Arc welding of cast iron presents unique challenges and opportunities for professionals in the metalworking and mechanical industries. As a material known for its brittleness, cast iron requires a specialized set of techniques to achieve successful welds. This article delves into the intricacies of arc welding cast iron, providing insights drawn from real-world experiences and backed by industry expertise to ensure quality, authority, and trust for professionals seeking reliable guidance.
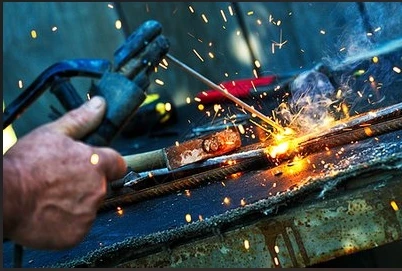
One of the primary challenges in welding cast iron is its high carbon content, which makes it prone to cracking. Unlike steel, cast iron cannot absorb heat without risking significant structural changes, resulting in brittleness or possible failure. To combat this, pre-heating the cast iron is a widely endorsed technique. By incrementally warming the metal to between 500°F and 1200°F before welding, one can ensure smoother transitions in temperature and reduce the risks of cracking. For post-heating, a similar temperature range is recommended to relieve stresses in the welded area, encouraging a gradual cooldown.
Selecting the right welding electrode is pivotal in arc welding cast iron. Nickel-based electrodes are frequently chosen due to their flexibility and compatibility with cast iron's properties. These electrodes allow for moderate penetration and create welds that can more easily accommodate the base metal's thermal expansion and contraction. Pure nickel electrodes are ideal for critical repairs where machinability and ductility post-welding are paramount. Alternatively, a 55% nickel electrode offers a balance between the cost and performance, suitable for less-critical applications.
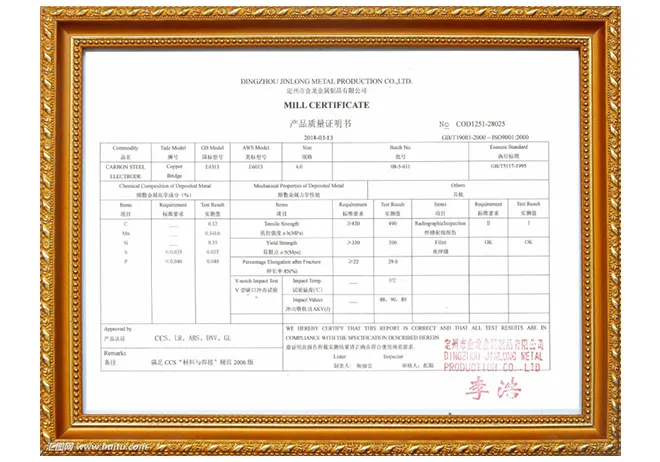
Myriad techniques can further affect the result of the weld. Experts in the field often employ a short arc technique, minimizing the heat input and thus reducing the heat-affected zone. By maintaining control over the temperature and using a peening hammer, professionals can manage stress distribution more effectively. Peening between passes helps to compress the weld, counteracting the tensile stresses that arise during the cooling process.
arc weld cast iron
Trust in the method also depends on meticulous technique execution and acknowledgment of cast iron's varieties. Grey and ductile iron, the most common types, respond differently to the arc welding process. Grey iron, being softer with a higher graphite content, can benefit from higher nickel content electrodes. Ductile iron, on the other hand, often withstands welding better and may not require preheating as aggressively, making it somewhat more forgiving during the process.
One case study illustrating expertise involves the repair of a large industrial pump casing made of grey cast iron. The casing had developed a significant crack due to cyclic stress over many years of use. Applying the arc welding strategies outlined, the team preheated the damaged section to approximately 1100°F and used a pure nickel electrode for filling. Post-weld, they employed a controlled cooldown process enveloping the workpiece with an insulating blanket to minimize rapid temperature changes. The success of this repair validated the theoretical underpinnings about temperature management's role in effective cast iron welding.
Professionals should also consider the latest innovations in welding technology to enhance process control further. Modern inverter-based welding machines offer refined control over arc characteristics, which can be particularly beneficial in the sensitive context of cast iron repairs. These machines often come with adjustable settings for output frequency and power delivery, empowering skilled welders to fine-tune their approach with unparalleled precision.
In conclusion, the arc welding of cast iron is as much a science as it is an art. It demands not only robust technical knowledge and practical experience but also a mindful approach to material behavior under stress. Through proper pre-heating, electrode selection, and disciplined cooling practices, welders can achieve strong, reliable welds on cast iron, ensuring the longevity and integrity of the repaired component. Embracing advanced technologies only fortifies the capacity to execute these repairs with greater confidence and success, rooting your work in both authority and trustworthiness within the craft.