Welding rods, also known as filler metals, play an essential role in the welding process. They come in various sizes and are crucial for ensuring the integrity and strength of welds. Understanding the differences in welding rod sizes is paramount for any welding project, whether for industrial applications, automotive repairs, or small DIY tasks at home.
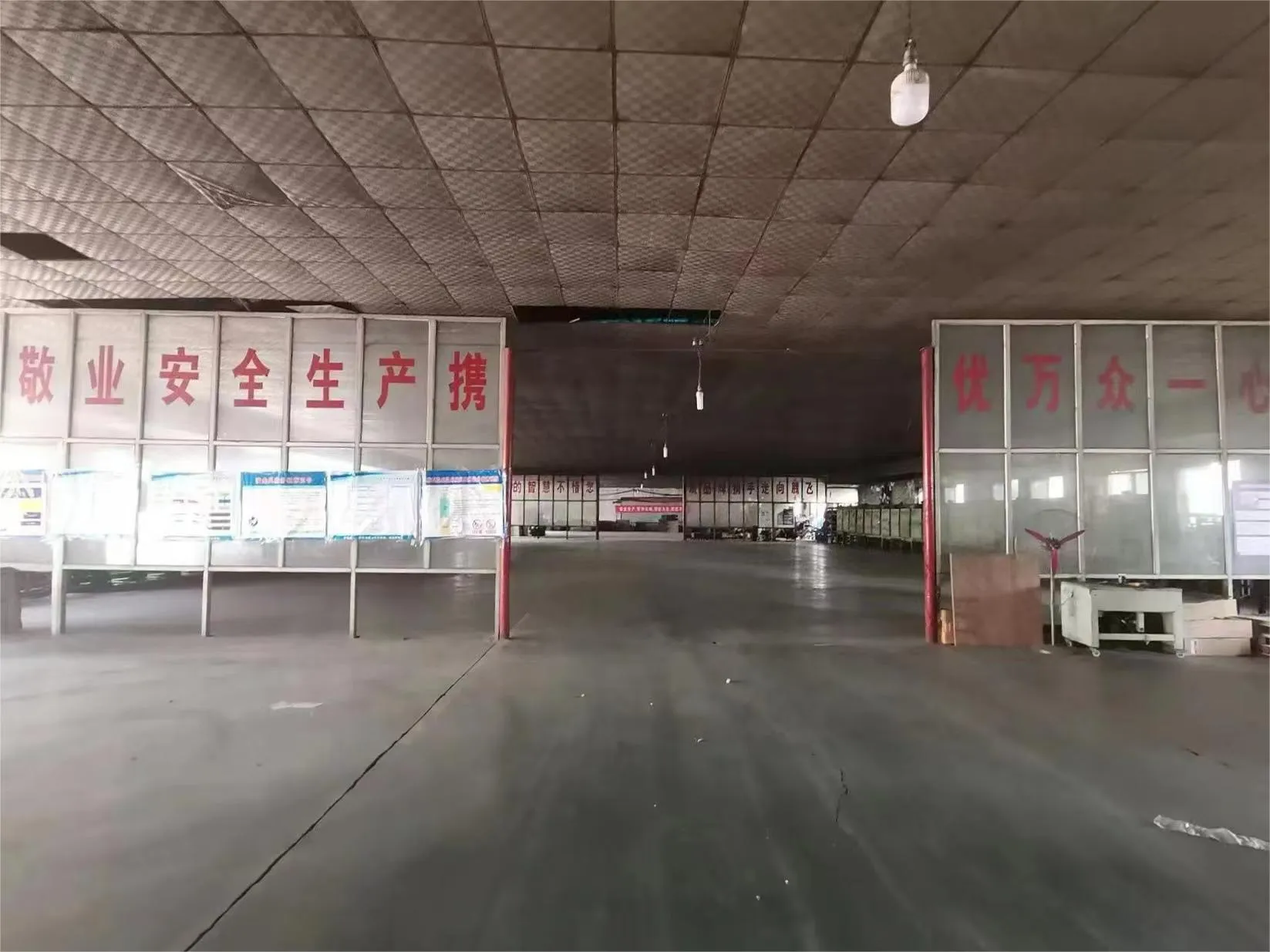
The diameter of a welding rod is one of its most distinguishing features and affects the amperage setting, penetration, and strength of the weld. Common diameters include 1/16 inch, 5/64 inch, 3/32 inch, 1/8 inch, 5/32 inch, and 3/16 inch. Each of these sizes has its specific uses and is chosen based on the thickness of the material being welded and the type of joint.
For thin materials, usually those less than 1/8 inch thick, welding rods of smaller diameters such as 1/16 inch or 3/32 inch are preferred. These smaller rods require lower amperages, which helps prevent burn-through and ensures a more precise weld on thinner materials. This is particularly crucial in work that demands precision, such as automotive body repairs, sheet metal application, or artistic metalworking.
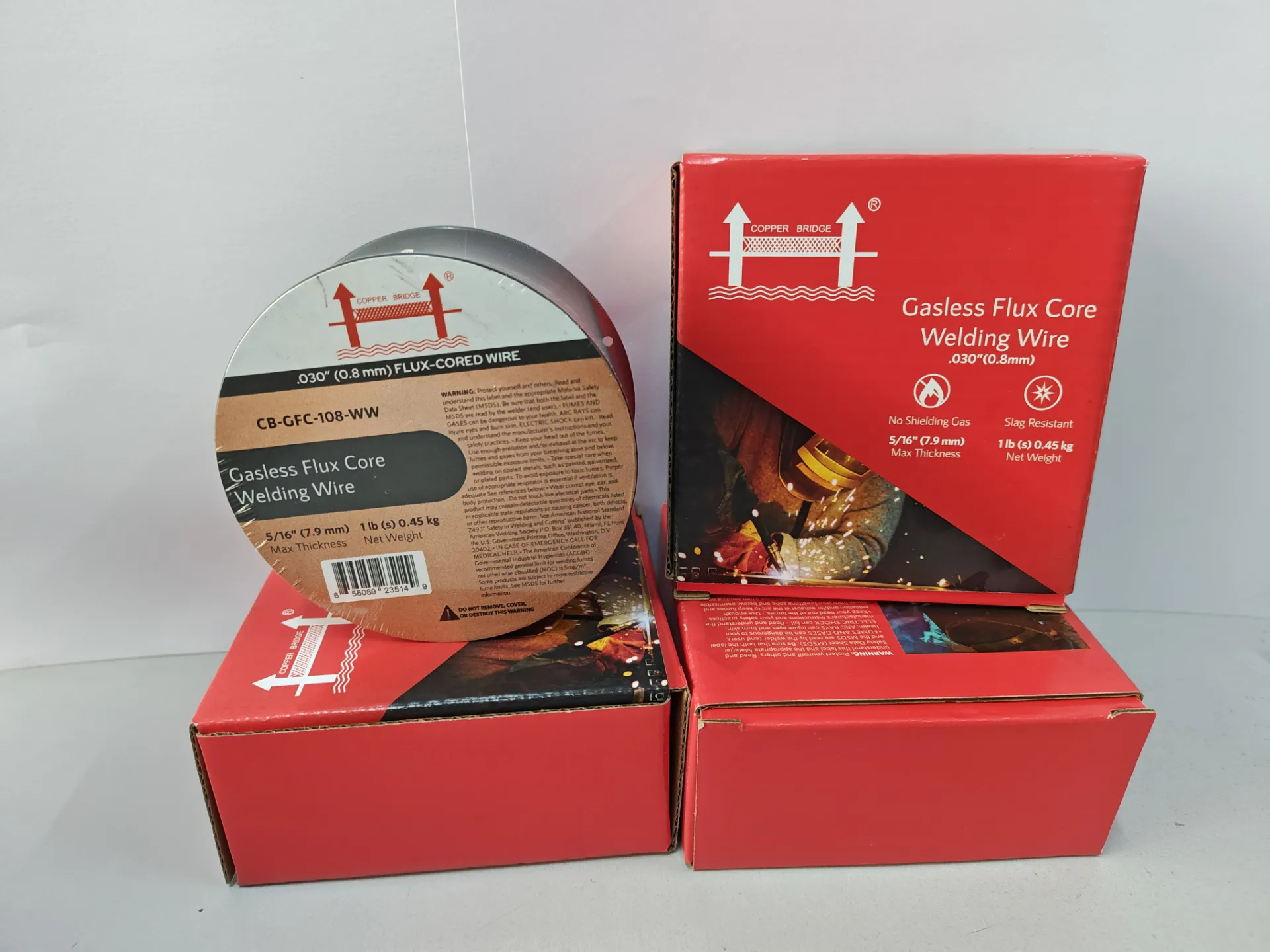
On the other hand, thicker materials, exceeding ¼ inch, are better suited for larger diameter rods like 1/8 inch, 5/32 inch or even 3/16 inch. These rods can handle higher amperage settings, providing deeper penetration and strong welds required for structural joints or heavy-duty fabrication. Construction projects and shipbuilding often rely on these larger rod sizes for their durability and robustness.
Choosing the correct rod size is also influenced by the welding position—flat, horizontal, vertical, or overhead. Larger rods tend to be less effective for out-of-position welding due to their weight and fluidity at higher amperages, which can lead to gravity-related defects. In these cases, opting for a slightly smaller rod can provide better control and quality.
sizes of welding rods
The material composition of the welding rod also affects its usability and performance. Typical compositions include mild steel, stainless steel, and aluminum, each offering different tensile strengths, corrosion resistance, and compatibility with various base metals. The American Welding Society (AWS) classification helps identify these rods, with details such as the tensile strength, flux coating, and rods' usability in welding positions indicated by the numbering system.
In addition to the rod's diameter and composition, the type of welding process—stick welding, MIG, or TIG—also governs rod selection. Specifically, stick welding often requires flux-coated rods, whereas MIG welding uses continuous wire on spools requiring compatibility on both fronts to achieve desired results.
For welders striving for efficacy and efficiency, maintaining a stock of various rod sizes can cater to diverse project needs. Coupled with proper storage to protect them from moisture and contaminants, this ensures longevity and optimal performance in every weld.
Equipping oneself with the knowledge about welding rod sizes not only improves the quality of the finished product but also enhances the safety and satisfaction of working with metals. Mastery in selecting the right rod size embodies expertise and trustworthiness, qualities that are highly regarded in the field of welding.