Wet welding electrodes are the cornerstone of underwater welding, offering unique advantages that cater to specific industrial needs. These electrodes are designed to function effectively in submerged environments, providing strength and durability to constructions resting below water surfaces. For companies engaged in maritime repair and construction, understanding the specific characteristics and advantages of wet welding electrodes is paramount.
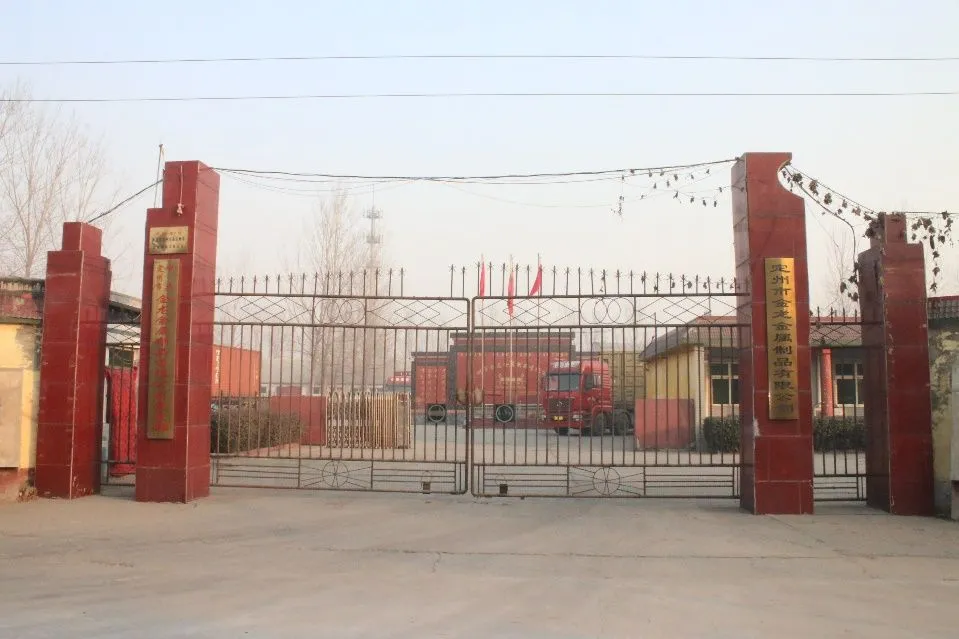
Experience with wet welding electrodes reveals several practical insights that guide their effective use. Firstly, these electrodes are coated with waterproof flux, which plays a critical role in preventing the entry of water during the welding process. This feature ensures that the arc remains stable, a crucial aspect when submerged environments impose challenges like pressure fluctuations and limited visibility. Experienced welders emphasize the importance of maintaining a consistent technique to ensure safety and quality, as the underwater environment can easily introduce variables that compromise the welding process.
Expertise in handling wet welding electrodes begins with understanding their specific types and applications. For instance, electrodes designed for ferrous metals differ from those intended for non-ferrous applications. This differentiation is imperative as it directly influences the strength and corrosion resistance of the weld. Professionals with extensive expertise often advocate for the use of electrodes that align with the metal's composition, ensuring optimal bonding and longevity of the weld. Additionally, the choice of electrode affects the speed and efficiency of the welding process, which are critical metrics in cost-time analysis for maritime projects.
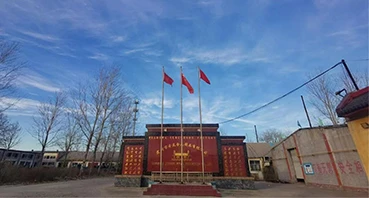
wet welding electrodes
From an authoritative standpoint, wet welding electrodes are integral to several industries, ranging from ship repair to offshore oil and gas rigs. Their unique design caters to the demanding nature of subsea environments where traditional welding techniques cannot be applied. Government regulations and industry standards emphasize the use of certified electrodes, manufactured according to stringent quality processes. Experts highlight how authoritative bodies, such as the American Bureau of Shipping (ABS) or Det Norske Veritas (DNV), set the criteria that these electrodes must meet. Credible manufacturers adhere to these standards, ensuring the end-users experience a reliable and safe underwater welding application.
Trustworthiness is an essential element in the supply and use of wet welding electrodes. The procurement process requires careful supplier vetting to ensure that the electrodes meet the specified certifications and industry standards. Trust is built on a track record of consistent performance, customer testimonials, and independent reviews. Many experienced welders rely on electrodes from reputable brands known for their rigorous quality control processes. Additionally, maintenance of the electrodes also plays a role in preserving their trustworthiness. Proper storage and handling prevent moisture ingress, which can compromise the electrode's performance even before welding begins.
In conclusion, wet welding electrodes are pivotal in the realm of underwater construction and repair, supported by a rich body of experience, expert knowledge, authoritative standards, and robust trust frameworks. Companies that integrate these electrodes within their operations gain the advantage of overcoming the unique challenges posed by underwater welding, ensuring durability and strength of underwater projects. As technological advancements propel the development of even more efficient electrodes, staying informed and adhering to best practices remains essential for anyone involved in this critical industrial sector.