry standards, such as those from the American Welding Society (AWS) and ISO guidelines. Adherence to these standards ensures the welded part meets quality, safety, and performance benchmarks, further cementing credibility and trustworthiness.
To conclude, stick welding cast iron is an endeavor that combines art and science, requiring diligent procedure and a firm grasp of the material's properties. Whether repairing a broken engine block or constructing a new cast component, success hinges on informed choices and meticulous execution. The interplay of experience, technical expertise, authority, and adherence to trusted practices culminates in a robust and crack-free weld that meets the highest quality standards.