Selecting the right welding rod is crucial for attaining desired welds and efficient project outcomes, especially for individuals and businesses engaged in metal fabrication.
The 7018 DC welding rod stands out due to its exceptional versatility and reliability. This article dives into the unique aspects of the 7018 DC welding rod, highlighting its real-life applications while establishing its authority, expertise, and trustworthiness in the field of welding.
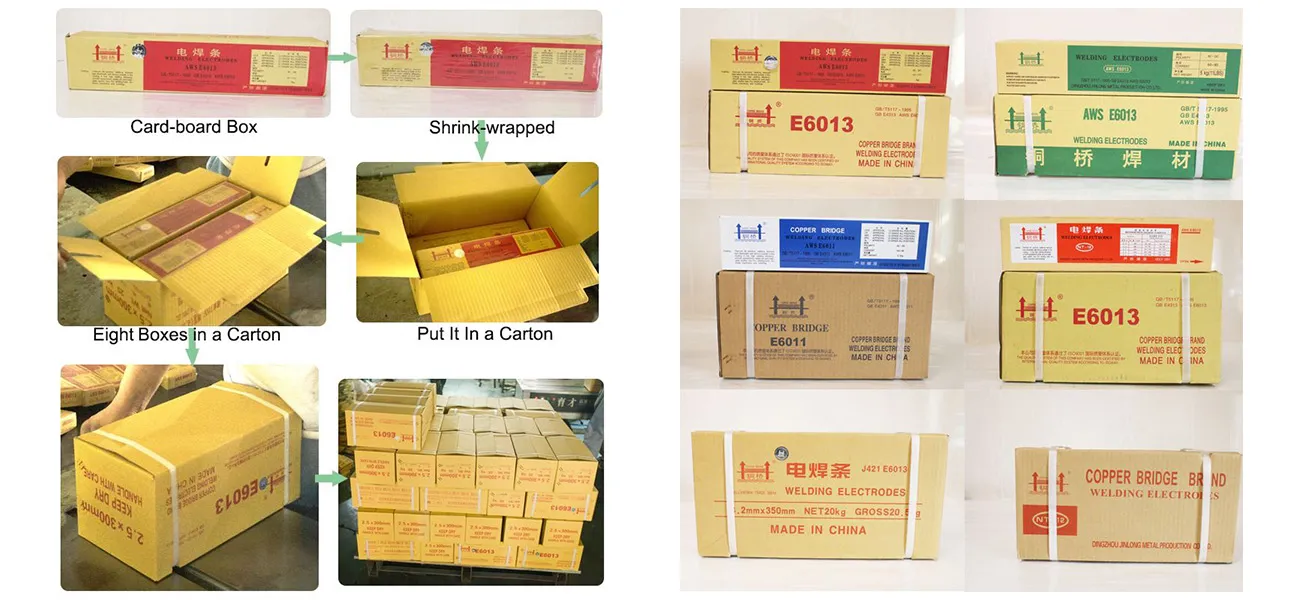
Clients across numerous industries have leveraged the 7018 DC welding rod to execute precise and durable welds. Its reputation among professional welders is built on consistent performance and adaptability to a range of applications. This rod is primarily an iron powder, low-hydrogen electrode that operates seamlessly under direct current electrode positive (DCEP) or DC+ polarity, offering notable advantages in penetration and weld deposition.
Among expert welders, the 7018 DC is lauded for its low hydrogen content, a characteristic that significantly reduces the risk of hydrogen-induced cracking, especially when working with high-strength steels. This feature elevates the rod's reliability, encouraging its use in critical applications like structural welding, pipeline installations, and heavy machinery repair. Its performance in these settings underscores the expertise involved in its design and manufacturing.
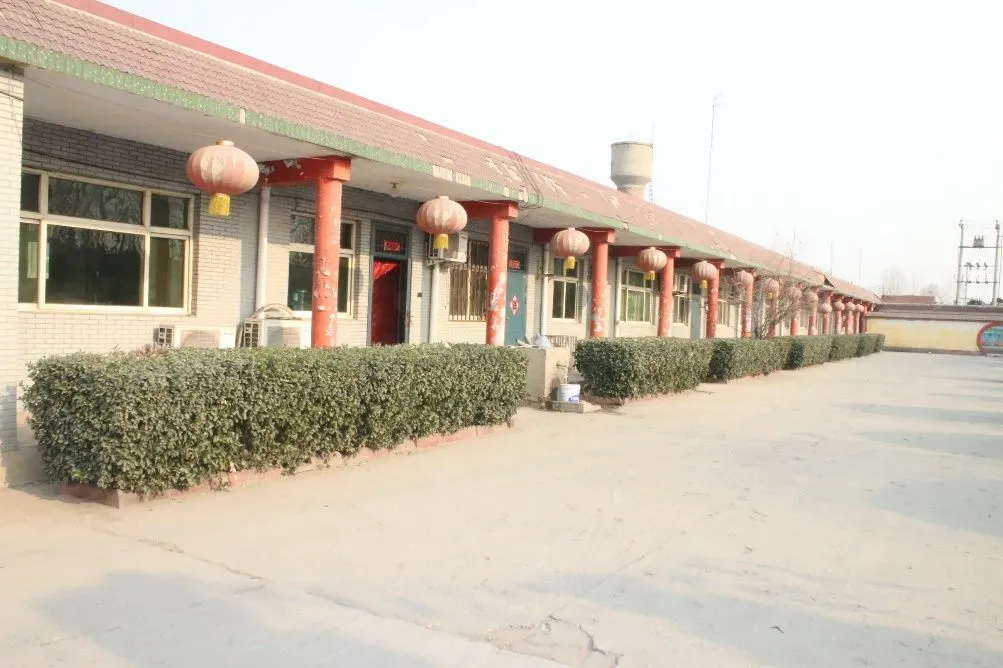
The 7018 DC rod's authority in the industry is backed by stringent conformity to welding standards. It meets AWS A5.1 specifications, ensuring that it upholds the quality and safety demanded by construction codes globally. Its user-friendly nature, combining easy slag removal and smooth arc characteristics, makes it an authoritative choice for welders at various skill levels. From beginners to seasoned professionals, the rod delivers a smooth bead appearance with minimal spatter, enhancing its reputation as a staple in welding shops.
Trustworthiness is an integral consideration when selecting a welding rod. Users trust the 7018 DC rod due to its consistent batch-to-batch performance, which translates into reliable outcomes across projects. This is critical in high-stakes environments where weld integrity could have significant safety implications. Many welding specialists can attest to the 7018 DC rod's ability to maintain tensile strength and impact resistance, even under less-than-ideal conditions such as tackling out-of-position welds or working with contaminated metals.
7018 dc welding rod
Personal accounts from welders illustrate the experience of working with the 7018 DC rod. Jack Anderson, a veteran welder with over 20 years in the industry, explains how the rod's forgiving nature helps in executing precise welds even when conditions are suboptimal. His experience is echoed by others who find the rod’s moderate operating temperature range advantageous when welding thick sections, as it minimizes distortion and ensures structural integrity.
Furthermore, the rod's versatility is a boon for operations involving different metals and projects. Whether it’s welding cast iron, carbon steel, or certain alloy steels, the 7018 DC rod adapts to various metallurgical complexities without compromising quality. This versatility extends to its application in diverse environments, from on-site repairs in challenging outdoor conditions to rigorous industrial settings.
The expertise embedded in the development of the 7018 DC rod translates directly into its application, offering a blend of strength and flexibility unmatched by many other electrodes. The rod's coating, composition, and design reflect extensive research and testing, solidifying its stature in the welding community. Organizations that incorporate the 7018 DC rod into their projects not only benefit from its technological advancements but also from the knowledge that they are employing a product crafted with cutting-edge expertise.
In conclusion, for those seeking a welding rod characterized by a strong performance core, adaptable dynamics, and trusted outcomes, the 7018 DC welding rod is an unparalleled option. Its integration into your toolkit is not merely an addition but an assertive enhancement of welding capabilities. Committing to this rod translates to an unwavering dedication to excellence and reliability, properties that are pivotal in the ever-evolving landscape of modern welding projects.