Exploring the Benefits and Applications of E316 16 Welding Rods
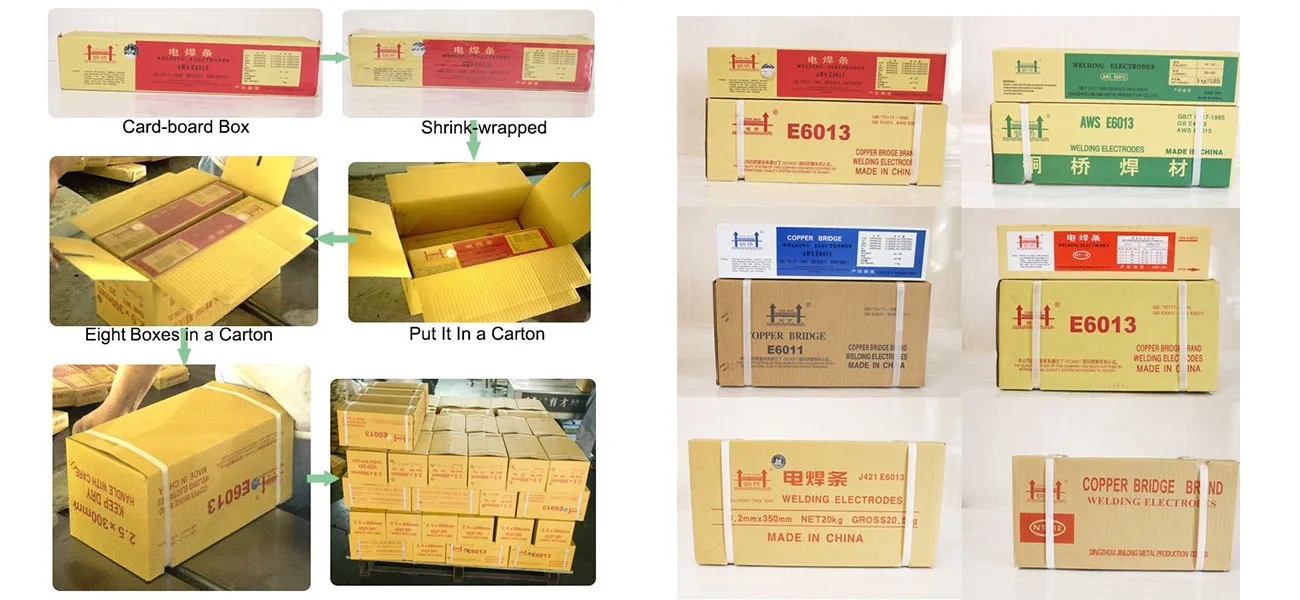
When dealing with critical welding jobs that demand durability and corrosion resistance, E316 16 welding rods are often the go-to choice for professionals across various industries. Renowned for their exceptional performance in diverse conditions, these rods are crafted to ensure strong and reliable welding, particularly in environments where exposure to corrosion is a significant concern.
E316 16 welding rods are primarily used for welding molybdenum-bearing austenitic stainless steels, such as Type 316 and 316L. These materials are commonly found in industries that handle aggressive substances, including chemical processing, pharmaceutical manufacturing, and marine applications. The rod's unique composition ensures that welded joints maintain high resistance to chemicals and acidic conditions. This feature is essential for equipment longevity and operational efficiency, where seamless performance is critical.
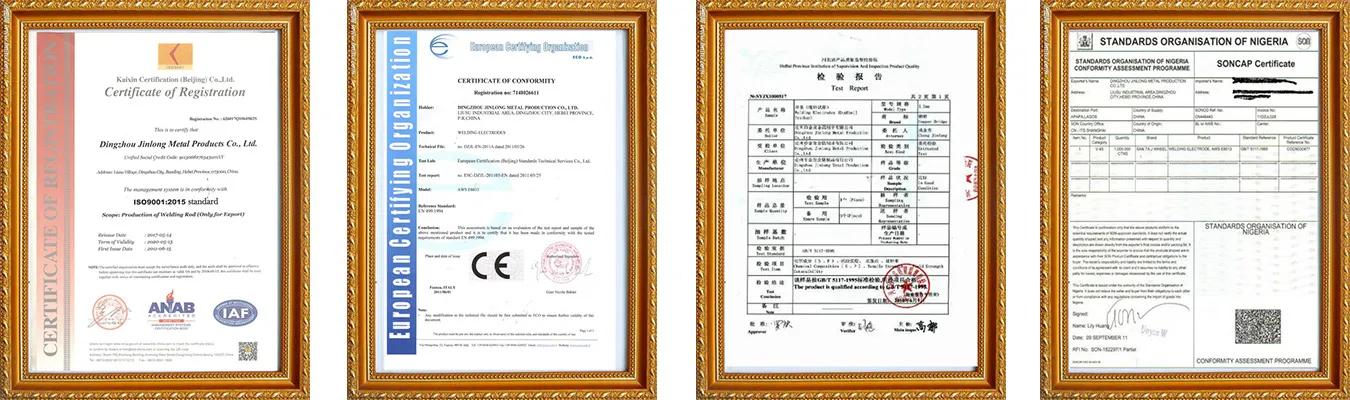
Emphasizing expertise in the field, it's important to note that E316 16 welding rods are specially formulated with a balanced combination of chromium, nickel, and molybdenum. This sophisticated mixture enhances the rod's tensile strength and elongation, making it suitable for high-pressure environments. The molybdenum component, in particular, adds a significant layer of protection against pitting corrosion - a common issue in corrosive environments.
e316 16 welding rod
From a professional perspective,
using E316 16 welding rods ensures reliability and consistency. Welders with experience working with these rods frequently highlight the ease of use, characterized by a smooth arc and minimal spatter. These features not only expedite the welding process but also reduce the need for extensive post-weld clean-up, saving time and resources. Expert welders often recommend maintaining optimal temperature control during the welding process to preserve the mechanical properties of both the rod and the base metal. This careful attention ensures a robust welded joint free from mechanical imperfections.
Authoritativeness in the welding domain is demonstrated through understanding the practical applications of E316 16 welding rods. These rods are indispensable in fabricating and repairing equipment subjected to high temperatures and chemical exposure. Industrial boilers, heat exchangers, and desalination plants regularly rely on these rods owing to their superior protective qualities. The assurance that E316 16 rods can withstand extreme conditions provides plant operators and engineers peace of mind, knowing their installations meet industry standards and regulations.
Alongside performance, the trustworthiness of E316 16 welding rods is validated by certification and compliance with international welding standards. This adherence signifies that these rods have been exhaustively tested and approved for use in critical applications, offering assurance to both welders and industry stakeholders. Professionals across the field often seek out manufacturers and suppliers who can provide detailed specifications and usage guidelines, further cementing their confidence in the product's reliability.
In conclusion, E316 16 welding rods represent the pinnacle of durability and corrosion resistance in the welding industry. Whether it's constructing new facilities or repairing existing infrastructure, these rods provide unparalleled performance and safety. Their ability to withstand harsh environmental factors makes them a preferred choice for experts aiming to deliver high-quality workmanship and ensure the longevity of their projects. As industries continue to evolve and demand more from their materials, E316 16 welding rods remain a vital tool in the arsenal of professional welders committed to excellence.