Selecting the right welding rod for stainless steel is crucial to ensure quality and durability in your welding projects. Stainless steel, known for its corrosion resistance and formability, demands careful material pairing to prevent defects and ensure structural integrity. For both seasoned welders and newcomers venturing into the craft, understanding the nuances of welding rods is key to mastering stainless steel welding.
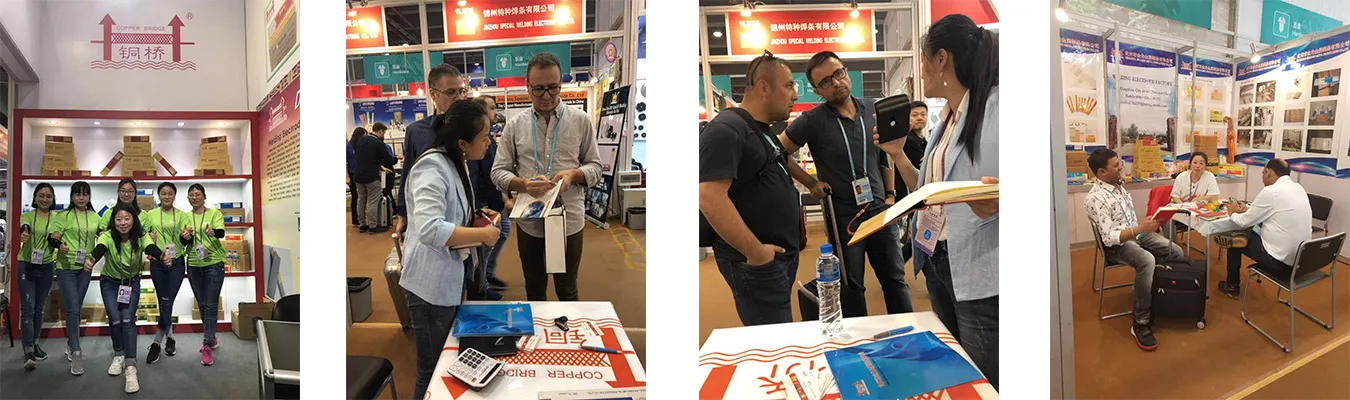
Firstly, it's important to recognize the various types of stainless steel, each classified by its crystal structure austenitic, ferritic, martensitic, duplex, and precipitation hardening. Among these, austenitic stainless steels are the most commonly welded. A typical example is the 300 series (like 304 or 316), which are non-magnetic and known for their high corrosion resistance.
When working with austenitic stainless steels, a prime welding rod recommendation is the E308L-16 or E316L-16. The ‘E’ indicates the electrode, ‘308’ or ‘316’ denotes the type of stainless steel, ‘L’ signifies low carbon content, reducing carbide precipitation, while ‘16’ stands for the type of current and coating. Selecting an E308L-16 rod is perfect for 304 stainless steel, whereas E316L-16 is suited for 316 stainless steel, especially in environments that are highly corrosive like marine applications.
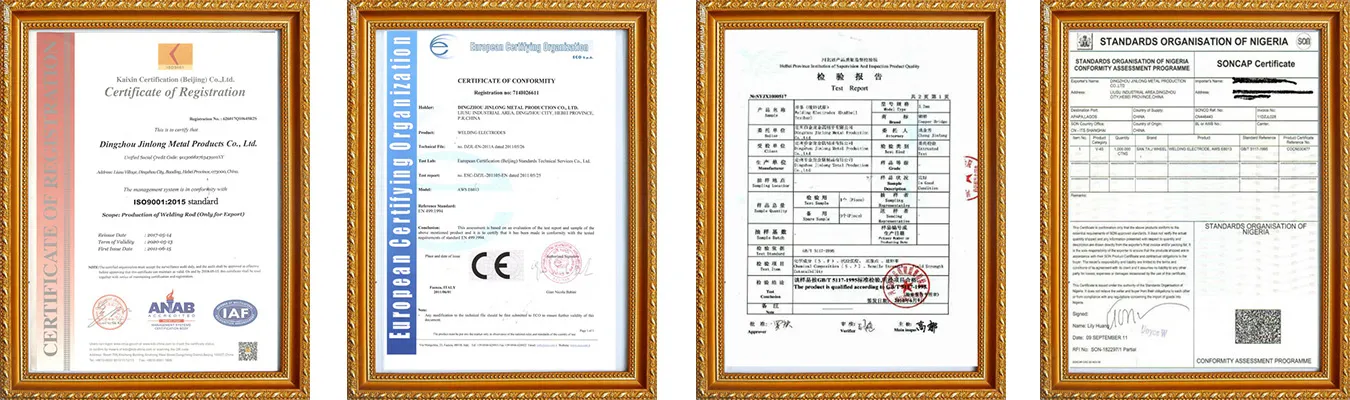
Welding ferritic stainless steels, usually represented by the 400 series (such as 409 or 430), requires different considerations due to their magnetic nature and higher susceptibility to grain growth when exposed to elevated temperatures. An E430 rod is recommended for these types, ensuring that the weld metal matches the corrosion resistance of the base metal and maintains a stable ferritic microstructure.
Martensitic stainless steels, demanding in terms of heat control due to their carbon content, requires electrodes such as E410 or E420. These rods provide a strong, durable weld while maintaining necessary hardness. They are ideal for applications involving wear resistance—think of kitchen knives or turbine blades.
Duplex stainless steels, known for their excellent strength and resistance to stress corrosion, require rods like E2209, matching the duplex nature and delivering a proper mix of ferritic and austenitic phases. This balance ensures that the weld matches the base metal's strength and corrosion resistance, essential in chemical processing or petrochemical industries.
what welding rod for stainless steel
Precipitation hardening stainless steels, characterized by their unique hardening process and exceptional strength, pose challenges in welding because of potential cracking. Here, selecting a rod like the 17-4PH offers compatibility, providing necessary strength while maintaining the integrity of the joint.
Welding with stainless steel electrodes requires consideration of specific parameters like preheat, interpass temperatures, and cooling rates. For instance, overheating can lead to carbide precipitation, depleting chromium from the steel's surface and reducing corrosion resistance—a common challenge for austenitic steels.
Furthermore, practical advice from experienced welders underscores the importance of joint preparation and cleanliness. Stainless steel surfaces should be free from oil, grease, and dust to prevent contamination and ensure a clean weld. Use stainless steel brushes or dedicated stainless steel grinding wheels to avoid transferring contaminants.
Safety is another critical element. Welding stainless steel involves fumes that contain hexavalent chromium, a known carcinogen. Adequate ventilation or respirators are vital to protect yourself from potential health risks during the welding process.
In conclusion,
choosing the correct welding rod for stainless steel is about more than just matching numbers. It requires an understanding of the metal's type, its application environment, and the specifics of the weld process. Drawing insights from seasoned professionals, while applying stringent safety measures, will ensure that each weld is not just a connection of metal but a crafted bond that stands the test of time. Implementing these considerations will not only enhance the quality of your weld but also secure a reputation for reliability and expertise in stainless steel welding.