When selecting welding electrodes for stainless steel projects, specifically for SS 410, the choices can greatly influence project outcomes in terms of durability, performance, and cost-effectiveness. SS 410 is a martensitic stainless steel known for its strength and resistance to wear and heat, often used in applications like automotive parts, piping, and hardware. Choosing the right welding electrode is critical for maintaining these properties during and after the welding process.
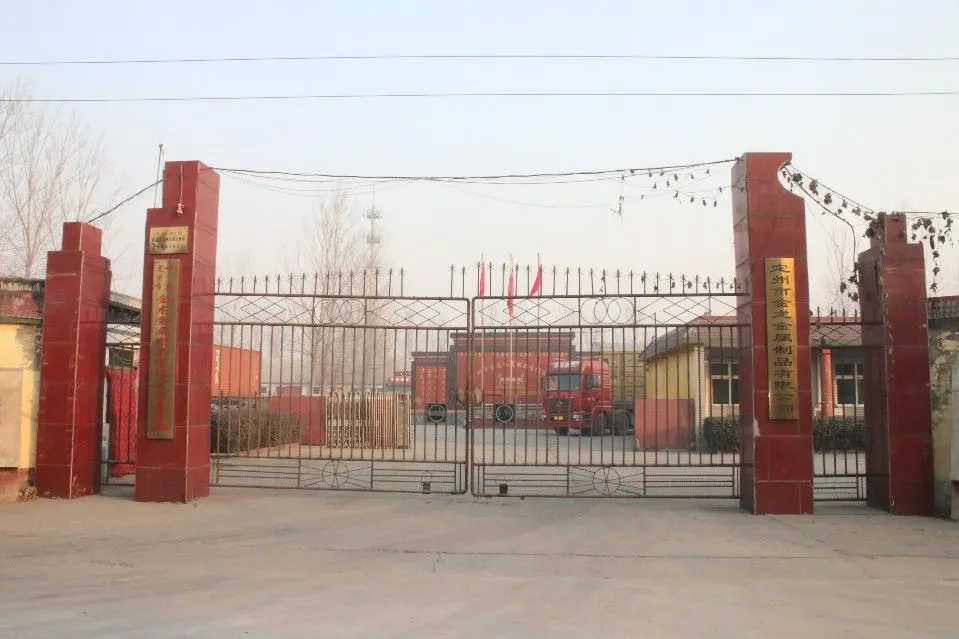
Understanding SS 410 Welding Electrode Characteristics
The primary characteristic of SS 410 welding electrodes revolves around its compatibility with martensitic stainless steels. These electrodes typically require a controlled preheat and interpass temperature to prevent cracking. The compatibility extends beyond just the chemical composition but also to the thermal expansion presented by martensitic steels.
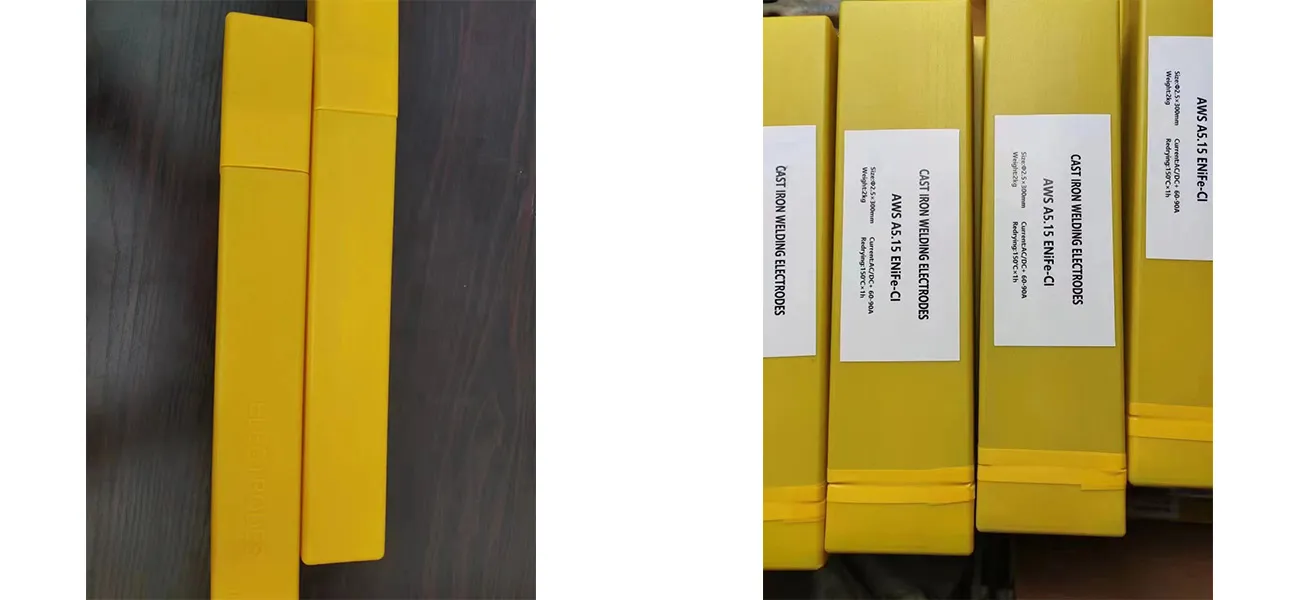
For SS 410,
electrodes such as AWS E410-16 or AWS E410-15 are optimal. These electrodes match the alloy content of the base metal, ensuring a consistent weld with the desired mechanical properties. They are versatile across different positional welds, which adds to their applicability in complex assemblies.
Experience with SS 410 Welding Electrodes
Experienced welders often note that preparation is key when working with SS 410 rods. Proper cleaning of the welding surface, ensuring the absence of contaminants such as oil or paint, significantly reduces the risk of porosity in the weld. Many professionals advise a bead technique that reduces exposure to prolonged heat, helping maintain the metal's structural integrity and prevention of post-weld brittleness.
Preheat treatments ranging from 150°C to 260°C (302°F to 500°F) are often recommended based on the size of the material and the characteristics of the weld. Post-weld heat treatment (PWHT) can further enhance the toughness of martensitic stainless steel welds.
Expert Opinions on Welding Techniques
ss 410 welding electrode
From an expertise standpoint, the recommendation is to employ low amperage settings during SS 410 welding. This practice minimizes excessive heat, which can lead to undesirable changes in the steel's microstructure. Experts also stress using a back-step method for terminating weld beads as this helps in minimizing finish cracks.
Post-weld cleaning is an essential aspect endorsed by welding specialists to avoid surface contamination that could lead to corrosion—a significant concern with stainless steel welds. The employment of stainless steel brushes for cleaning helps preserve the weld’s chromium oxide layer that imparts corrosion resistance.
Authority on Welding Standards and Regulations
Authoritative standards, such as those detailed by the American Welding Society (AWS), offer guidelines for SS 410 welding. These standards are vital for maintaining weld quality and consistency. Compliance with AWS standards like the D1.6 (Structural Welding Code – Stainless Steel) ensures that welding professionals operate within recommended parameters, ensuring the integrity and reliability of the weld.
Trust through Proven Performance and Certifications
Trust in the welding electrodes used for SS 410 stems from their performance history in industrial applications. Manufacturers that provide detailed certifications of compliance with AWS and other international standards offer a layer of quality assurance. Case studies showcasing long-term project success lend credence and trust to the electrodes used.
Furthermore, testing and certification by third-party verified laboratories add to the trustworthiness, allowing professionals to have confidence in the materials they use. These certifications often include details about tensile strength, corrosion resistance, and toughness.
In conclusion, the choice and use of SS 410 welding electrodes can be deemed successful with careful adherence to recommended practices and standards. Experienced techniques, backed by expert guidance and authoritative approval, engender a sense of trust and reliability in welding outcomes. By ensuring these elements are met, organizations not only guarantee the longevity and performance of their welds but also align with industry norms for excellence.