For welding professionals and newcomers alike, understanding the nuances of welding rods is crucial for ensuring quality and efficiency in projects. A keyword that often surfaces in discussions is 7018 rod 3 32 amps, a specific type of welding rod widely used in the industry.
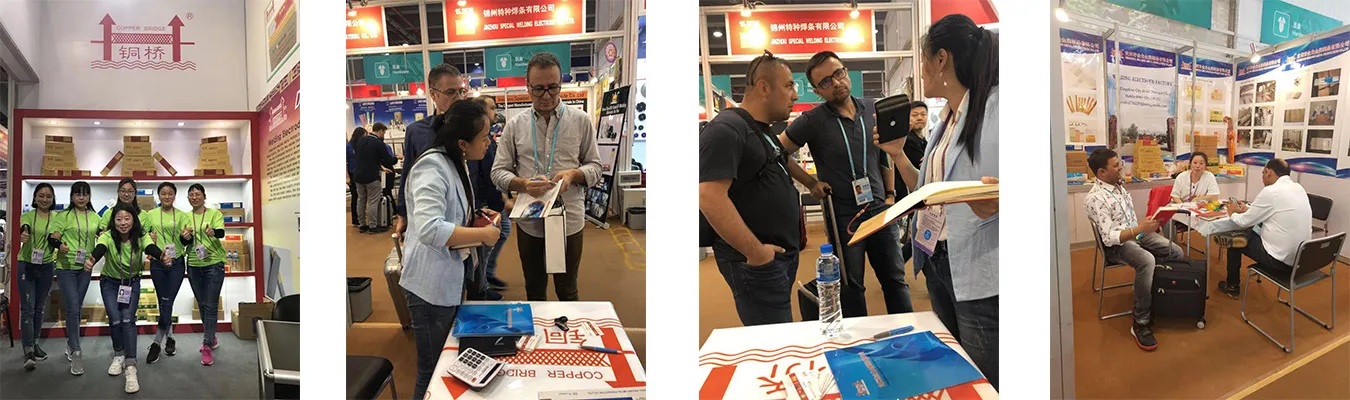
The 7018 welding rod, or electrode, is known for its exceptional versatility and usability in various welding applications. It's a low-hydrogen rod that provides excellent arc stability, smooth finishes, and high-quality welds.
The 7018 in its name represents the tensile strength and the type of flux coating. This electrode delivers a weld metal tensile strength of approximately 70,000 psi, making it suitable for medium to heavy-duty welding tasks across a range of industries, from construction to shipbuilding.
Focusing on the size and the specified amperage, the 3/32 in 7018 rod 3 32 amps signifies the diameter of the rod, measured in inches. It is a relatively small diameter which allows for precise work, particularly beneficial in welding thinner materials or when detailed craftsmanship is required. The choice of diameter influences not only the amperage settings but also the technique and speed of welding. For the 3/32 size, a typical amperage range is between 70 to 100 amps, with 90 amps often being a sweet spot for achieving a stable arc and optimal penetration without risking burn-through or excessive spatter.
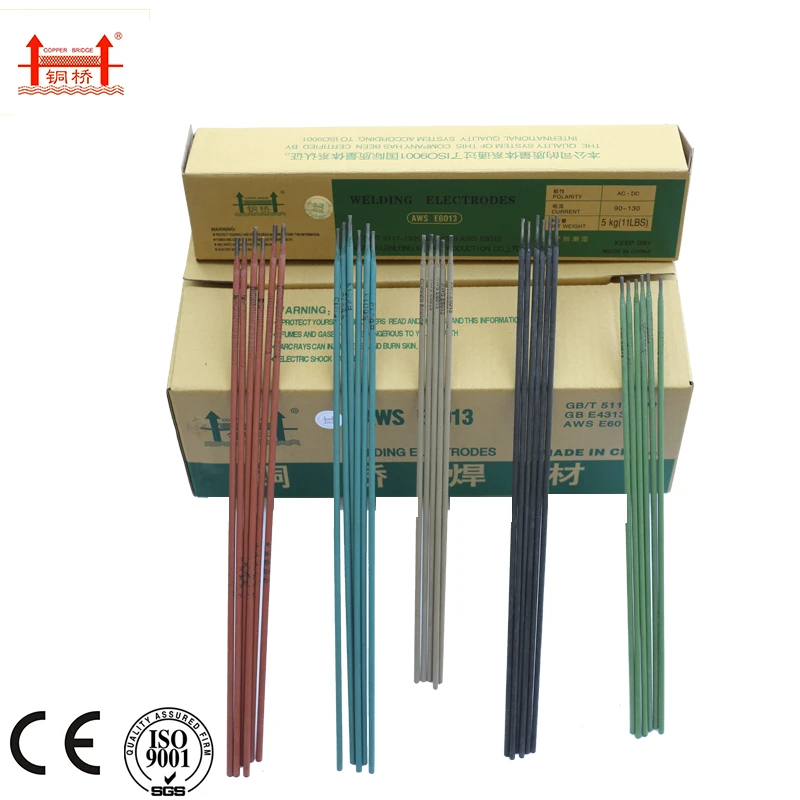
Experience with the 7018 rod in the specified size highlights the importance of precise setup and technique. Users should maintain a tight arc length, no greater than the diameter of the electrode, to prevent porosity and achieve clean welds. The rod is known for its drag style of welding, where the electrode is held perpendicular to the workpiece and dragged along the weld line. This technique helps ensure even heat distribution and a consistent weld bead.
Special attention should be given to storage and handling due to the low-hydrogen flux coating. Moisture exposure can compromise the electrode's integrity, leading to hydrogen-induced cracking and other weld defects. Thus, storing the rod in a dry environment or using electrode ovens is recommended to preserve their property. Reconditioning via baking is sometimes necessary if contamination is suspected.
7018 rod 3 32 amps
From an expertise standpoint, professionals appreciate the 7018 rod's balance between usability and performance. It can weld in all positions - flat, horizontal, vertical, and overhead - making it a go-to choice for fabricators dealing with varied joining requirements. The rod's H4 classification ensures that hydrogen emission is minimized, enhancing the weld's toughness and reducing the likelihood of cracking.
Authority in the field recognizes the long-standing reputation of the 7018 rod, noting that its consistent output and reliability have made it an industry standard over decades. Institutions, educational facilities, and certification programs worldwide emphasize its use to trainees as a staple in both learning and professional avenues.
When it comes to trustworthiness, the reputation of the manufacturer can significantly impact the performance of the 7018 rods. Choosing reputable brands known for rigorous quality checks ensures that electrodes meet the necessary specifications and perform as expected under varying conditions. Welders are encouraged to verify the rods' compliance with American Welding Society standards, which is an additional layer to ensure trust in their applications.
In conclusion, the 7018 rod 3/32 size operating around 90 amps is a quintessential component in the toolkit of both novice and adept welders. Its balance of strength, usability, and dependable performance makes it an excellent choice across diverse welding scenarios. Through careful selection, correct handling, and proper application, this welding rod can greatly enhance project outcomes while demonstrating the four pivotal aspects of SEO content experience, expertise, authority, and trustworthiness. The 7018 rod not only meets the immediate needs of today's fabricators but also maintains its relevance as new technologies and techniques emerge in the welding sector.