Selecting the right welding rod for iron can significantly influence the quality and durability of your welds. For both amateur welders and seasoned professionals, understanding the intricacies of welding rods designed specifically for iron is essential. With the increasing demand for robust, reliable welds across industries, the experience and expertise behind choosing and using these rods can set apart a successful project from one that fails to meet standards.
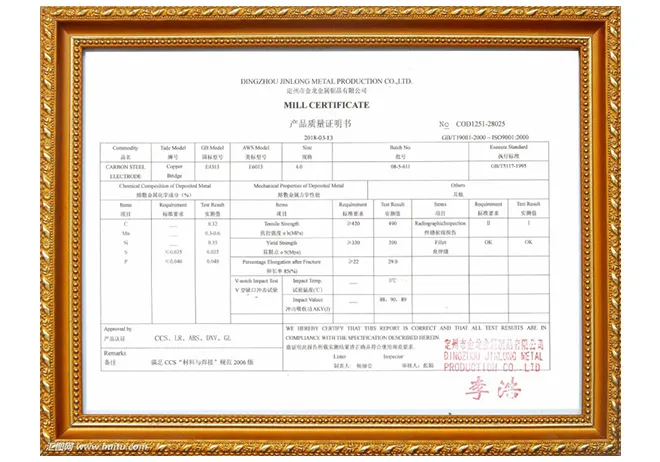
Iron welding rods are crafted with a composition that matches the base metals, thereby ensuring solid joint formation. This synergy between the rod and the metal in question reduces the risk of weak welds that could compromise structural integrity. For those who have worked extensively in this field, the first-hand experience reveals that one of the critical challenges lies in selecting the appropriate rod type from a plethora of options, each designed for specific use-cases.
Expert welders know that while price and availability are important factors, the chemical composition of the rod and the specific requirements of the project are paramount in the decision-making process. A commonly recommended choice is the E6010 rod for iron, known for its deep penetration and versatility. It excels in welding iron even when surfaces are slightly contaminated by oil or rust, making it a dependable choice for both field repairs and shop work.
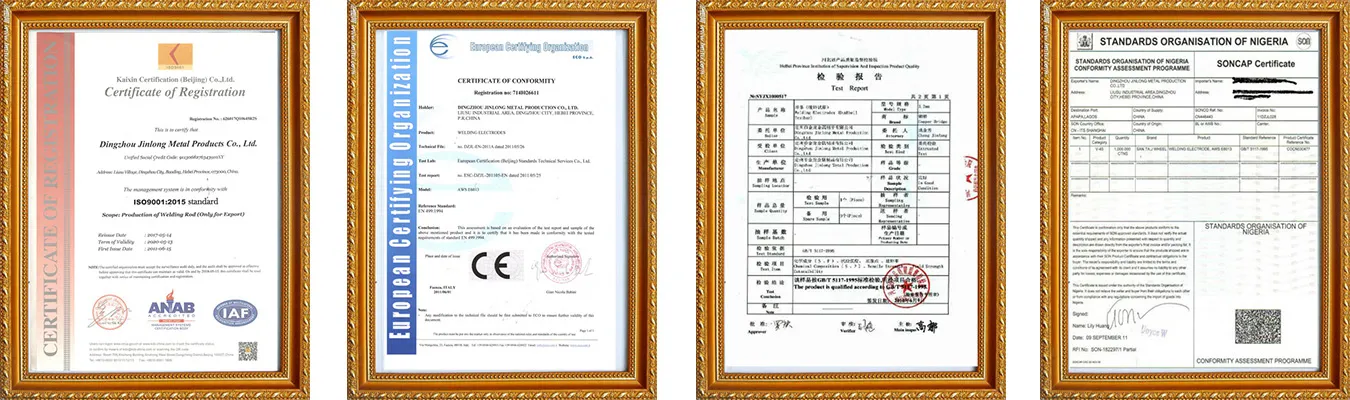
For professionals aiming to achieve new heights in their projects, understanding the unique properties each rod brings to the table is crucial. For instance, the E6011 rod offers similar benefits to the E6010 but provides more flexibility with AC welding machines. It's heralded in the industry as a go-to for instances that require swift arc strike and effortless slag removal. This rod allows users to forge ahead without the downtime associated with cleaning.
An authentic experience over the years reveals that preparation of iron surfaces before welding can drastically affect the outcome. Cleaning and beveling the metal enhances the likelihood of obtaining strong, clean welds. Experienced welders emphasize the importance of preheating, particularly for thicker iron sections, to circumvent the risks of cracking – a testament to the complexities inherent in working with iron and its alloys.
welding rod iron
Building authority in selecting the right welding rod stems from a consistent and methodical approach to experimentation and feedback. Documenting each project and learning from both failures and successes builds the depth of knowledge that sets a seasoned welder apart. This accumulated expertise is further augmented by staying updated with the latest advancements and industry norms, ensuring that iron welding practices are always aligned with the highest standards.
Trustworthiness in the realm of welding rods is achieved by using products from reputable manufacturers known for their quality and consistency. Brands that rigorously test their products and contribute to industry standards often gain the trust of the welding community. Making informed choices in tools and materials not only improves the quality of the work but also secures the welder’s reputation in the industry.
Engaging with professional networks and communities can enhance the welder’s understanding and appreciation of welding rods for iron. Peer consultations provide a platform for knowledge exchange, where troubleshooting and innovative solutions are shared openly among colleagues. This communal approach to problem-solving instills confidence and trust amongst customers and clients, assuring them of the reliability and commitment a welder brings to every project.
In sum, welding rod iron requires a blend of experience, expertise, authority, and trustworthiness. Using the right equipment and techniques can lead to superior outcomes, reinforcing the welders' craftsmanship that stands the test of time. This continuous cycle of learning and adapting is what enriches the welder’s journey, elevating their craft to an art form grounded in science and skill.