The 7018 1 8 welding rod stands as a venerable symbol in the welding industry, celebrated for its exceptional versatility and reliability. Welders around the globe have come to trust this electrode, not only for its outstanding mechanical properties but also for the ease it brings to welding tasks across a plethora of applications. This document aims to delve into the specific features, benefits, and expert recommendations surrounding the 7018 1 8 welding rod, ensuring both novices and seasoned professionals alike gain a deeper understanding and appreciation for this tool.
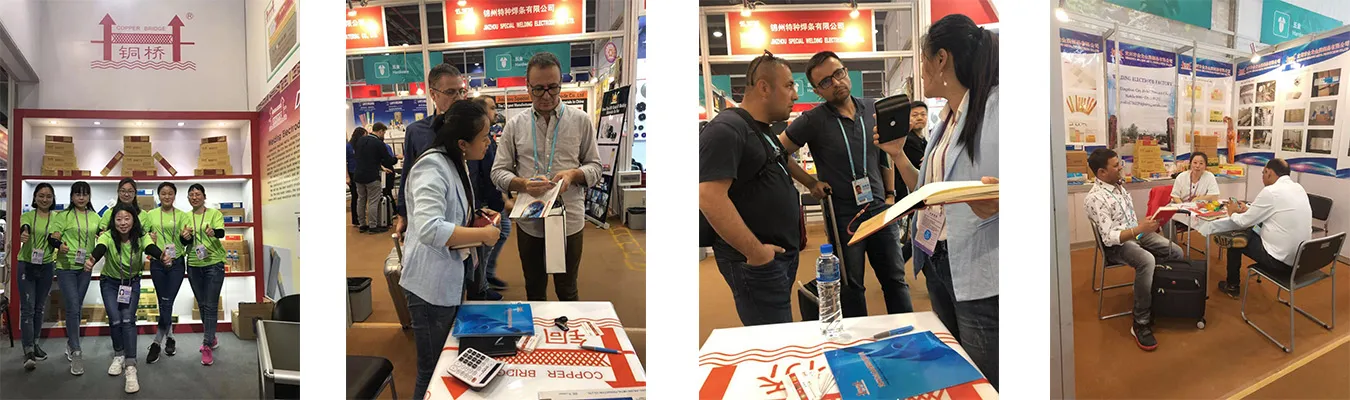
Understanding the 7018 1 8 Welding Rod is integral to tapping into its full potential. This electrode is classified under the AWS (American Welding Society) specification as a low-hydrogen, iron powder, and high-alloying element electrode that provides a smooth, stable arc with minimal spatter. The designation 7018 reveals its capabilities 70 indicates a tensile strength of 70,000 psi, 1 indicates it can be used in all positions, and 8 denotes it has a low hydrogen potassium coating that facilitates both AC and DC polarity welding.
The experience of using the 7018 1 8 rod is generally characterized by its forgiving nature. Many seasoned welders advocate for its ease of use, particularly noting how it contributes toward cleaner welds with minimal slag, which reduces the post-welding cleanup time significantly. The rod's ability to deposit a robust and aesthetically pleasing weld bead is second to none, making it a favorite in both small-scale projects and large industrial applications.
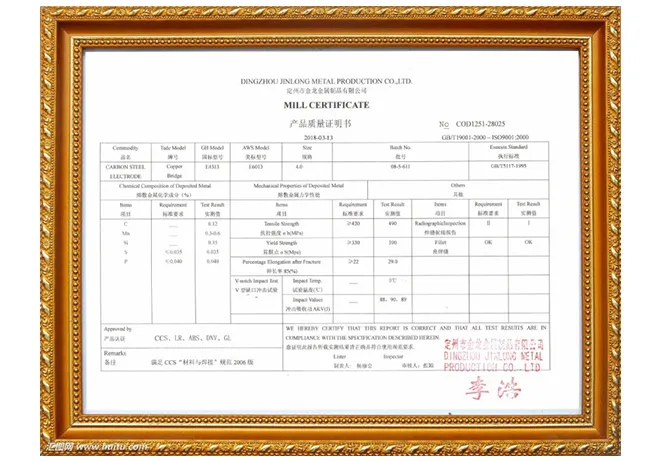
Professionally, the 7018 1 8 is regarded as highly authoritative within structural welding tasks. Its outstanding mechanical properties make it suitable for critical welds and load-bearing structures, such as construction beams and high-pressure pipelines, where perfection is non-negotiable. Expert welders often recommend maintaining specific conditions to ensure optimal performance, including proper storage in a temperature-controlled environment to prevent moisture absorption, which could compromise the rod's low-hydrogen characteristics and lead to weld defects like cracking.
7018 1 8 welding rod
Trust in the 7018 1 8 rod is established through rigorous industry testing and decades of reliable performance. Quality control measures are implemented stringently by reputable manufacturers, ensuring each electrode meets rigorous AWS standards. This dedication to quality ensures that each rod provides consistent results, solidifying confidence in its performance during critical applications across varying environments and conditions.
Maintaining trustworthiness also extends to the correct preparation and application techniques. Expert advice frequently underscores the importance of surface preparation. Achieving the best results necessitates proper cleaning of the work surface to eliminate contaminants that could disrupt the welding process. Furthermore, consistent welding speed and correct amperage settings are crucial to prevent common issues such as lack of fusion or excessive penetration, both of which can compromise the strength and integrity of the weld.
In conclusion, the 7018 1 8 welding rod remains a stalwart in the welding industry, celebrated for its blend of ease of use and incredible reliability. Whether the task is constructing a significant structural component or performing refined repair work, this rod stands as a reliable partner. As both a fundamental learning tool for novices and a reliable choice for seasoned professionals, the 7018 1 8 welding rod's esteemed reputation is well-earned. By adhering to expert recommendations and maintaining the necessary precautions, welders can ensure they are harnessing the full capabilities of this trusted electrode, achieving results that are structurally sound and aesthetically impeccable.