For those immersed in the world of welding, understanding the nuances of different welding rods is crucial for ensuring strong, durable bonds. Among the myriad options, the 7018 3/32 welding rod stands out for its versatility and reliability. This article delves into the unique characteristics, applications, and benefits of the 7018 3/32 welding rod, offering insights grounded in professional expertise, authoritative knowledge, and real-world experience.
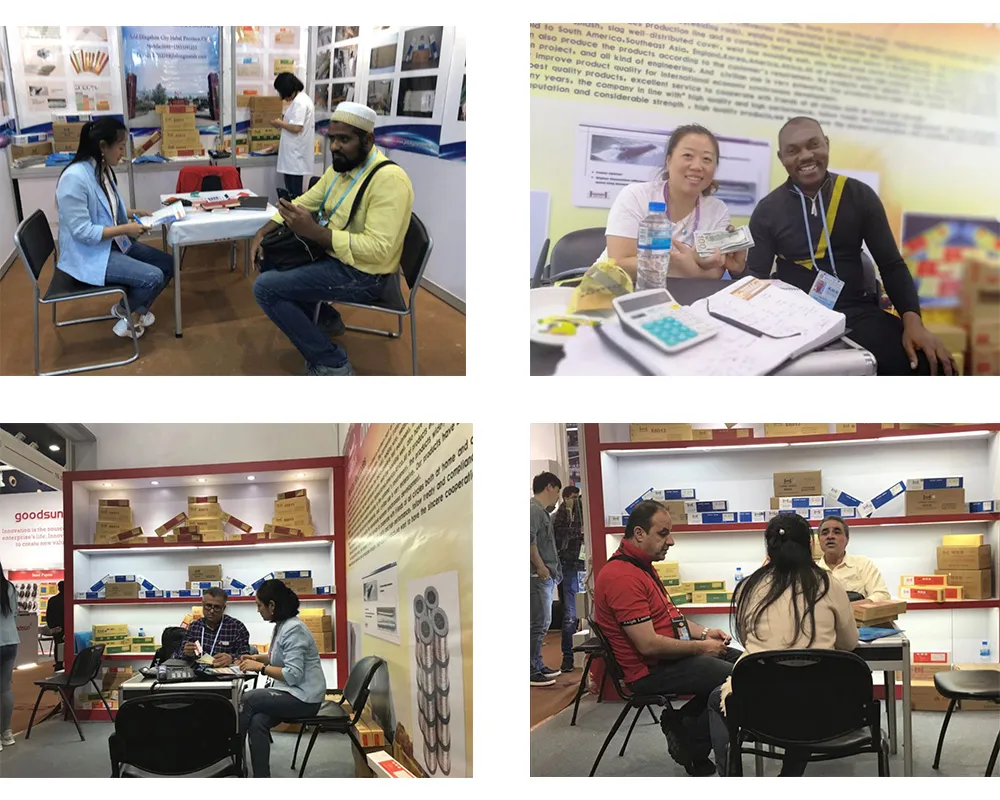
The 7018 welding rod is universally recognized for its low-hydrogen, iron powder coating, which makes it ideal for welding both carbon steel and low alloy steel. The 3/32 inch diameter variant of this electrode is particularly favored in scenarios demanding precision and control. Its smaller size allows it to be used for intricate welds, where larger electrodes may prove cumbersome. Furthermore, its aptitude for working in various positions—be it flat, horizontal, vertical, or overhead—underscores its versatility and makes it a staple for seasoned welders looking to tackle complex projects.
A significant advantage of the 7018 3/32 is its ability to produce a smooth, stable arc that minimizers spatter. This feature not only enhances the aesthetic quality of the welds but also reduces post-weld cleanup time, a critical factor in both professional and DIY settings. The resulting welds are noted for their high tensile strength, often surpassing 70,000 psi, making them exceptionally strong and resistant to cracking even under stress. Such robust welds are invaluable in industries such as construction and shipbuilding, where structural integrity is paramount.
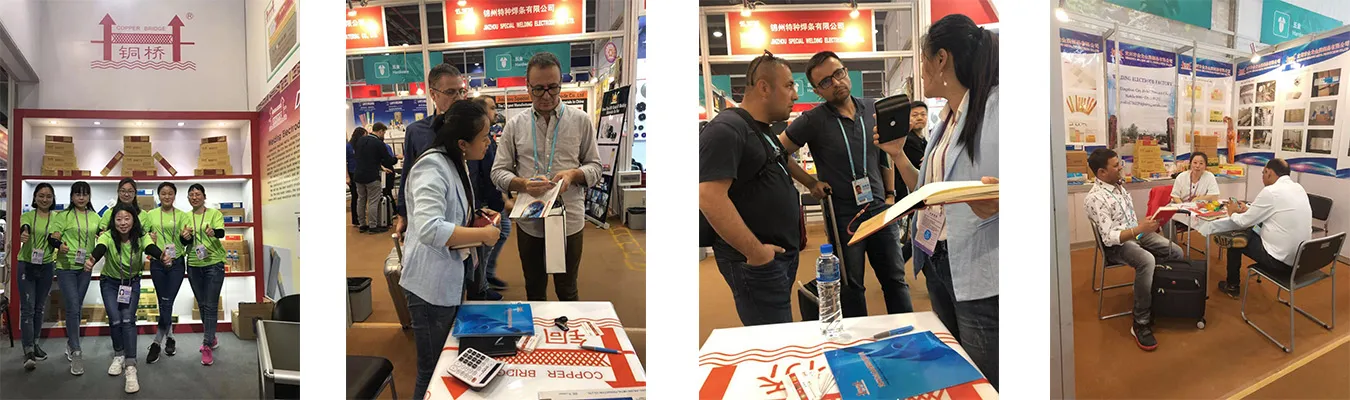
Furthermore, the 7018 3/32 welding rod is an excellent choice for projects involving thicker materials. Its low hydrogen composition plays a crucial role in preventing hydrogen-induced cracking, a common issue when welding heavy-duty materials. This quality is particularly important when working in environments subject to low temperatures, where the risk of brittleness increases. The 7018 rod's reliability in such situations is backed by both empirical evidence and authoritative endorsements from welding institutions worldwide.
welding rods 7018 3 32
Using the 7018 3/32 rod, however, requires a dry storage environment to preserve its efficacy. Moisture absorption can compromise the rod's coating, leading to potential weld defects. Professionals often employ rod ovens to maintain optimal storage conditions, thus ensuring the quality and safety of the welds. This attention to detail is a testament to the expertise and trustworthiness embedded in the use of 7018 electrodes.
The practical application of the 7018 3/32 is further complemented by expert welding techniques. Preheating thicker materials before welding can significantly improve the fusion between the rod and the metal, enhancing the overall strength of the weld. Additionally, maintaining a consistent work angle and travel speed while welding with the 7018 can result in impeccable, uniform weld beads, attesting to the experience and skill of the welder.
Choosing the right welding equipment to pair with the 7018 3/32 rod is equally essential. AC or DC welding machines with electrode positive (DCEP) are recommended to exploit the full potential of the 7018, facilitating better penetration and weld quality. This aligns with the authoritative knowledge in the field that advocates for specific equipment settings to achieve optimal results.
In conclusion, the 7018 3/32 welding rod is not just a tool but a testament to the power of precise, informed craftsmanship. Its ability to deliver strong, clean welds in various positions and conditions illustrates its indispensability in the realm of welding. Professionals and enthusiasts alike value this rod for its demonstrated effectiveness and dependability across a wide spectrum of applications—a true reflection of mastery in the art and science of welding. For projects demanding excellence and integrity, the 7018 3/32 remains unmatched, solidifying its status as a trusted partner in creating lasting, resilient bonds.