Welding cast iron with 309 stainless steel electrodes offers a unique set of challenges and benefits. The nuances of this process demand an experienced hand, authoritative insight, and a thorough understanding of metallurgy and welding techniques. This article delves into the intricacies of using 309 electrodes for cast iron welding, focusing on practical experiences, expert guidance, authoritative information, and trustworthy practices to ensure successful results.
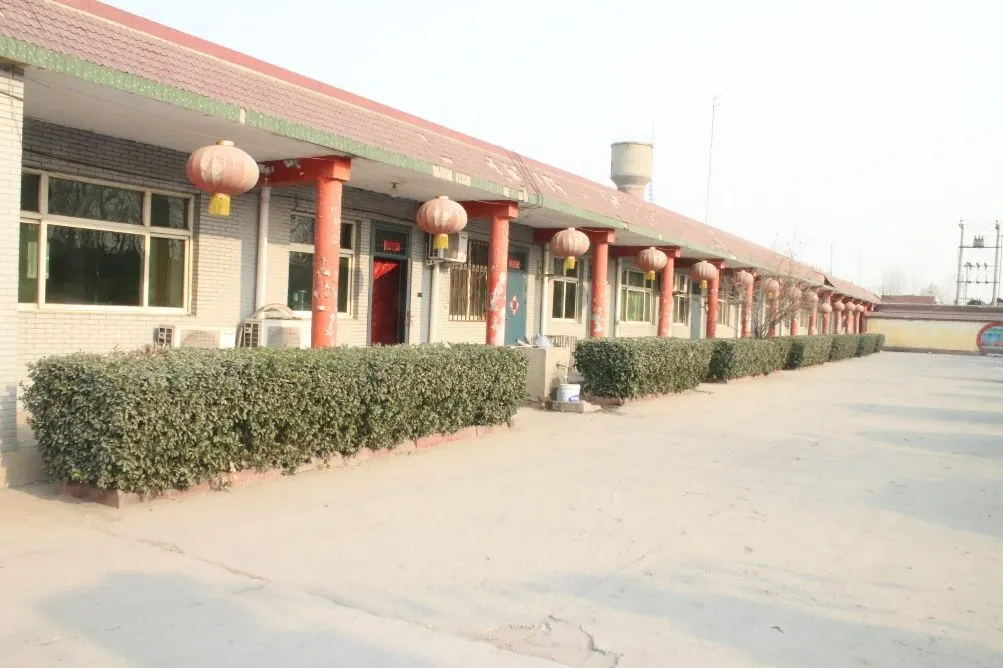
The appeal of using 309 stainless steel electrodes in welding cast iron primarily stems from their versatile properties. Unlike traditional nickel rods often used for cast iron, 309 stainless rods offer greater strength and resistance to cracking. This ability comes from the high chromium and nickel content within 309 rods, allowing welders to bridge materials with differing thermal expansion characteristics – a common issue with cast iron.
From the perspective of experience, seasoned welders report that preheating the cast iron workpiece is critical. The preheat temperature should be around 500°F (about 260°C), which minimizes thermal shock and reduces the risk of cracking. During cooling, a slow process is preferred to avoid introducing unwanted stress fractures. Investment in a heat blanket can facilitate more uniform cooling.
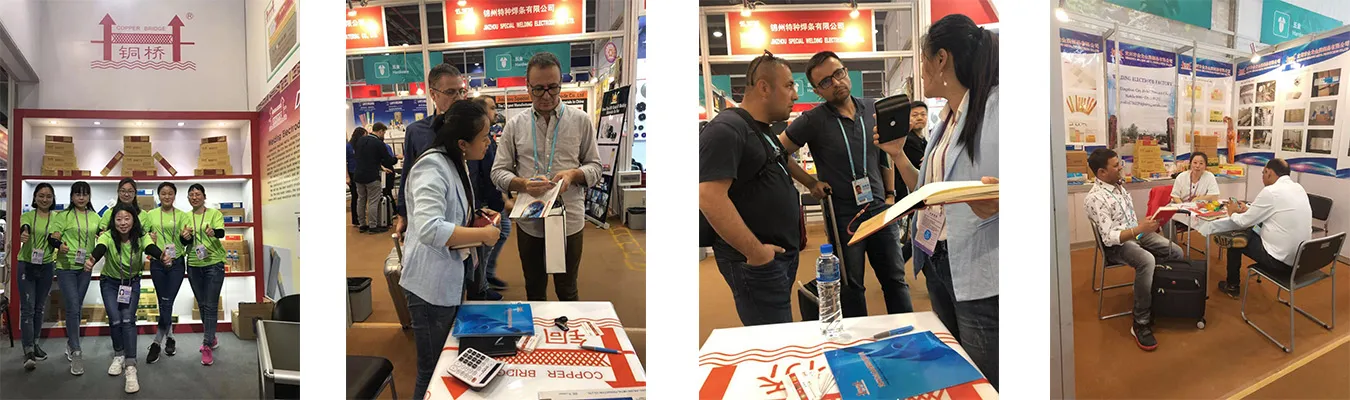
Expertise in welding also signals the importance of surface preparation. Cleansing the cast iron surface rigorously before welding can mean the difference between a strong bond and a weak joint. Oils, paints, and rust, common on cast iron surfaces, can prevent proper adhesion if not thoroughly removed. Use a wire brush or a grinder to prepare the surface effectively.
The choice of electrode diameter is another consideration for professionals. For cast iron parts of varying thickness, starting with a smaller diameter rod often helps in managing the heat input and prevents excessive penetration or burn-through, especially with thinner sections. Seasoned welding technicians suggest keeping a steady hand and maintaining consistent movement to ensure even heat distribution and smooth weld beads.
welding cast iron with 309
Authoritative knowledge from metallurgical studies indicates a balancing act between different phases of iron when welding with 309 electrodes. The key lies in maintaining ductility and reducing brittleness. A beneficial practice includes peening the weld while it is still hot to relieve stress and thus reducing brittleness. This technique, endorsed by successful welding practitioners, enhances durability.
Trust in the welding process also comes from practicing sound techniques consistently. Using stringer beads rather than weaving motions helps in managing heat input more effectively. Furthermore, people with deep experience in this field often recommend post-weld heat treatment, especially when welding thick cast iron parts. This additional step aids in stress relief and improves the overall integrity of the weld.
Welders should be aware that welding with 309 rods on cast iron can color the bead due to differences in metallurgical composition. While this factor might not affect the weld’s structural integrity, it may influence aesthetic applications. Discussing such variables with clients beforehand is always wise.
Lastly, a critical part of establishing authority and trustworthiness involves ongoing education and certification in welding technologies. Joining professional organizations, attending workshops, and becoming certified by industry bodies such as the American Welding Society (AWS) can equip welders with the latest techniques and innovations in welding cast iron with stainless steel electrodes, further proving their expertise and trustworthiness in this niche.
In conclusion, the practice of welding cast iron with 309 stainless steel electrodes is both art and science. It requires a blend of proven technique, continuous education, and adherence to safety standards to achieve a strong, reliable weld. Whether for industrial applications or repair jobs, understanding the materials and employing best practices can yield the high-quality results that both welders and their clients can trust.