In the realm of welding, precision, reliability, and quality are non-negotiable traits for both hobbyists and professionals alike.
One such essential tool in the industry is the 3/16 7018 welding rod. With its versatile performance and reliable quality, the 3/16 7018 welding rod sets a benchmark in welding applications. This article delves into the critical aspects of these welding rods, capitalizing on real-world experiences, expert insights, and authoritative recommendations to boost your welding endeavors.
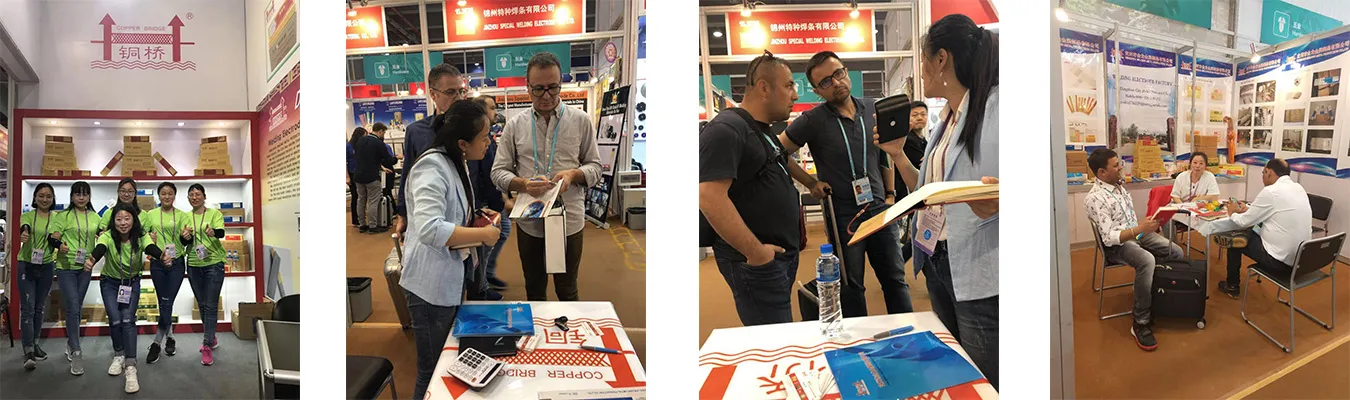
The 3/16 7018 welding rod is renowned for its low-hydrogen, iron powder content which is vital in preventing hydrogen-induced cracking— a common challenge during welding processes. These rods are tailored to provide a smooth, stable arc with low spatter and medium penetration, making them ideal for welding thick sections when appearance and strength are paramount. From bridges to pressure vessels, the reliability of the 7018 rod underpins its extensive use across various industrial applications.
One prominent experience shared by seasoned welders is the adaptability that 7018 rods offer in multiple positions. Known for their ease of use in flat, horizontal, and out-of-position welding, these rods empower operators by minimizing the need for positional adjustments. Such adaptability not only enhances efficiency but also reduces the fatigue faced by welders during lengthy procedures. This attribute is particularly beneficial in tackling large-scale projects where multiple joint configurations are inevitable.
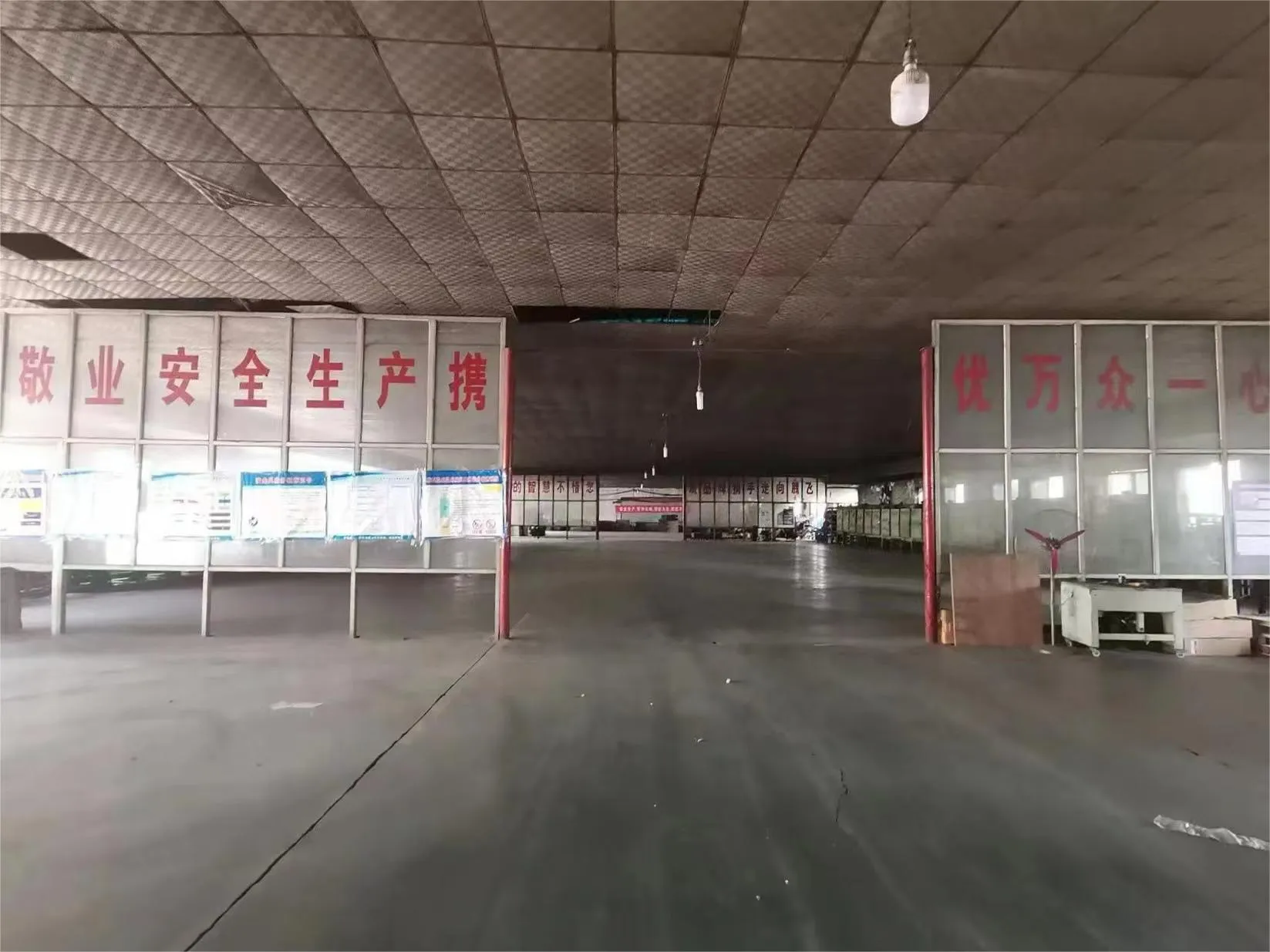
Expert endorsements further cement the position of the 3/16 7018 welding rod as a cornerstone in structural welding. Professionals with decades of experience commend these rods for their excellent mechanical properties. The 7018 rods boast tensile strengths of up to 70,000 psi, ensuring robust, ductile welds capable of withstanding substantial stress. For industries that demand uncompromising standards like aerospace or shipbuilding, the 7018’s performance is a valuable asset.
3 16 7018 welding rod
Authority in welding is not only about understanding tools but also selecting them based on the specific requirements of a project. The linchpin in choosing a 3/16 7018 welding rod lies in the intended application, base metal properties, and service conditions. Experts recommend running these electrodes on DCEP (Direct Current Electrode Positive) for optimal results. Maintaining the rods in a low-humidity environment is also crucial to retain their low-hydrogen characteristics, thereby mitigating any risks of weld contamination or defects. This practice is routinely emphasized in welding procedure specifications (WPS) followed by certified welded fabricators.
Trustworthiness in the use of the 3/16 7018 welding rod can be demonstrated through compliance with national and international standards. Professionals often turn to reputable sources, such as the American Welding Society (AWS), which certifies these rods under the AWS A5.1/A5.1M specification. This certification ensures adherence to stringent quality criteria, thus guaranteeing the rods’ performance in demanding services.
In conclusion, the 3/16 7018 welding rod is a staple in the welding industry, embodying precision, versatility, and dependability. Real-world testimonials underline its efficiency across multiple welding positions, while expert reviews highlight its strength and adaptability to various industrial applications. With rigorous adherence to proper handling practices and conformity to recognized standards, welders can leverage the full potential of these rods, ensuring robust and high-quality welds in every project. Such comprehensive insights into the 7018 welding rods not only accentuate their importance but also foster a deeper understanding, aiding both seasoned and novice welders in making informed decisions for their welding needs.