Understanding the diverse types of welding electrodes is crucial for ensuring high-quality performance and longevity of welded materials. Welders must choose the right electrode to align with specific applications across various industries, from construction and automotive to aerospace and manufacturing. In this comprehensive guide, we delve into four primary types of welding electrodes, focusing on their composition, applications, advantages, and technical characteristics to provide a better understanding for industry professionals.
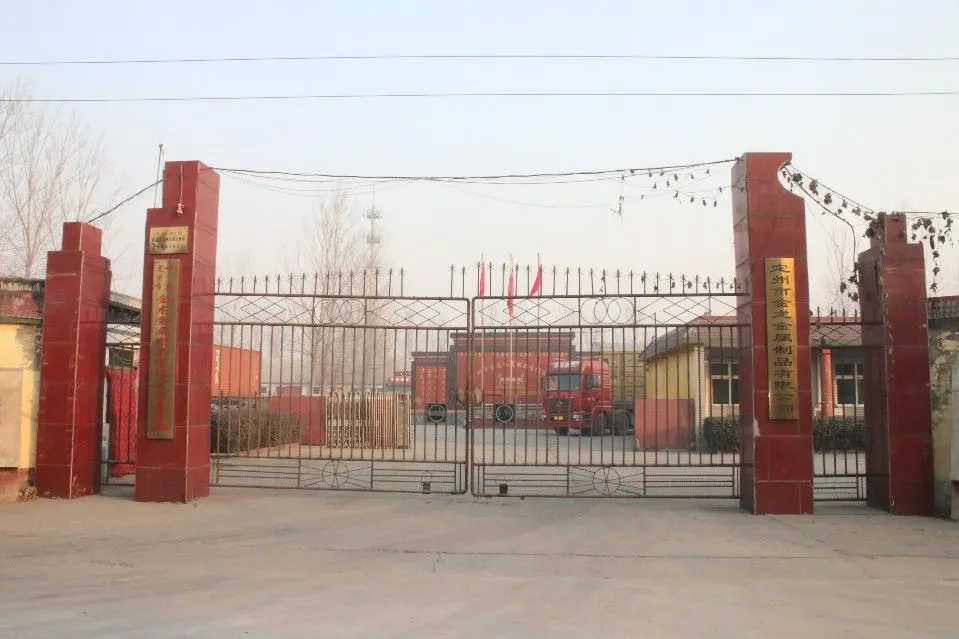
1. Consumable Electrodes
Consumable electrodes are integral to processes like Shielded Metal Arc Welding (SMAW) and Gas Metal Arc Welding (GMAW). These electrodes melt and become a part of the weld itself, providing added material to the joint. E6010 and E7018 are popular types, each offering distinct advantages. E6010 electrodes are known for deep penetration and are commonly used in pipe welding, delivering superior results on rusty or dirty surfaces. Conversely, E7018 electrodes provide a smoother arc and are suited for structural welding jobs due to their high tensile strength of 70,000 psi.
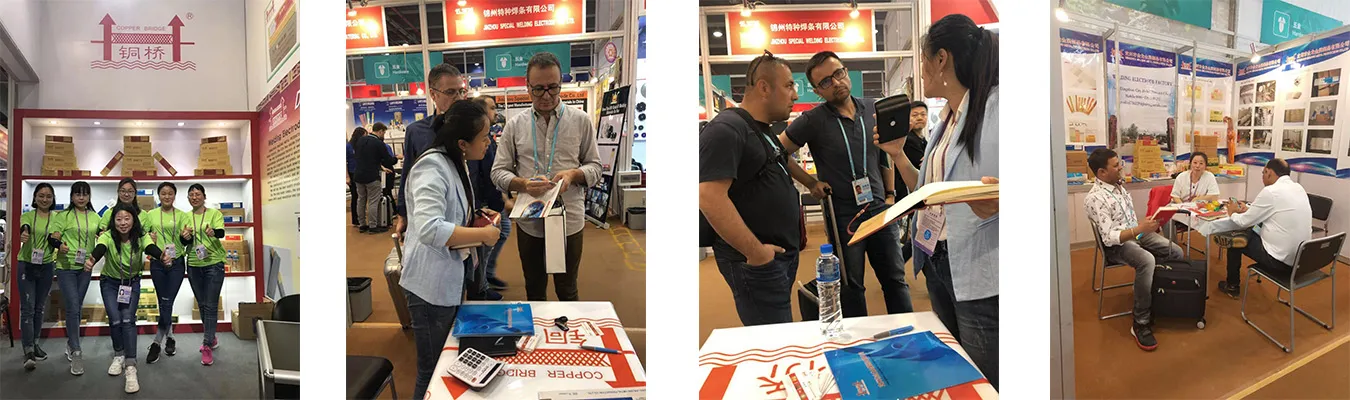
2. Non-Consumable Electrodes
Non-consumable electrodes like Tungsten electrodes used in Gas Tungsten Arc Welding (GTAW) do not melt during the welding process. Instead, they provide a path for the welding current that generates the heat necessary to melt and fuse the metals. Tungsten electrodes are lauded for their heat resistance and electrical conductivity, allowing for precise and high-quality welds especially in critical applications such as aerospace where precision is paramount.
3. Covered Electrodes
types of welding electrodes pdf
Also known as coated electrodes, covered electrodes feature a flux coating that provides shielding from contamination and improves arc stability. The composition of the coating varies, influencing factors like slag formation, deposition rate, and current carrying capacity. Rutile, basic, and cellulose are common types of coatings, each preferred for different welding conditions. For instance, rutile coatings promote easy handling and excellent surface finish, making them ideal for general structural work. Understanding the specific requirements of a welding job is essential to selecting the appropriate covered electrode.
4. Bare Electrodes
Used mostly in submerged arc welding (SAW), bare electrodes lack a coating and rely on a separate flux to protect the weld pool. These electrodes are characterized by high deposition rates and are typically used in automatic or semi-automatic systems for welding thick plates and longitudinal seams in pipelines. The absence of a coating allows for cleaner welds and minimal spatter, crucial for large-scale industrial applications.
In selecting the appropriate welding electrode, factors such as material type, position, current type, and strength requirements should be given priority. Additionally, operational considerations such as ease of use, welding position, and environmental conditions must be factored into the decision-making process. Consulting with welding experts and leveraging data sheets can help ensure the choice of electrode aligns with the desired outcomes of weld quality and durability.
Staying updated with the latest developments and trends in electrode technology can further enhance welding applications. Advanced coatings and composites are continually being developed to meet evolving industry needs for efficiency and performance. Ensuring consistent quality control and adherence to standardized testing protocols enhances trustworthiness and reliability in welded structures.
By selecting the appropriate type and understanding the underlying advantages of each welding electrode, professionals can enhance the quality and integrity of their welds, contributing positively to the project's overall success and longevity.