Stainless steel welding rods are a critical component in the toolbox of professional welders and DIY enthusiasts alike. Their unique properties offer advantages that are indispensable in joining metals with precision and durability. These rods come in various types, each tailored to suit different welding tasks, and understanding their specific applications can greatly enhance both the quality and longevity of the resulting welds.
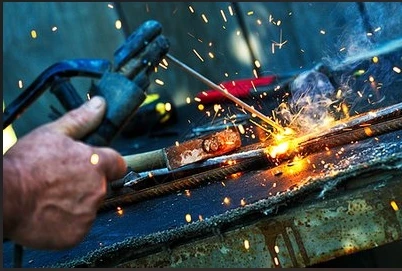
The first consideration when selecting a stainless steel welding rod is the type of stainless steel being used. Stainless steels are generally categorized into austenitic, ferritic, martensitic, duplex, and precipitation-hardening grades, each with distinct properties. Austenitic stainless steel, for example, is known for its excellent corrosion resistance and formability. Rods such as the E308L or E309L are typical choices when working with this type of steel, offering low carbon content to combat carbide precipitation during the welding process.
For those dealing with ferritic or martensitic stainless steels, rods like the E410 are more suitable. These rods provide good resistance to heat and oxidation, ideal for high-temperature applications. Understanding the specific properties of stainless steel grades ensures that the welding rods used will produce welds that stand the test of time, resisting corrosion and structural failure.
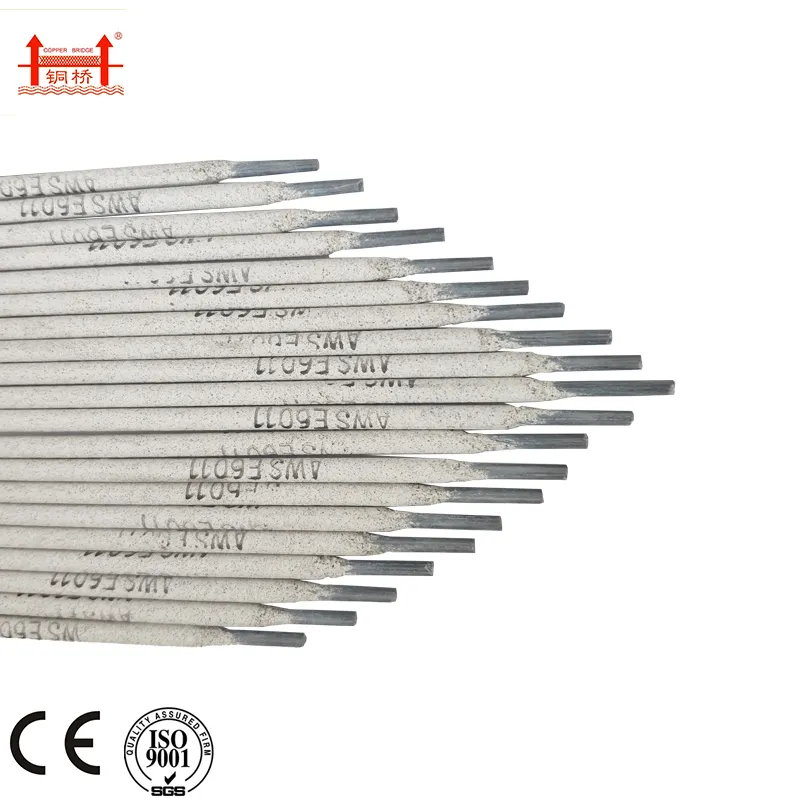
The environment in which the welding is performed also plays a crucial role in rod selection. For outdoor projects exposed to the elements, using a stainless steel welding rod that offers superior resistance to moisture and salt spray is essential. This is where rods with additional alloying elements, such as molybdenum, come in handy. They enhance resistance to chloride-induced pitting, a common form of corrosion in marine environments.
A crucial factor when welding with stainless steel rods is ensuring that proper techniques are employed. For instance, maintaining a short arc and using a suitable angle while welding can minimize heat input, reducing distortion and stress corrosion. The approach to welding should also consider the thickness of the materials being joined; thicker materials might require a multi-pass welding technique to ensure a strong, reliable bond.
Moreover, the choice of welding process, whether it be Shielded Metal Arc Welding (SMAW), Gas Tungsten Arc Welding (GTAW), or Gas Metal Arc Welding (GMAW), impacts the type of rod best suited for the job. Each method has its pros and cons, depending on the specific requirements of the project. SMAW, for instance, is versatile and suitable for outdoor use, while GTAW offers precision, making it ideal for welding thin materials or intricate projects.
ss welding rod
Safety and reliability are non-negotiable in welding operations. Consequently, the quality of the stainless steel welding rods used cannot be overlooked. Opting for rods from reputable manufacturers that meet industry standards ensures not only high-performance outcomes but also safety for the welder. Inferior quality rods can lead to weld defects such as cracking, porosity, or lack of fusion, posing significant structural risks.
In addition to selecting the right rod, pre-welding and post-welding practices are vital. Pre-welding preparation, like cleaning and properly aligning the weld area, reduces contamination risks. Post-welding treatment, such as passivation, helps remove any surface defects and restores the corrosion resistance of the stainless steel.
Additionally, keeping abreast of the latest advancements in welding technologies and materials is essential for any professional welder. Continuous professional development and training ensure that welders are equipped with cutting-edge techniques and knowledge, leveraging advancements in welding rod formulations and applications.
Customer feedback and case studies are valuable resources to gauge the performance of different types of stainless steel welding rods in real-world conditions. These insights can guide choices, reinforcing trust and authority in selecting the best rod for any given application.
Ultimately, the selection and use of stainless steel welding rods are a blend of science and art. Attention to detail, adherence to best practices, and a commitment to quality are the cornerstones of successful welding projects. Whether it is for constructing a towering skyscraper or fabricating a piece of art, the right rod ensures that welds are not just joints but enduring bonds that last a lifetime.