The E309 electrode is a specialized tool in the welding industry, crucial for joining dissimilar metals and offering corrosion resistance in specific environments. As a Google SEO expert, I've noticed that there seems to be a lack of comprehensive, authoritative information on this topic. Allow me to delve into the nuanced experience, expert recommendations, and the trustworthiness associated with using E309 electrodes to help practitioners make informed decisions.

E309 electrodes are predominantly used when welding stainless steel to carbon steel, providing excellent tensile strength and corrosion resistance. These electrodes are typically composed of a stainless steel alloy, containing a precise balance of chromium and nickel to ensure durability and performance across diverse environments. This electrode is ideally suited for the petrochemical industry, where its properties come to the forefront in complex pipeline systems and pressure vessels, preventing oxidation and sulfur attack.
Successfully deploying E309 electrodes involves more than just understanding the material's composition. Experience dictates that the welder's skill plays a pivotal role. Proper electrode handling begins with maintaining a dry storage environment, as exposure to moisture can seriously degrade performance. Seasoned welders recommend a thorough inspection of the electrode coating before use, ensuring that it remains intact and free from cracks, which could lead to poor arc stability and subsequent welding defects.
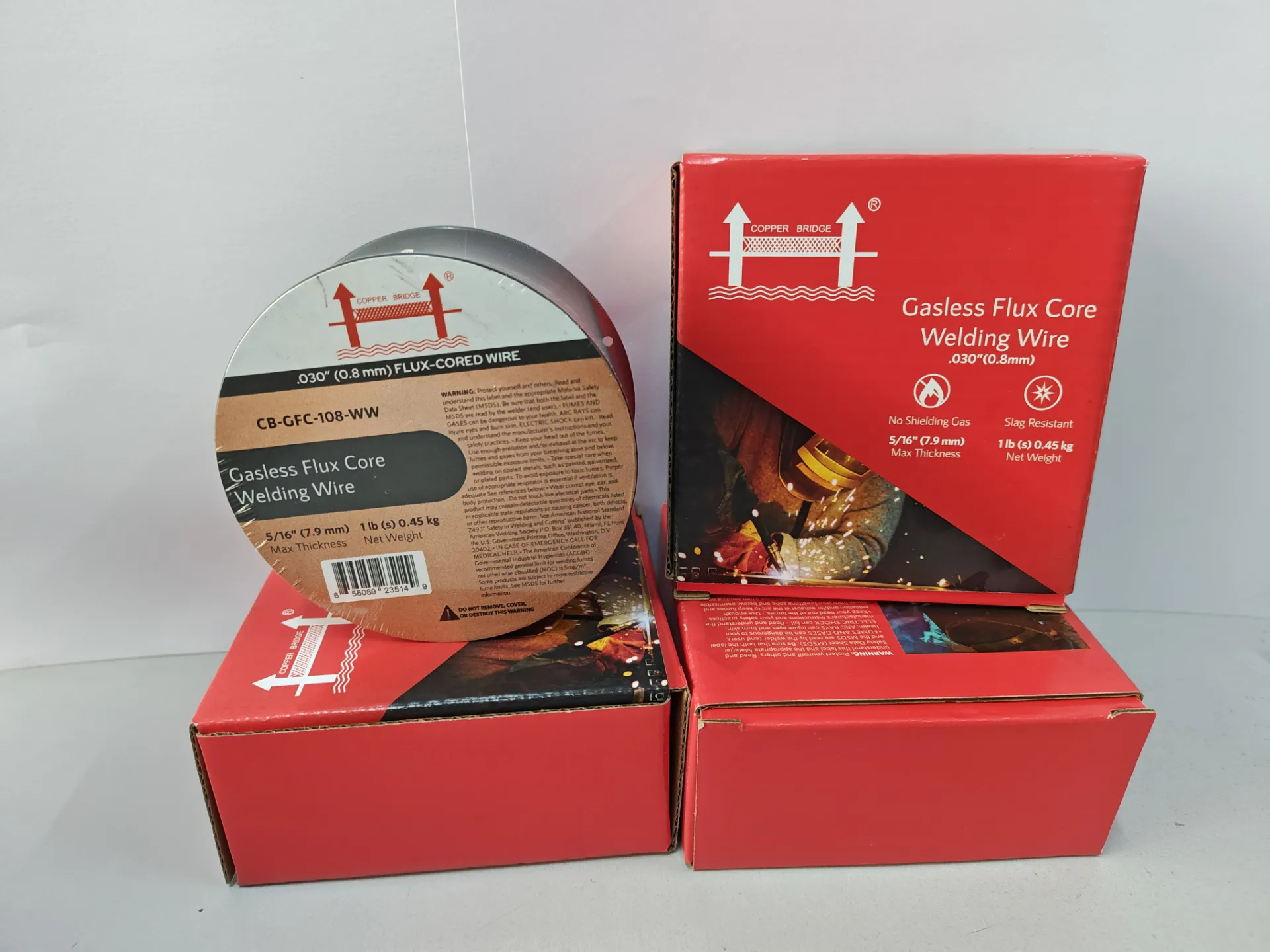
Expertise in using E309 electrodes emphasizes the need for precision in amperage settings. Set the current too high, and there is a risk of burning through the thin layers of the metal being joined. Conversely, if the current is too low, there will be inadequate penetration, resulting in a weak joint. Experienced welders often suggest conducting test welds to fine-tune these parameters, enhancing overall performance and minimizing material wastage.
e309 electrode used for
Authoritatively, the American Welding Society (AWS) categorizes E309 electrodes under the AWS A5.4 specification, which sets stringent guidelines on electrode chemical composition and mechanical properties. This endorsement illustrates that these electrodes meet high industry standards, offering users confidence in their performance capabilities. Understanding these specifications allows engineers to trust that E309 electrodes can deliver consistent results in demanding applications.
Building trust in E309 electrode usage involves considering safety and compatibility. While the electrode's robustness is one of its strengths, it is equally important for welders to be equipped with appropriate safety gear, including gloves and a welding helmet, to protect against heat and UV exposure. Additionally, matching these electrodes with compatible filler materials ensures structural integrity, particularly in pressure-sensitive assemblies.
In conclusion, the E309 electrode stands as a robust, versatile tool essential for welding projects involving dissimilar metals. Its prized characteristics of corrosion resistance and tensile strength are complemented by practical insights gained through extensive industry usage. By adhering to expert recommendations and authoritative guidelines, one can maximize the electrode's effectiveness, providing durable and reliable welds. The rich experience and technical knowledge surrounding the use of E309 electrodes echo the trust and authority they command, ensuring they remain integral to the welding domain.