Selecting the right welding rod for stainless steel is crucial in ensuring a strong, corrosion-resistant weld. Stainless steel welding is frequently employed across industries ranging from automotive manufacturing to the construction of high-end kitchen appliances. Thus, the expertise in selecting the appropriate welding electrode cannot be overstated. Understanding the nuances involved in this selection process can save time, reduce costs, and improve the overall quality of the end product.
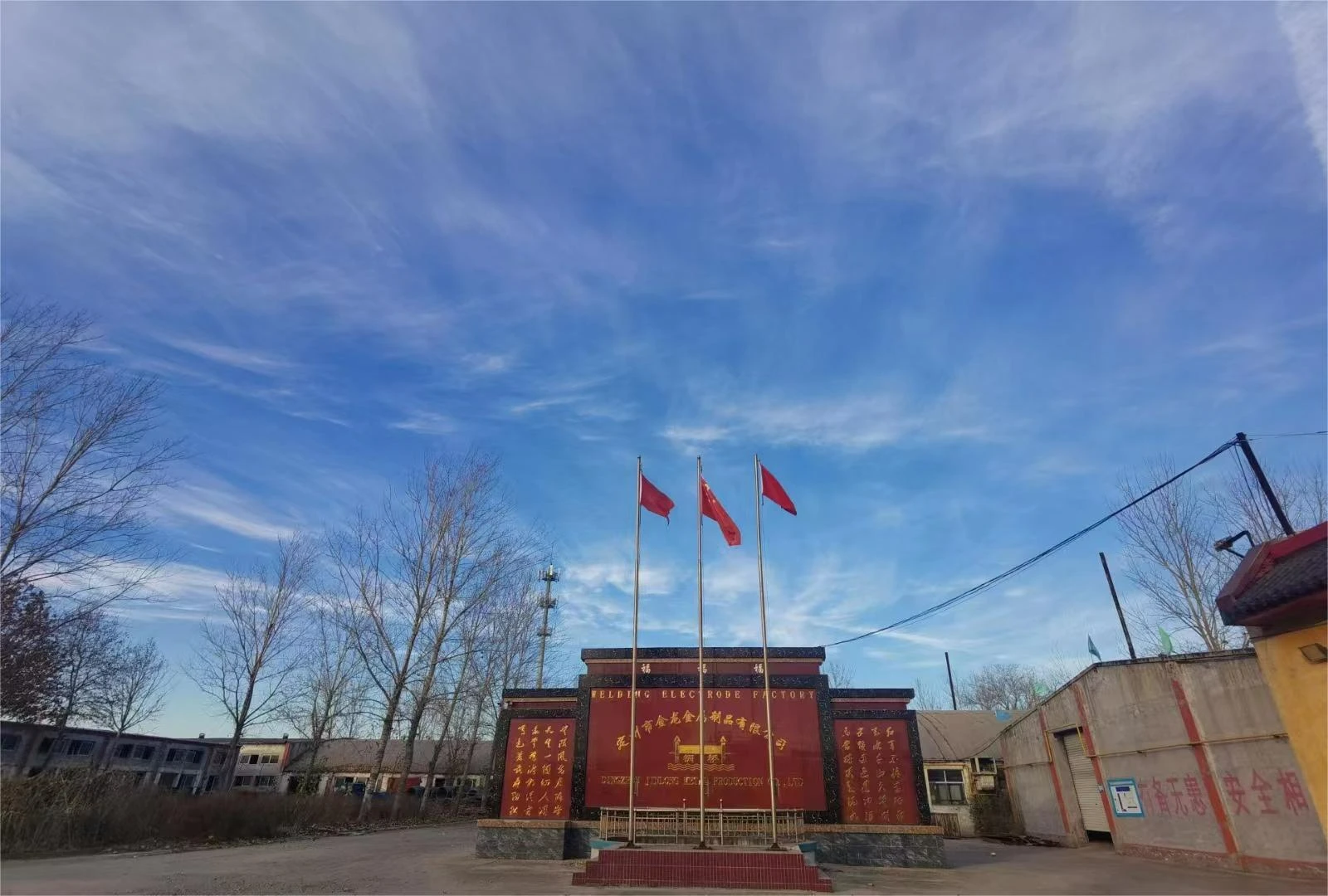
When choosing a welding rod for stainless steel, one must first understand the type of stainless steel involved. Stainless steels come in various grades, each with its own specific considerations. The most commonly used grades are 304, 316, and 308. Each of these grades has different elements that influence corrosion resistance, strength, and weldability. For example, 304 stainless steel is well-suited for general-purpose applications due to its excellent corrosion resistance. In contrast, 316 stainless steel is often used in marine environments due to its enhanced resistance to harsh conditions.
E308L electrodes are commonly used for welding 304 stainless steel, providing a robust and reliable weld. Meanwhile, E316L electrodes are the preferred choice for welding 316 stainless steel, optimized for resistance against chlorides and harsh chemicals. The “L” in these electrode classifications indicates a low carbon content, which is crucial to prevent carbide precipitation and intergranular corrosion during welding. The selection of low-carbon electrodes is especially important in applications where the welded joints will be subjected to high temperatures or corrosive environments.
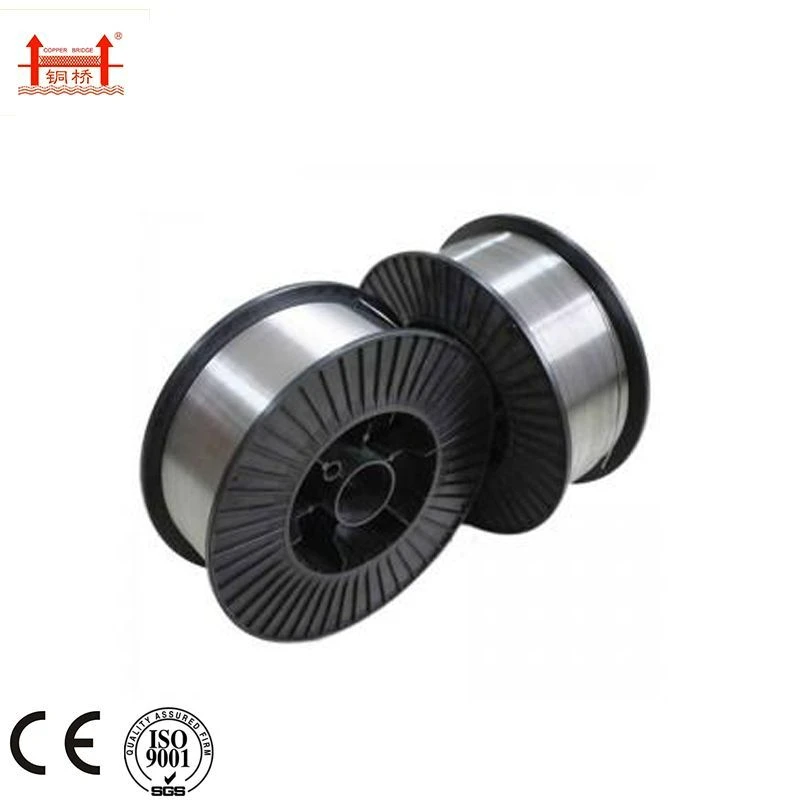
Beyond matching the filler material with the base metal, understanding the welding technique is also vital. While Stick welding (SMAW) is popular due to its simplicity and versatility, Tungsten Inert Gas (TIG) welding is preferred for stainless steel due to its precision and ability to create clean, high-quality welds. TIG welding requires a higher level of skill, but the results often justify the expertise required. Gas Metal Arc Welding (GMAW or MIG) is another viable option, providing high deposition rates, but careful control is needed to manage heat input and avoid distortion.
Within TIG welding, the choice of inert gas also influences the outcome. Argon is the most widely used shielding gas due to its excellent arc stability and cleaning action on the weld pool. For thicker materials, a mix of Argon and Helium can be used to increase heat input and improve penetration. The use of a back-purge gas, typically Argon, is important when welding thin materials to prevent oxidation at the root of the weld.
what welding rod do you use for stainless steel
The expertise in welding stainless steel also extends to proper preparation. Stainless steel surfaces must be meticulously cleaned before welding to remove any contaminants such as oils, rust, or shop dirt. These can introduce contaminants into the weld pool, leading to defects and compromised properties. Specialized cleaning agents or mechanical means like brushing with stainless steel brushes are recommended. Additionally, the application of anti-splatter compounds can protect surrounding areas from weld damage.
For those in industrial settings, quality assurance during the welding process is paramount. Non-destructive testing methods such as X-ray or ultrasonic inspection can detect subsurface defects in the welds. These methods enhance the trustworthiness of the welded components, ensuring compliance with stringent industry standards such as ASTM or ASME codes. Moreover, maintaining certifications for welders, such as those provided by the American Welding Society (AWS), strengthens the credibility and authority of the welding operations.
The choice of equipment and consumables also plays a significant role. Reliable, high-quality welding machines that provide stable current outputs and incorporate advanced features like pulse welding modes support welders in achieving consistent results. The use of premium-grade electrodes and filler materials, often verified through certifications and testing, further guarantees the weld's integrity.
In conclusion, the selection of the appropriate welding rod for stainless steel is a multi-faceted process that demands a comprehensive understanding of the materials, methods, and equipment involved. By honing this expertise, professionals can ensure the longevity and performance of welded structures, maintaining their status as authoritative figures in the welding industry.