Selecting the right stainless welding electrode is crucial for achieving high-quality welds, especially in industries where strength and corrosion resistance are paramount. With a plethora of electrodes available in the market, choosing the right one can be a complex task. However, understanding their distinct characteristics and applications can greatly aid in making an informed decision.
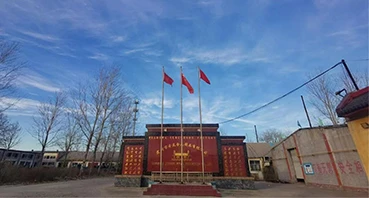
Stainless welding electrodes are designed to fuse metals while preserving essential alloy components that increase the durability and strength of the joint. These electrodes come in several grades and types, each suitable for different stainless steel categories such as austenitic, ferritic, martensitic, duplex, and precipitation-hardening stainless steels.
Austenitic stainless steels, typically represented by the 304 or 316 series, are among the most commonly welded stainless steels. If you're using an austenitic stainless steel,
look for electrodes designated with a 308, 316, or similar identifier. These electrodes contain the right balance of chromium and nickel to maintain corrosion resistance and ensure that the weld matches the strength and appearance of the base metal.
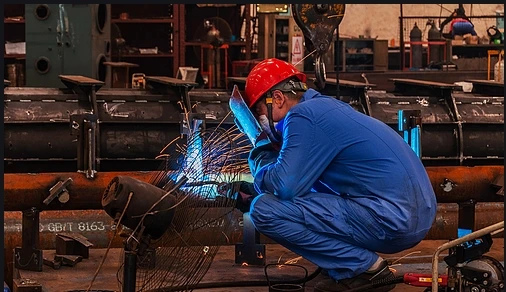
For ferritic stainless steels, which are magnetic and generally less prone to thermal expansion, 430 series electrodes are the optimal choice. These electrodes produce welds with good resistance to stress corrosion cracking and are often used in automotive applications and decorative trims.
When dealing with martensitic stainless steels, used in applications requiring high hardness and moderate corrosion resistance, selecting the appropriate electrode is crucial to prevent issues like cracking. 410 series electrodes are engineered for these types of stainless steels, producing hard yet corrosion-resistant welds suitable for applications such as turbine blades and surgical instruments.
stainless welding electrode
In scenarios where duplex or super duplex stainless steels are involved, the welding electrode must complement the balanced dual-phase structure of these materials. Electrodes like the 2209 type are specifically crafted to ensure good mechanical properties and resilience against corrosion, particularly in environments like petrochemical plants and marine applications.
The profession of welding calls for a depth of knowledge not only in material compatibility but also in the operational parameters of the welding process itself. Every application has its challenges, such as the potential for distortion, cracking, or reduced corrosion resistance. Therefore, the utilization of backing gases like argon or a mixture of argon and hydrogen can be advantageous, providing a shielding effect that minimizes oxidation and preserves chromium content at the weld surface.
Pre-weld preparation and post-weld cleaning are equally vital to the success of welding stainless steel. Remove any surface contaminants and oxidations such as oil, rust, or scale from the workpieces to ensure optimal metallurgical bonding. Post-welding, the application of passivation processes can help restore the chromium-rich oxide layer essential for corrosion resistance, further extending the longevity of the welded structure.
In conclusion, understanding the particularities of stainless welding electrodes will significantly enhance the quality and resilience of welds in different industrial environments. Complex as it may seem, this expertise in electrode selection and welding process optimization contributes not only to product innovation but also establishes a benchmark for quality in the fabrication industry. Such informed decisions and practices develop reliability, confirming the welder's authoritative command over the stainless steel welding processes. The more knowledgeable and precise your approach is, the more your welding craftsmanship will reflect trustworthiness and expertise, distinguishing your work in a competitive field.